Fatal and non-fatal construction accidents continue to lead the occupational safety statistics for the worst reasons (Kim et al., 2019; Man et al., 2019). The construction activity’s complex nature (Winge et al., 2019), with temporary and non-routine tasks (Mohammadi et al., 2018), technology heterogeneous (Kang et al., 2020) and its exposure to macroeconomic fluctuations undermines the management of their occupational safety (Liang & Fung, 2019), which enhance accidents and injuries that cause relevant cost at different levels, personal, social and financial (Guo et al., 2016).
Siggelkow (2007) and Flyvbjerg (2006) postulated that case-based research is well suited to study organizational-related phenomena and that social sciences may be strengthened from a greater number of case studies. Encouraged by these ideas, we studied the occupational safety in one of the largest Portuguese construction companies. We carry out a preliminary study considering data from its occupational accidents (data distinct from the ones reported in the present manuscript). The results showed that the company’s safety culture did not positively influences the workers’ safety behaviors as they increased their seniority in the firm. As would be expected the contrary, we concluded that there could be problems with the company’s safety culture transmission to the operational base workforce, conveyed by the safety leadership. Working conditions may also have influenced workers’ safety performance. These results were presented to the 13th National Congress of Health Psychology - Covilhã, Portugal (Corte-Real et al., 2021). Previous results led us to the present study, which based on the company front-line workers’ perceptions and used a structural equation modeling analysis to develop and test two independent mediation models to verify if the working conditions and the safety leadership mediates the relationship between safety culture and safety performance. The knowledge obtained may help company’s managers to gain some insights into the role of perceived safety culture, working conditions and safety leadership in predicting its workers’ safety performance. Considering the relevance of the company in the Portuguese construction sector, our conclusions may also help to understand what is going on in similar firms, in this sector in Portugal, and to identify problematic areas that need to be addressed.
According to Silva (2021), we approach the phenomenon of occupational safety based on the safety culture model (Cooper, 2000; Geller, 1989) and the triadic model of reciprocal determinism proposed by Bandura within the Social Learning Theory (Bandura, 1977) and the Social Cognitive Theory (Bandura, 1986). That is, we assumed that workers ‘internal psychological factors (personal factors), his behavior (behavioral factors) and the work situation / environment they find themselves in (situational/environmental factors) influence each other to determine the occurrence of occupational incidents or accidents. Furthermore, based on Skinner’s operant conditioning theory (Skinner, 1974) and in line with DeJoy and colleagues (2004), we assumed that when managers and supervisors demonstrate their commitment to workers’ safety and their concern for workers’ well-being, the latter tend to be willing to reward the organization by complying and participating with the occupational safety.
Thus, considering that construction occupational safety is influenced by organizational, managerial, environmental and individual’s factors (Khalid et al., 2021), for instance, by the safety culture (Feng, 2013; Feng et al., 2014), the working conditions (Fernández-Muñiz et al., 2017; Peng & Chan, 2020) and the safety leadership (Fernández-Muñiz et al., 2014; Skeepers & Mbohwa, 2015), we tested two different models. One exploring how the relationship between safety culture and safety performance can be influenced by working conditions on the company’s construction sites and from their workers’ point of view. Other exploring how the safety leadership can influence that relationship.
Indeed, safety performance (SP) is an important driving force to improve industry’s occupational safety and has been defined as an aspect of the global performance at work that refers to workers’ behaviors that promote the organization’s overall safety (Cornelissen et al., 2017; Griffin & Neal, 2000). It is a two-dimensional construct composed of safety compliance and safety participation (Neal et al., 2000; Neal & Griffin, 2002). Safety compliance refers to workers’ core safety activities and procedures considered part of their tasks that improve their own safety. Safety participation refers to workers’ discretionary behaviors that indirectly improve workplace safety, like voluntary participation in safety activities (Neal et al., 2000). Barling and colleagues (2002), Clarke (2006) and Nahrgang and colleagues (2011) adopted the workers’ safety behaviors (participation and compliance) to measure workers’ safety performance and showed that they are influenced by safety culture (Fernández-Muñiz et al., 2007; Silla et al., 2017), by working conditions (Bronkhorst, 2015) and by safety leadership (Grill & Nielsen, 2019).
In turn, safety culture (SC) is defined as a set of attitudes, beliefs, perceptions and meanings shared by most of the organization’s workers, establishing the norms and values that guide their occupational safety behaviors (Guldenmund, 2000; Hale, 2000; Richter & Koch, 2004). The workers’ involvement (Fernández-Muñiz et al., 2007; Liu et al., 2020; Singh & Misra, 2020), the managers’ commitment (Fang et al., 2020; Fruhen et al., 2019; Michael et al., 2005) and the organizations’ safety management system (Job et al., 2020; Vinodkumar & Bhasi, 2010; Yiu et al., 2018) embody the organizational safety culture, and this latter influences working conditions, safety leadership, and safety performance. For instance, Feng et al. (2014) showed the interactive effects of safety culture on safety performance in hazard projects, and Duryan and colleagues (2020) emphasized the importance of cultivating a safety learning in construction companies to improve their occupational safety performance. Thus, we propose Hypothesis 1: Safety culture has a direct and positive effect on safety performance. Other contributions suggested that a constructive culture in which cooperation, supportive relationship, individual growth and high performance are encouraged, improves the safe work environment (Silla at al., 2017). On the other hand, Oswald and colleagues (2020) suggested that the safety culture often loses the battle when a trade-off is required with construction costs, originating high safety risks (e.g., through cheaper and poor-quality equipment, machinery and temporary structures) and poor working conditions. Thus, we propose Hypothesis 2: Safety culture has a direct and positive effect on working conditions. In turn, Fernández-Muñiz et al. (2007) showed the important role of managers in promoting workers’ safe behaviors, both directly through their attitudes and behaviors, and indirectly by developing a safety management system that improves the organization’s safety performance. Furthermore, Fang et al. (2020) emphasized the role of safety leadership to not only directly reduce unsafe behavior but also to fundamentally change the causes of unsafe behavior through safety culture improvement, ultimately achieving the goal of reducing unsafe behaviors sustainably and preventing accidents. Thus, we propose Hypothesis 3: Safety culture has a direct and positive effect on safety leadership.
