Introduction
Corrosion, wear and fracture are some of the main damage suffered by mild steel, which has resulted in its components degradation and lower durability. These have been major concerns in various industrial set-ups 1-3. Surface modifications via composite coatings have been widely utilized to improve mild steel properties for advanced and sophisticated applications 4),( 5). The preference for mild steel coating through electrodeposition technique over other surface modification methods is due to its bonding efficiency, cost effectiveness, fine texture and good thickness ratio 6. Cobalt (Co), Ni and Zinc (Zn) mono coatings have been used to be deposited on mild steel 7. However, multiple failures were reported, due to their low durability in high corrosive and intensely abrasive environments 8-10. These challenges have been addressed by employing composite deposition as an alternative for improving the mono coatings properties 11-13.
Steel surface coating with particles from the oxidation of metals, ceramic and polymers has effectively provided substantial tribological properties and good oxidation stability 14-17. Electrodeposition of composites, such as ZnO (zinc oxide), Al2O3 (aluminum oxide), Cr2O3 (chromium oxide), TiO2 (titanium dioxide), Al6O13, SiC (silicon carbid), WC (tungsten carbide) and Cr3C2 (chromium carbide), have proved effective to a certain degree 18,19. However, the search for better materials, to obtain mechanical, tribological, corrosion resistance and surface morphology optimization, continues 20-22. Improved metals surface morphology has been achieved by ensuring the particles homogenous distribution through their continued agitation, to avoid their agglomeration. Other processing parameters might as well affect the metals coating morphology 23. This work has investigated the effect of Ni-SiO2, Ni-SiO2- C6H5N3, Ni-Al2SiO5 and Ni-Al2SiO5-10C6H5N3 composite films on mild steel corrosion resistance in a 0.5 M HCl solution, via linear potentiodynamic polarization technique. The samples micro-hardness, wear resistance and surface morphologies were investigated to establish their performance.
Experimental procedure substrates preparation
Mild steel commercially sourced was cut into coupons, with the dimensions of 45 mm x 25 mm x 2mm, and used as cathode, while a 99% Ni plate, with the dimensions of 50 mm x 30 mm x 2 mm, was the anode. The mild steel samples surfaces were cleaned with emery papers, and submerged in sodium carbonate for 10 s, to remove rusty particles from them. The mild steel samples were then pickled and activated with 10% HCl, at room temperature, for 10 s. The pickled mild steel samples were instantly rinsed in distilled water. The mild steel chemical composition used for this experiment is shown in Table 1.
Table 1 Mild steel composition (wt%).
Element | C | Mn | Si | P | S | Al | Ni | Fe |
Composition | 0.15 | 0.452 | 0.181 | 0.011 | 0.0312 | 0.0051 | 0.007 | Balance |
Coating bath preparation
Table 2 shows the bath formulation for Ni-30SiO2 and Ni-30SiO2-10C6H5N3 coating, while Table 3 shows the bath formulation for Ni-30Al2SiO5 and Ni-30Al2SiO5-20C6H5N3 coating. The reagents and particles were dissolved in distilled water, and left for 48 h, maintaining a constant pH value, and temperatures of 5.0 and 45 ºC, respectively.
Electrodeposition process
During the electrodeposition process, mild steel was positioned at an equivalent distance of 3 cm between two nickel plates. The plating bath was continuously stirred at 250 rpm, and a constant temperature of 45 oC was maintained throughout the coating process. The constant stirring ensured the particles stable suspension, and reduced their sticking tendency. The charge particle electrophoresis mobility in the solution was enhanced, due to the minimal particles agglomeration 24. Constant agitation aided the particles mass transfer, and also enhanced deposition quality. However, inordinate agitation could be detrimental to the electrodes stability, affecting the charge transfer region and, consequently, reducing the deposition quality 25.
Samples characterization
The coated samples thicknesses were measured using an Elcometer microthickness meter gauge (Elcometer 456 Model). with the accuracy of ±1%. The uncoated and coated samples corrosion resistances were examined using a potentiodynamic polarization technique that utilizes a three-electrode cell system in 0.5 M HCl, at an ambient temperature of 25 oC. The contact and reference electrode were the graphite rod and Ag/AgCl, respectively. Tafel curves were generated from -1.5 to 1.5 V, at a 0.005 V/s scan rate. The test samples wear and hardness were investigated using a CERT UMT-2 multi-functional tribological testing and a high diamond pyramid indentation, respectively. The samples wear characterizations were carried out at a room temperature of 25 oC, using a load of 10 N, at a constant speed of 5 mm/s and a displacement amplitude of 2 mm, for 20 min, on the reciprocating sliding tester. A silicon nitride (Si3N4) ball, with the diameter of 4 mm and mass of 50 g, was used as the counter body, for examining the sample wear behavior. More so, the test samples morphologies were examined using a high resolution optical microscopy, at 10 X magnification. The test samples heattreatment was carried out in a vacuum, at 400 ºC, for 1 h.