Working conditions (WC) have been described as the set of aspects that directly and/or indirectly influence the circumstances in which workers perform their work, related either to the organizational context, to the external environment, or to the permanent dialectic between these two aspects (Aleksynska et al., 2019). According to Demerouti and Bakker (2011), work demands and work resources are initiators of inspirational processes, positive or negative. Work demands refer to physical, psychological, social or organizational aspects of the tasks that require sustained physical and/or psychological (cognitive and emotional) effort or skills, like high work pressure or unfavorable physical conditions. Work resources refer to physical, psychological, social or organizational aspects of the tasks that are functional in achieving work goals, reduce job demands and the associated physiological and psychological costs, and stimulate individual growth, learning and development (e.g., salary, career opportunities, occupational safety, supervisor and coworker support, performance feedback). Nahrgang et al. (2011) showed that, across industries, risks and hazards are the most consistent job demand and a supportive environment is the most consistent job resource in terms of explaining variance in safety outcomes. Furthermore, Fernández-Muñiz et al. (2017) concluded that in process industries, work pressure, occupational hazards and coworker support influence safety compliance, and occupational hazards, incentives and coworker support influence safety participation. In turn, Forteza and colleagues (2017) considered work demands (e.g., organizational complexity) and work resources (e.g., job coordination, job planning, or preventive planning) as construction risk predictors affecting safety performance. Moreover, Mohammadi and Tavakolan (2019) evidenced that production pressure affects safety performance and safety management interventions in construction projects, showing the relationship between the incident rate and shift hours, and Chen and colleagues (2017) emphasized that the working demands can originate workers from creating shortcuts in their tasks and taking risks. Lastly, Sousa and Ramos (2018) confirmed that there is a chain of effects between working conditions (high demands and a limited social support from coworkers and supervisors, or the perception of high levels of exposure to psychosocial risks) and physical and psychological ill-being symptoms, among truck drivers, a large professional category in the construction industry. Thus, based on the previous researches, we propose that Hypothesis 4: Working conditions have a direct and positive effect on safety performance.
Moreover, Cornelissen et al. (2017) suggested that the safety performance depends on organizational safety culture and workplace conditions at high-risk industries (construction included) and Duryan et al. (2020) emphasized the importance of a positive safety culture to encourage transfer of lessons learnt from good practices, incidents, near misses and failures between different construction projects/sites and their specific working conditions. Thus, we propose Hypothesis 5: safety culture affects safety performance through working conditions.
Lastly, safety leadership (SL) can be defined as the process of interactions between leaders and followers through which the first can exert their influence on the latter to achieve organizational safety goals, under the circumstances of organizational and individual factors (Zhu et al., 2005). According to Grill and Nielsen (2019), the construction managers influence worker’s’ safety performance in a positive way when their leadership practices correspond to continuous planning and coordination and/or monitoring work and proactively correcting deviations, or influence in a negative way when managers focus themselves just on meet deadlines and minimize costs. Furthermore, Schwatka et al. (2019) suggested that safety leadership training can improve construction supervisors’ leadership skills and improve safety performance, and Kessler et al. (2020) suggested that supervisors might encourage subordinates to behave more safely, directly modelling their safety behaviors by the immediate social environment’s influence. According to Burns (1978), leaders can influence their followers’ behaviors through the transactional leadership style and/or the transformational leadership. Indeed, Inness Michelle and colleagues (2010) suggested that safety transactional leadership improves subordinates’ safety behaviors, showing that this contingent reward leadership practice enhances workers’ behavior towards the achievement of the organizational safety goals, through rewards, punishments or corrective feedback to the workers. In turn, Mullen and colleagues (2017) suggested that perceived safety transformational leadership is positively associated with workers’ safety performance (compliance and participation). They showed that relationships between perceived workers safety obligations and their safety performance are stronger when safety leadership perception is high, opposing to when it is low. Based on the previous studies, we consider that Hypothesis 6: Safety leadership has a direct and positive effect on safety performance.
Oswald and Lingard (2019) and Wu and colleagues (2016) suggested that the safety leadership interaction between different construction stakeholders (project owners, main contractor and subcontractors) influence the occupational safety performance, showing how supervisors can implement effective safety measures and publicize safety policies and values through the construction sites, that is, conveying the organization’s safety culture. In turn, Skeepers and Mbohwa (2015) suggested that, in the construction industry, the contingency leadership visibility is influenced by a positive safety culture and influences safety performance. Furthermore, Stiles and colleagues (2018) concluded that, in the rail construction sector, the safety leadership depends on safety culture’s dimensions, such as increasing safety visibility, the workers’ involvement, the safety good practices’ recognition, and an effective communication. Moreover, Martínez-Córcoles and colleagues (2011) showed that, in a complex and risky industrial environment, when safety culture is strong, leaders safety behaviors generate a higher safety environment among the workers, improving their safety performance. As the previous researches showed that safety culture influences safety leadership and the latter influences safety performance, we propose the Hypothesis 7: safety culture affects safety performance through safety leadership. Thus, we propose the two models presented in Figure 1, to explore the relationships between observed variables and to test whether the working conditions and the safety leadership (separately considered) exert mediator effects on the relationship between safety culture and safety performance, in the perspective of the company’s workers.
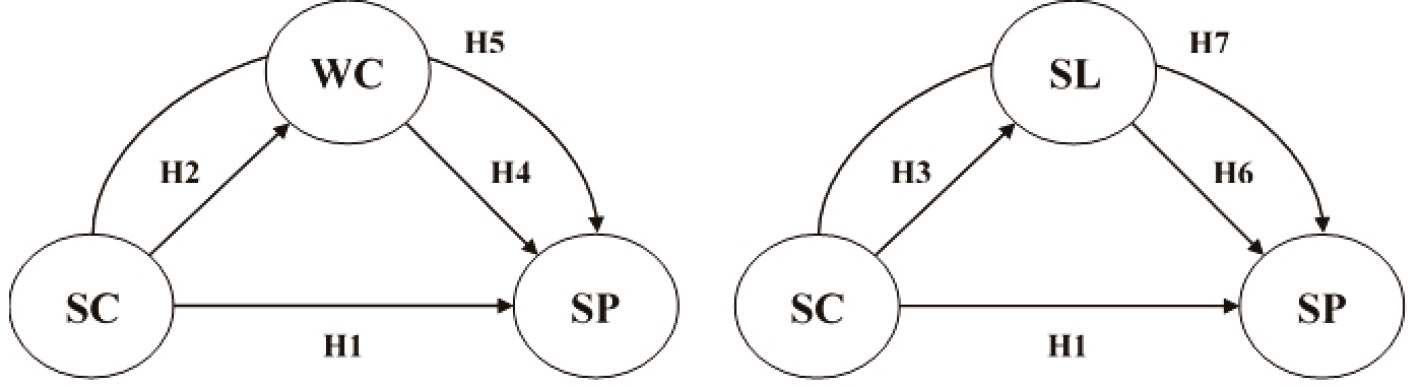
Note. SC=safety culture, WC=working conditions, SL=safety leadership, SP=safety performance, H5=mediation hypothesis of WC on SC-SP relationship, H7=mediation hypothesis of SL on SC-SP relationship.
Figure 1 Proposed conceptual models
Method
Participants
The study used a convenience sample of N=320 workers from a Portuguese construction company’s sites, with the following sociodemographic characteristics: Of the total sample, 92% were male. In relation to participants’ age, 13% were <30 years, 16% were between 31 to 40 years, 30% were between 41 to 50 years, 31% were between 51 to 60 years, and 9% were >60 years. In relation to participants’ occupational category, 3% were site managers, 6% were mid-level supervisors, 6% were front-line supervisors, 47% were front-line workers, 27% were topography, quality and safety technicians, and 4% were front-line administrative workers. In relation to participants’ level of education, 24% had primary school [≤6th grade], 23% had elementary school [7th to 9th grade], 29% had secondary school [10th to 12th grade], and 29% had bachelor or equivalent. In relation to participants’ seniority in the firm, 11% had <1 year, 20% had between 1 to 5 years, and 68% had >5 years. Furthermore, 33% of the participants were involved in occupational accidents, at least once. To confirm the sample proportion representativeness with respect to the company employees’ population, we carried out one sample z-test. The result showed that the workers ‘operational category (p=.078) and the workers’ sex (p=.39) were representative.
Study measures
We used a questionnaire for the data collection composed of two parts. The first, consisting of the sociodemographic data, aims to characterize the sample (e.g., gender, age, occupational category, education level, seniority in the firm, occupational accidents). The second part consists of four scales selected to evaluate the variable under analysis. We adapted the Safety Performance Scale, the Working Conditions Scale (Fernández-Muñiz et al., 2017) and the Safety Leadership Scale (Fernández-Muñiz et al., 2014) of to the specific contex of our study. To measure safety culture, we used the Portuguese version of the Safety Culture Scale (Fernández-Muñiz et al., 2007) validated for the Portuguese context by Job et al. (2020). The previous four original scales were already administered in the Spanish construction sector, culturally similar to Portuguese ones. After back translating the scales of Fernández-Muñiz et al., 2007 into Portuguese, we submitted a preliminary list of 99 potential items to a panel of occupational safety experts (professional and academics) to confirm the items’ appropriateness to our study sample. Furthermore, the questionnaire was submitted to a pre-test with two groups of 20 workers from other Portuguese construction firms, to confirm if they would correctly understand the items. We confirmed the adequacy of 91 items. Eight items on the safety culture scale were excluded for being inappropriate to the specific context of our study sample. As in the original scales, the items were presented in a Likert-type format and we asked participants to rank their responses on a 5-level scale, depending on their perceptions (1=strongly disagree; 5=strongly agree).
Procedure
We obtained previous approval for the study from the University’s ethics committee and the company’s board. Between November 25 and 28, 2019, at each construction site where the data were collected, we briefly explained the study’s objectives and requested voluntary, individual and anonymous participation from the participants. We used the construction site canteens to hand out 1000 questionnaires, jointly with the participants’ written consent, and we established one week for the response period. We collected 320 completed questionnaires in closed envelopes introduced inside mailboxes located in the canteens, which correspond to 32% response rate.
Data analysis
To assess the significance and strength of the relationships between the variables and determine the extent to which each hypothesized model was consistent with the data, we adopt a structural equation modeling analysis and carry out two structural equation models. A structural equation modeling analysis allows the models to consider latent variables, which are always richer and more accurate in terms of information and likely enhances explained variance and R 2 values. The global quality of the adjustment of the models were tested with the maximum likelihood method. The models were considered to have acceptable or good fit, respectively, if chi-square test and chi-square/degrees of freedom were between 5 to 2 (Wheaton, 1987); the CFI was higher than .8 and .9 (Bentler, 1990); the GFI was higher than .9 or .95, and the RMSEA, p[RMSEA≤.05] was lower than .08 or .05 (Schermelleh-Engel et al., 2003). However, we used different values in specific identified situations, so as not to lose relevant dimensions in the occupational safety phenomenon. Given the number of items in each psychological measures and the number of participants (320), and given that structural equation modeling analysis considered latent variables with multiple indicators, we respected Bentler and Chou (1987) criterion according to which a ratio of 5 cases per variable can be reasonable for normally distributed data. The constructs’ convergent validity was evaluated through composite reliability and average variance explained (Hamid et al., 2017), by confirming the Cronbach’s alpha ≥.7 (De Vellis, 2017), the average variance explained ≥.5 (Hair et al., 2010), the standardized confirmatory factor analysis loadings for all item scales ≥.5 (Anderson & Gerbing, 1988) and the construct reliability ≥.7 (Hair et al., 2010). The correlations between the factors were smaller than the square root of the average variance extracted between those factors (Hamid et al., 2017). The subscales’ discriminant validity was tested by confirming that the confidence interval (two standard errors) around the correlation estimation of each pair of factors did not contain 1 (Anderson & Gerbing, 1988). All the statistical analysis were performed using IBM SPSS Statistics (v. 26) and IBM SPSS AMOS (v. 26) and results were considered significant for p<.05.