Results and discussion
Coating thickness and estimation of coating per unit area
Table 4 shows the average thickness obtained from the samples thickness measurement at different points. The coating per unit area (mg/mm2) was calculated using equation 1 or 2.
where w, L, T and B are the samples weight gain, length, thickness and breadth, respectively, and A is their coated area.
Linear potentiodynamic polarization
The coated test samples linear potentiodynamic polarization examination showed that they had lower corrosion resistance, in the 0.5 M HCl solution, than that of the control sample. Table 5 and Fig. 1 show the summary of the potentiodynamic polarization results and the Tafel plot, respectively.
In Table 5, it can be seen that the Ni-30SiO2-10C6H5N3 coated sample exhibited a lower corrosion rate (Ecorr) that that of the Ni-30SiO2 coated sample. Similarly, the Ni-30Al2SiO5-10C6H5N3 coated sample was found to possess a lower Ecorr than that of the Ni-30Al2SiO5 coated samples. This shows that the 1H-benzotriazole (10C6H5N3) addition further hindered the mild steel active sites attack by the Cl- ion.
More so, the lowest current density (jcorr) and highest degree of polarization resistance (Rp), recorded for the Ni-30Al2SiO5-10C6H5N3 coated sample, could be attributed to the synergetic effect of both Al2SiO5 and 10C6H5N3, and to their adhesiveness on mild steel 26. The Tafel plot in Fig. 1 revealed the particulates mixed inhibitory effect. This was confirmed by the Ecorr values closeness.
Samples microhardness analysis
Fig. 2 shows the micro-hardness values of heat-treated and unheated samples.
These values were obtained using the Vickers hardness technique, with the aid of high diamond pyramid indentation (EMCO Test Dura-scan), at a test load of 10 g, for 20 s.
Indentations were carried out across the mild steel samples surfaces, at an interval of 20 μm. Vickers micro hardness values were computed using the applied load, and the average diagonal of the impression created on the test samples. The micro-hardness of all the samples increased after the heat-treatment, which shows that it improved the particles adhesion kinetics 27. Considering the unheated samples, the uncoated mild steel micro-hardness was raised from 60 to 94 kgf/mm2, with 30g SiO2, and further increased to 108 kgf/mm2, with 10g C6H5N3 particles. A similar increase was noticed with Ni-30Al2SiO5 and Ni-30Al2SiO5-10C6H5N3 coated samples. The increment in micro-hardness could be attributed to the increase in the stain energy of the matrix alloy, as a result of the particles addition 28.
Samples wear behavior
Fig. 3 shows the comparative test samples wear loss.
The uncoated sample exhibited lower wear resistance than that of the coated sample, because the intermolecular bonds within the mild steel were easily distorted, resulting in the material wearing at a faster rate 16. The wear resistance was found to increase after the heat-treatment. The coated sample higher wear resistance indicates that the particulates acted as a load bearing component and building block against the counter body. Ni-30Al2SiO5- 10C6H5N3 and Ni-30Al2SiO5 coated samples suffered lower wear loss than that of the other samples, which could result from the load bearing capacity of the hard Al2SiO5 and from the good bonding between the particles and the matrix.
This, consequently, minimizes the particles pull out. More so, the coating mass particles concentration, size and homogenous distribution could have increased the anti-wear action that results from the elemental stability between mild steel and Al2SiO58,11.
Morphology of the unheated and heat-treated samples
Figs. 4a-e shows the high resolution optical microscopy micrographs of the unheated coated and uncoated samples.
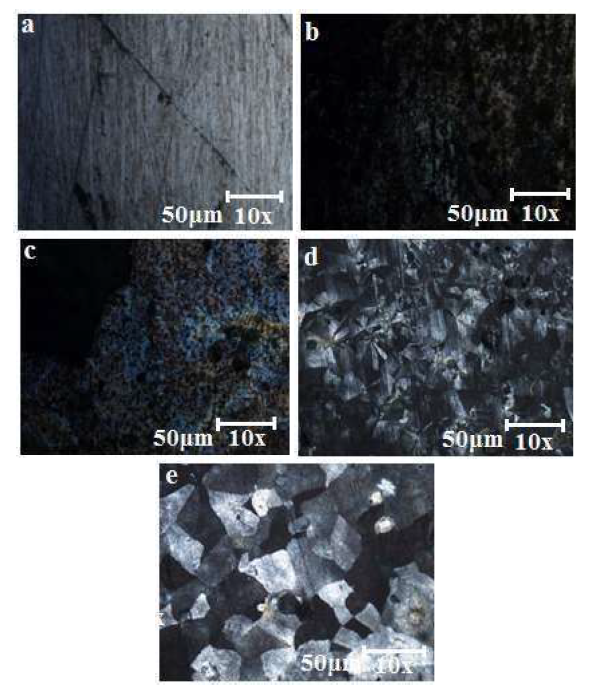
Figure 4 Micrographs of mild steel: (a) uncoated; (b) Ni-30SiO2 coated; (c) Ni-30SiO2-10C6H5N3 coated; (d) Ni-30Al2SiO5 coated and; (e) Ni-30Al2SiO5-10C6H5N3 coated.
Expectedly, the micrograph of the uncoated mild steel surface exhibited rough morphology and initiation of pitting corrosion 29,30. Fig. 4b-e shows the growth of several crystals on the mild steel surface, without defects and minimal porosity. Figs. 4b and 4c appear darker and smoother, signifying the presence of similar particles in the coated samples. However, Figs. 4d and 4e exhibit a unique flakelike crystalline structure at the mild steel surface. This could be linked to the Al2SiO5 nanoparticles inclusion and uniform dispersion in the Ni matrix, which resulted in the generation of more nucleation sites, and minimized the crystal growth, leading to the development of nano-sized grains 31-33. The synergy between Al2SiO5 and the whitish C6H5N3 could have been the reason for the double phases displayed by the micrograph in Fig. 4e, which represents the Ni- 30Al2SiO5-10C6H5N3 coated sample 34. However, it possesses a brighter and smoother morphology than that of the other samples.
The high resolution optical microscopy micrographs of the heat-treated samples are shown in Figs. 5a-e.
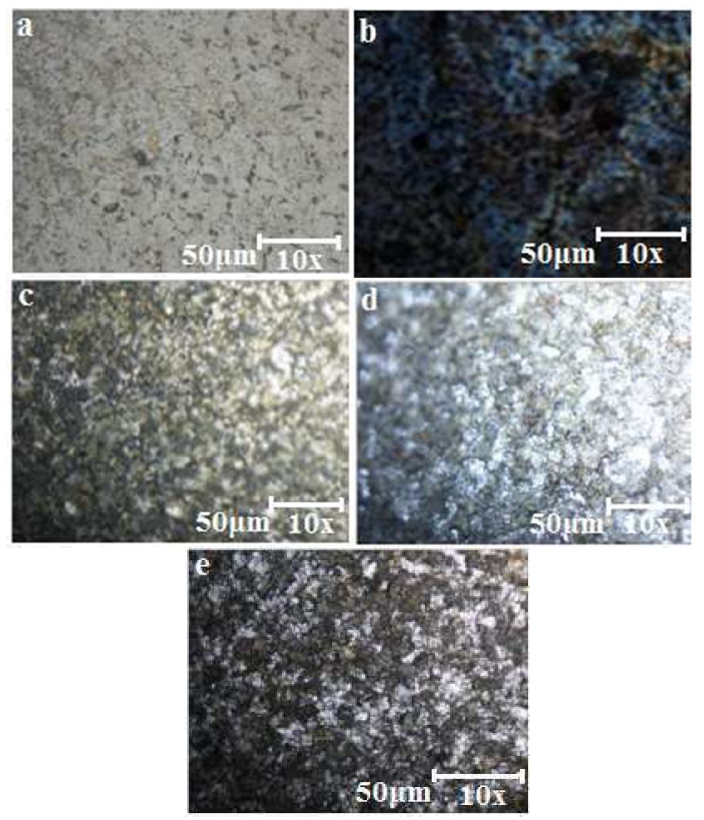
Figure 5 Micrographs of heat-treated mild steel: (a) uncoated; (b) Ni-30SiO2 coated; (c) Ni-30SiO2-10C6H5N3 coated; (d) Ni-30Al2SiO5 coated and; (e) Ni-30Al2SiO5-10C6H5N3 coated.
The micrograph of the heat-treated mild steel shown in Fig. 5a appears rougher than that of the mild steel in Fig. 4a. Little cracks were also noticed on the micrograph. This crack formation could result from the iron oxide (Fe₂O₃) growth, when it was treat-heated to 400 oC, for 1 h 35. Although, due to the oxide formation, a change in color was observed in the micrograph of Figs. 5b-e, compared to those of the unheated samples in Figs. 4b-e coatings, with a continuous and crack-free morphology. This achievement could be ascribed to the particles surface refinement behavior, and to the coated steel oxidation kinetics 36. In Figs. 5c and 5e, the coating matrix modification, as a result of the C6H5N3 addition, might have delayed the oxidation process, and, consequently, reduced the stress in the coating matrix. More so, the oxide films could have been responsible for the enhanced substrate oxidation resistance 37.
Conclusions
The electrodeposition of Ni-30SiO2, Ni-30SiO2-10C6H5N3, Ni-30Al2SiO5 and Ni-30Al2SiO5-10C6H5N3 coatings on mild steel was achieved. The modified mild steel exhibited better strengthening characteristics than those of the uncoated steel, due to the coatings adhesion onto the substrate. Improved corrosion and wear resistance were also observed for all the coated samples. The Ni-30Al2SiO5-10C6H5N3 coated steel exhibited the lowest wear loss, and also offered the highest resistance to the attack by the corrosive agents. The coated mild steel good surface morphology indicated that the particles were well dispersed during the electrodeposition process, which impacted on its electrochemical behavior, micro-hardness characteristics and wear resisting capacity. Comparatively, Ni-30Al2SiO5-10C6H5N3 coated mild steel exhibited the overall best performance characteristics.