Results
Scales’ psychometric properties
Safety performance measure validation (SP). Workers’ safety performance perception was assessed based on the two-dimensional scale of Fernández-Muñiz et al. (2017): the safety compliance dimension (4 items), referring to workers’ behavior that improves their own safety and could be considered part of their work role; the safety participation dimension (9 items), referring to voluntary participation in safety activities. Both dimensions presented Cronbach’s alpha values of .89, in the original study.
In the current study, safety performance also consists of two dimensions that have the same meaning as in the original study: the safety compliance, which uses four items (e.g., “employees use safety equipment properly”, and the safety participation, which uses six items (e.g., “employees participate in carrying out risk evaluations and safety audits”. The two dimensions presented Cronbach’s alpha of .85 and .89 respectively, average variance explained both of .56, standardized lambda parameters of .99 and .75 respectively, and construct reliability of .84 and .88 respectively, confirming the convergent validity and the reliability of the scale.
We conducted a second-order confirmatory factor analysis. The results showed that the second-order model fit the data acceptably: χ 2 (29)=70; p<.001; Rχ 2 /df=2.41; CFI=.98; GFI=.96; RMSEA=.07; p(RMSEA≤.05)=.083, suggesting that it should be appropriate to combine the scores of the two dimensions into an overall score for safety performance. The second-order latent variable, safety performance, was computed M=3.39 (SD=0.67) and the correlation between the two dimensions was r(320)=.60, p<.001. Discriminant validity was approved since there were no disputes between the two dimensions.
Safety culture measure validation (SC). Workers’ safety culture perception was assessed based on the three-dimensional scale used by Job et al. (2020): workers’ involvement (4 items) refers to workers’ compliance with safety procedures and their participation in improving working conditions; Managers’ commitment refers to managers’ attitudes regarding risk (4 items) and managers’ behaviors regarding risk (5 items). Safety management system refers to the organization’s integrated mechanisms comprising policies, strategies, and procedures designed to control occupational risks. It contains six sub dimensions: Safety policy (4 items), consisting of capturing the existence of an integrated and written declaration reflecting the organization’s commitment to safety. Incentives (5 items), measuring how companies encourage their workers to participate in safety activities. Training (7 items) to assess training plans to develop workers’ competence and safety skills. Communication (4 items), capturing the transferring of information to workers about risks in the workplace and combat them. Preventive planning (7 items), capturing procedures to evaluate the risk and establish the safety measures for avoiding accidents. Emergency planning (4 items), capturing an organized plan in case of an emergency. Internal control (5 items) that assesses the presence of mechanisms to evaluate if safety objectives are achieved. Benchmarking (2 items) that assesses if a company compares its safety performance with other similar companies. In the original study, the dimensions’ Cronbach alpha ranged between .78 (communication) and .93 (managers’ attitudes and preventive planning, both).
In the current study, the occupational safety experts’ screening removed eight of the 51 original items of this scale. We conducted an exploratory factor analysis and excluded 12 items. The remaining 31 items were arranged in five dimensions: Worker’s involvement, with the same meaning as in the original study, which uses two items (e.g., “employees involved in creating guidelines for procedures and instruction manuals”), a dimension that we have retained due to its importance in occupational safety, despite being evaluated by only two items. Managers’ commitment, which essentially reflects the extent to which managers and supervisors are committed to their workers’ safety, manifested by their attitudes or behaviors and by written declarations concerning occupational safety, which uses 10 items (e.g., “managers consider that employees’ training is essential for achieving a safe workplace”). Safety management system (11 items), which captures the existence of training plans (4 items) to develop worker’s competencies and skills in safety; evaluates communication (3 items) referring to the transferring of information to workers about risks in the workplace; incentives (3 items) that measure the extent to which the firm motivates workers to participate in activities relating to their safety; and evaluate the existence of periodic inspection (1 item) to ensure effective functioning of the whole safety management system. One sample item of safety management system is “meetings periodically held between managers and workers to take decisions affecting the work organization”. Control (3 items), which evaluates the extent to which the firm internally complies with safety procedures (1 item) and externally compares its safety actions and performance with other firms (2 items) (e.g., “firm’s accident rates regularly compared with those of other organizations from the same sector using similar production processes”). Emergency planning (5 items), which captures the existence of an organized plan in case of emergency (4 items) and control its implementation (1 item) (e.g., “firm has implemented its emergency plan”). The Cronbach’s alpha of the five dimensions ranged between .75 (workers’ involvement), and .92 (safety management system); the average variance explained ranged between .50 and .61; the standardized lambda parameters ranged between .64 and .94; and construct reliability ranged between .75 and .92, confirming the convergent validity and the reliability of the scale.
Moreover, we conducted an exploratory factor analysis. The results showed that the second-order model fit the data below the recommended cut-off values: χ 2 (423)=1100; p<.001; Rχ 2 /df=2.6; CFI=.89; GFI=.81; RMSEA=.071; p(RMSEA≤.05)<.001. Despite the referred poor fit indices, due to the second-order model complexity, we considered that it still should be appropriate to combine the scores of the five dimensions into an overall score for safety culture, a crucial dimension in the present study. The second-order variable, safety culture, was computed M=3.61 (SD=0.56) and the correlation between the five dimensions ranged from r(320)=.295, p<.001 to r(320)=.731, p<.001. There were minor disputes for the safety management system and management commitment dimensions regarding the discriminant validity approval for safety management system and emergency planning dimensions and working conditions and safety leadership constructs. However, the differences are too small, each with .01, .01 and .03, respectively, so they can be ignored (Rahim & Magner, 1996) and discriminant validity can be accepted (see Table 1).
Table 1 Convergent validity of the dimensions (α, AVE, λ, CR) and fit indexes of the measurement models (CFI, GFI, RMSEA)
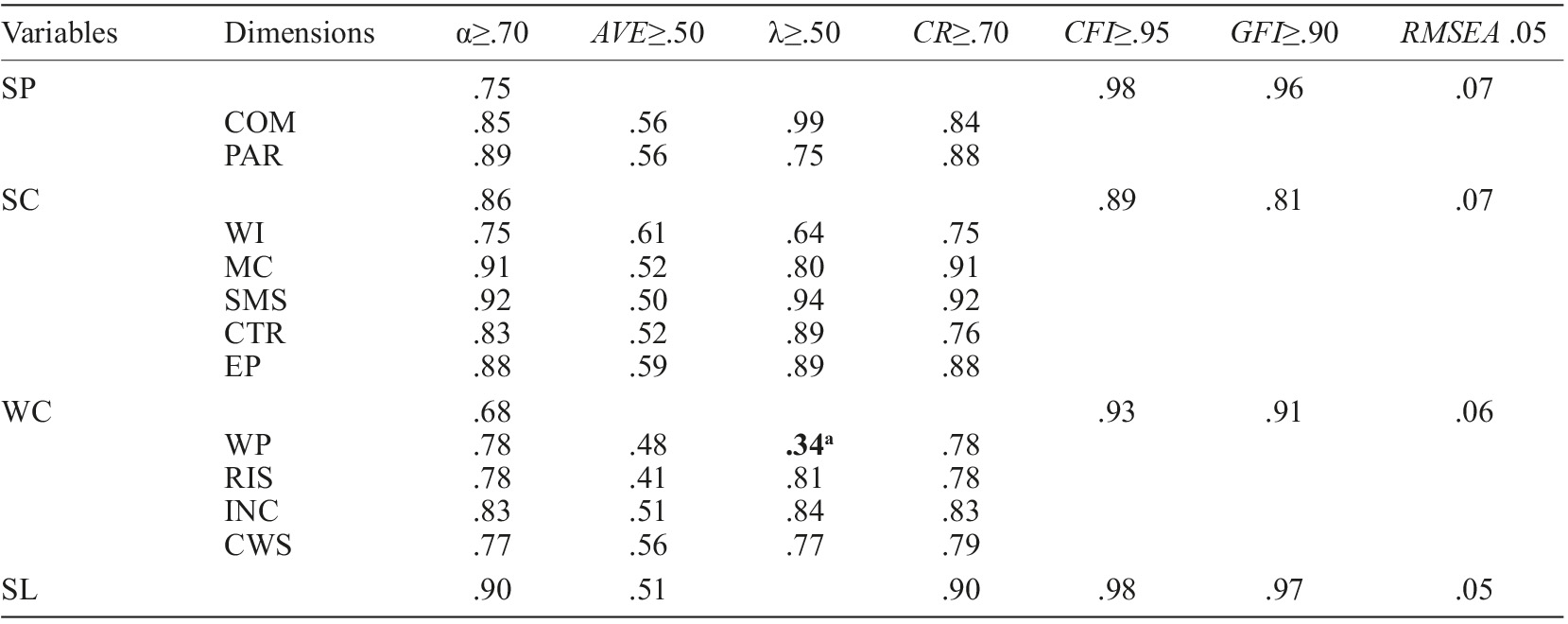
Note. SP=safety performance; COM=safety compliance; PAR=safety participation; SC=safety culture; WI=workers’ involvement; MC=managers ‘commitment; SMS=safety management systems; CTR=control; EP=emergency planning; SL=safety leadership; WC=working conditions; WP=work pressure; RIS=environmental conditions and occupational hazards; INC=safety incentives; CWS=coworker support; α=alpha Cronbach; EVA=average variance explained; λ=standardized loadings confirmatory factor analysis; CR=construct reliability; CFI=comparative fit index; GFI=goodness of fit; RMSEA=root mean square error of approximation. ain bold, coefficients that do not check the recommended limits.
Working conditions measure validation (WC). Workers’ working conditions perception was assessed based on the four-dimensional scale of Fernández-Muñiz et al. (2017). The work pressure (4 items), which refers to perceived workers’ workload and time pressure. The environmental conditions and occupational hazards (7 items), which refers to workplace’s noise, light and space conditions, risks, and hazards. The safety incentives (5 items), which refers to compensations, rewards and the firm recognitions in workers’ adequate safety behaviors. The coworker support (5 items), which refers to coworkers’ support and motivation. In the original study, the Cronbach’s alpha values ranged between .78 (work pressure) and .87 (environmental conditions and occupational hazards).
In the current study, we conducted an exploratory factor analysis and eliminated four items. The remaining 17 items were arranged in the same original dimensions, with the same meanings. Work pressure uses four items (e.g., “employees are often pressurized to finish tasks quickly”). Environmental conditions and occupational hazards use five items (e.g., “noise level is appropriate”. Safety incentives use five items (e.g., “firm rewards employees who inform about dangers in their workplace”). Coworker support uses three items (e.g., “employees try to ensure that their workmates comply with safety procedures”). The Cronbach’s alpha ranged between .77 (coworker support) and .83 (incentives); the average variance explained ranged between .41 (risks) and .56 (coworker support); the standardized lambda parameters ranged between .34 (work pressure) and .84 (incentives); and construct reliability ranged between .78 (work pressure and risks) and .83 (incentives). The work pressure’s standardized lambda presented a dispute respecting the recommended value; however, we decided to keep this crucial dimension in the occupational safety phenomenon. Thus, the scale convergent validity and reliability were confirmed.
Furthermore, we conducted a second-order confirmatory factor analysis. The results showed that the second-order model fit the data well: χ 2 (112)=263; p<.001; Rχ 2 /df=2.35; CFI=.93; GFI=.91; RMSEA=.07; p(RMSEA≤.05)=.009, suggesting that it should be appropriate to combine the scores of the four dimensions into an overall score for working conditions. The second-order variable, working conditions, was computed M=3.33 (SD=0.49) and the correlations among the four dimensions ranged from r(320)=.119, p=.033 to r(320)=.563, p<.001. Discriminant validity was accepted because there were no disputes between the four dimensions (see Table 2).
Table 2 Discriminant validity of the dimensions
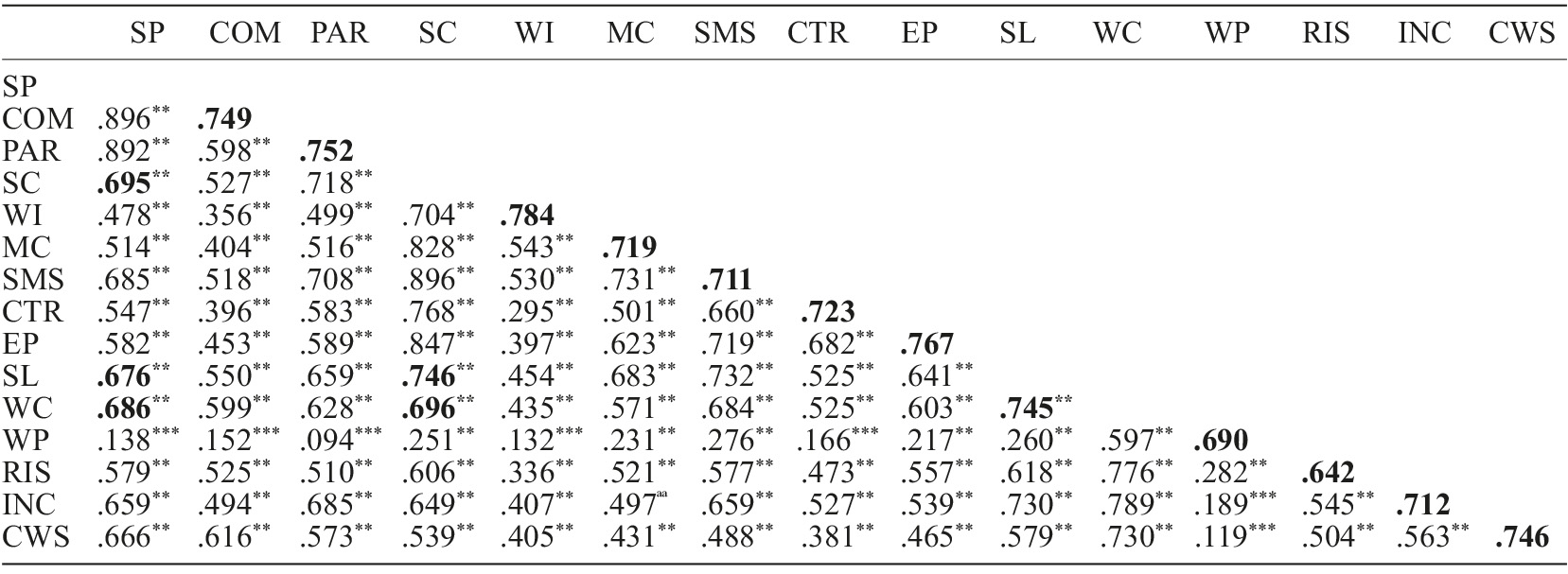
Note. The square root of the average variance extracted (AVE) in diagonal and bold, and correlations between dimensions under study, off diagonal and bold. SP=safety performance; COM=safety compliance; PAR=safety participation; SC=safety culture; WI=workers’ involvement; MC=managers ‘commitment; SMS=safety management systems; CTR=control; EP=emergency planning; SL=safety leadership; WC=working conditions; WP=work pressure; RIS=environmental conditions and occupational hazards; INC=safety incentives; CWS=coworker support. * p<.05; ** p<.01; *** p<.001; showed in diagonal and bold; factor correlation coefficients showed in the other matrix entries (off diagonal).
Safety leadership measure validation (SL). Workers’ safety leadership perception was assessed based on the two-dimensional scale of Fernández-Muñiz et al. (2014). The transactional leadership (3 items), which refers to the way managers promote safety behaviors among workers through rewards and/or punishments. The transformational leadership (7 items), which refers to managers’ supportiveness and their concern for workers’ well-being. In the original study, the dimensions presented Cronbach’s alpha .72 and .91, respectively.
In the current study, we conducted an exploratory factor analysis and eliminated one item. The remaining nine items were arranged in a single dimension, safety leadership (e.g., ‘the managers consider safety to be as important as production’). The convergent validity indexes respected the recommended values (Alpha=.90; average variance explained=.51; construct reliability=.90).
Furthermore, we conducted a second-order confirmatory factor analysis. The result showed that the second-order model fit the data satisfactorily: χ 2 (23)=45; p=.004; Rχ 2 /df=1.97; CFI=.98; GFI=.97; RMSEA=.05; p(RMSEA≤.05)=.33, suggesting that it should be appropriate to combine the scores of the single dimension into an overall score for safety leadership. The second-order variable, safety leadership, was computed M=3.57 (SD=0.68).
The safety performance prediction through safety culture, mediated by safety leadership. The three latent variables presented satisfactory reliability levels, convergent validity and discriminant validity and the proposed mediated model was satisfactory for each of its measure scales. Notwithstanding the GFI indices disrespected the recommended value, the mediation model revealed acceptable quality adjustment indexes: χ 2 (1150)=2446; p<.001; χ 2 /df=2.13; CFI=.88; GFI=.76; RMSEA=.06; p(RMSEA≤.05)≤.001. Pearson’s correlations between the principal model’s dimensions (SC, SL, and SP) were statistically significant (p<.001), ranging between .68 and .75 (see Table 2). Thus, we considered that the proposed mediation model produces consistent results for the study sample.
The results showed that SC has significant standardized direct (unmediated) and positive effects on SP (β=.69; p=.01), that is, this result supports the Hypothesis 1, which proposes the direct effect of SC on SP. The results also showed that SC has a total non-significant standardized indirect (mediated) and positive effect on SP (β=.13; p=.14), resulting from the direct, significant and positive effects from SC on SL (β=.84; p=.01) and the direct, non-significant and positive effects from SL on SP (β=.15; p=.16). Thus, these results support the Hypothesis 3, which proposes the direct effect of SC on SL, but did not support the Hypothesis 6, which proposes the direct effect of SL on SP. Furthermore, these results did not support the Hypothesis 7, which proposes the effect of SC on SP trough SL, which means that they did not confirm the proposed mediation hypothesis. The total variance of SL was explained in 71% (R 2 =.71) and the total variance of SP was explained in 69% (R 2 =.69) (see Figure 2).
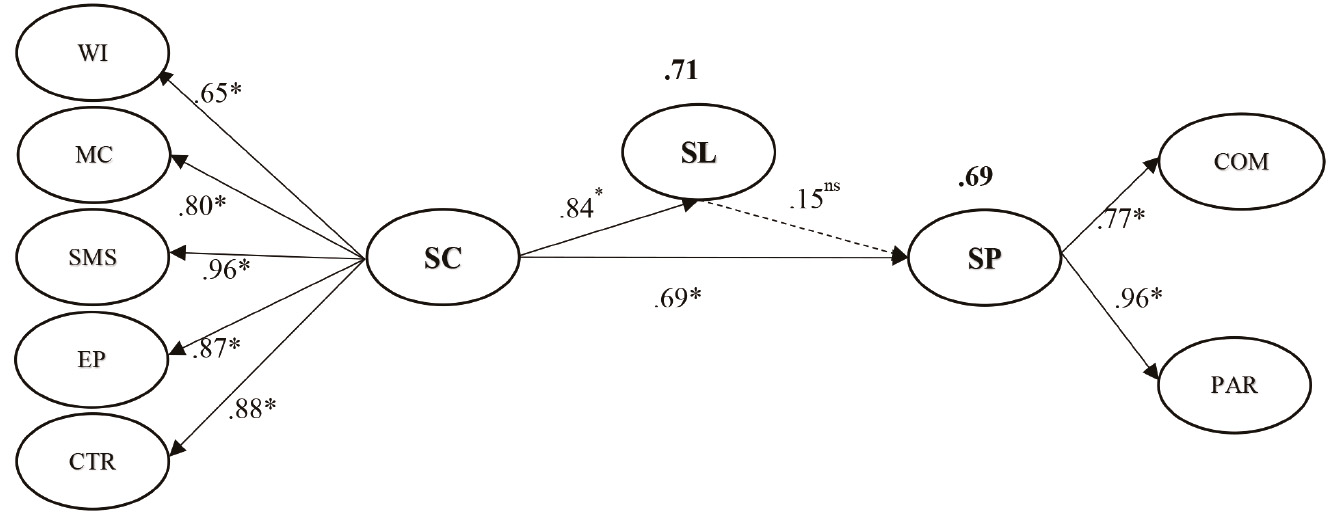
Note. With first and second order patents; square multiple correlations (in bold) and standardized regression weights. SC=safety culture; WI=workers’ involvement; MC=managers’ commitment; SMS=safety management system; EP=emergency planning; CTR=Safety control; SL=safety leadership; SP=Safety performance; COM=safety compliance; PAR=safety participation. Significant regression weight (*; p<.001); non-significant regression weight (ns; p=.14); square multiple correlation (R 2 ) in bold.
Figure 2 Proposed mediation model of the relation between safety culture and safety performance through safety leadership, re-specified for the study sample
The safety performance prediction through safety culture, mediated by working conditions. The three latent variables presented satisfactory reliability levels, convergent validity and discriminant validity and the proposed mediation model was satisfactory for each of its measure scales. Notwithstanding the GFI indices disrespected the recommended value, the mediation model revealed acceptable quality adjustment indexes: χ 2 (1567)=3189; p<.001; χ 2 /df=2.03; CFI=.86; GFI=.74; RMSEA=.06; p(RMSEA≤.05)≤.001. Pearson’s correlations between the principal model’s dimensions (SC, WC, and SP) were statistically significant (p<.001), ranging between .69 and .70 (see Table 2). Thus, we considered that the proposed mediation model produces consistent results for the study’s sample.
The results showed that SC has a non-significant standardized direct (unmediated) and positive effects on SP (β=.07; p=.78), that is, this result did not support the Hypothesis 1, which proposes the direct effect of SC on SP. The results also showed that SC has a total significant standardized indirect (mediated) and positive effect on SP (β=.77; p=.01), resulting from the direct, significant and positive effects from SC on WC (β=.87; p=.01) and from the direct, significant and positive effects from WC on SP (β=.89; p=.01). Thus, these results support the Hypothesis 2, which proposes the direct effect of SC on WC, and they support the Hypothesis 4, which proposes the direct effect of WC on SP. Furthermore, these results support the Hypothesis 5, which proposes the effect of SC on SP trough WC, which means that they support the proposed mediation hypothesis. The total variance of WC was explained in 75% (R 2 =.75) and the total variance of SP was explained in 89% (R 2 =.89) (see Figure 3).
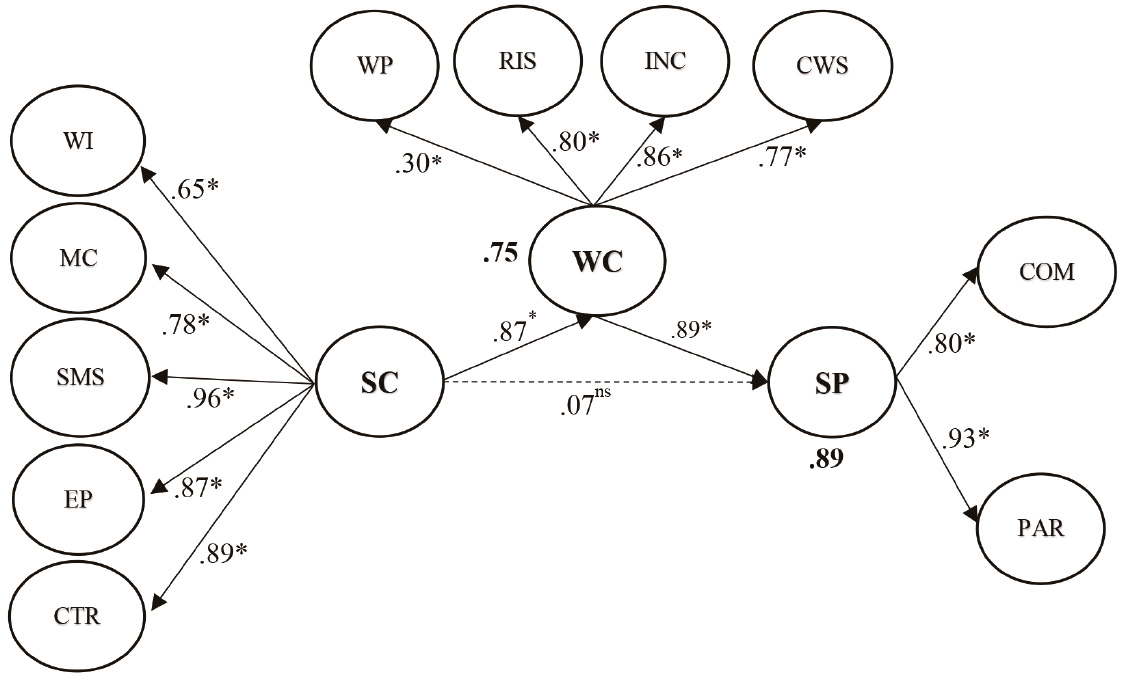
Note. With first and second order patents; square multiple correlations (in bold) and standardized regression weights. SC=safety culture; WI=workers’ involvement; MC=managers’ commitment; SMS=safety management system; EP=emergency planning; CTR=Safety control; WC=working conditions; WP=work pressure; RIS=environmental conditions and occupational hazards; INC=safety incentives; CWS=co-worker support; SP=Safety performance; COM=safety compliance; PAR=safety participation. Significant regression weight (*; p<.001); non-significant regression weight (ns; p=.78); square multiple correlation (R 2 ) in bold.
Figure 3 Proposed mediation model of the relation between safety culture and safety performance through working conditions, re-specified for the study sample
Discussion
We remember that whenever we refer to safety culture, working conditions, safety leadership, and safety performance, we want to refer to the workers’ perception-level of the respective variable.
The study main result confirmed the contextual effect of the safety culture on the safety performance prediction, directly when the safety leadership influence was not significant and indirectly through working conditions. Indeed, the safety culture influenced the safety leadership and this influenced the safety performance. Furthermore, the safety culture influenced the working conditions and this variable influenced the safety performance. In other words, the result showed that when we consider the relationship between safety culture, working conditions and safety performance, the indirect effect between safety culture and safety performance mediated by working conditions was significant and the direct effect was not. Therefore, considering the significant indirect effect between safety culture and safety performance (mediated by working conditions), we can expect that the more the workers perceive the safety culture, the better they perceive working conditions and the better they perceive safety performance (the better they commit to safety procedures and participate in occupational safety issues).
This result reinforces the role of safety culture on safety performance prediction, coherently with the study of Duryan et al. (2020), which recognized that safety performance could be improved through a positive safety culture that guaranty the transfer of knowledge between construction projects (lessons learned from good practices, incidents, near misses and failures), reducing risks on the workplace. This result is predictable since safe and pleasant working conditions assign a more influential and tangible role to the working conditions’ perception. Indeed, studies have suggested that when there is a positive work environment, resulting from social influence (support from coworkers), feedback on safety results (positive and negative ones), or praise from supervisors and small incentive awards, occupational safety workers’ compliance and participation are improved (Kessler et al., 2020; Stiles et al., 2018). Likewise, Fernández-Muñiz et al. (2017) emphasized that working conditions influence safety compliance and safety participation, and Nahrgang et al. (2011) suggested that reducing risks and hazards and creating supportive environments in industrial processes improve safety performance. According to these authors, managers’ commitment (attitudes and behaviors) can improve working conditions (e.g., by encouraging coworkers’ support, by reducing work pressure or decreasing the occupational hazards), which can avoid workers’ risky behaviors and reinforce their voluntary participation in safety activities, that is, improve safety performance.
Other result not least important showed that the safety culture influenced safety performance positively mainly by a significant and direct effect, but also by an indirect and non-significant effect through safety leadership. That is, when we consider the relationship between safety culture, safety leadership and safety performance, the direct effect from safety culture on safety performance was significant and the indirect effect was not. Therefore, considering the direct and significant relationship between safety culture and safety performance, in the presence of a non-significant influence of the safety leadership, we can expect that the more positive the workers perceive the safety culture, the more they perceive safety leadership, but the same do not occur between safety leadership and safety performance. Thus, we realized that the mediation effect of safety leadership on the relationship between safety culture and safety performance was not significant. Nevertheless, this result is coherent with authors that proposed close connotations between safety culture and safety leadership in construction projects. For instance, Wu et al. (2016) suggested that safety culture influences safety leadership relationship between the project owner, the main contractor and the construction site supervisors, inducing the latter to adopt safe behaviors as models for workers. However, this research result was poorly consistent with Martínez-Córcoles et al. (2011) study, which showed that when safety culture was strong, the safety leadership generated a higher safety involvement among the workers, predicting their perceived safety behaviors and improving their safety performance. Our result was also poorly coherent with Fang et al. (2020) study, which highlighted the role of safety leadership, not only directly by reducing unsafe behavior in the workplace, but mainly by changing the causes of these behaviors via safety culture, sustainably reducing unsafe behaviors.
Considering that both results focus on crucial occupational safety resources (expensive and scarce ones), which are organizational safety performance predictors and the way to manage it, our study suggests that to promote company safety performance, the firm should focus itself on developing its safety culture. In fact, due to the current international crisis context, numerous companies face critical compatibility concerns regarding the safety culture, due to mergers, acquisitions, and other operations aimed at reducing permanent staff and making structures more flexible. Complementary, the firm should focus itself in their safety leadership behaviors and attitudes and in their own working conditions. Indeed, according to Oswald et al. (2020), in the project construction phase, working conditions can be degraded by cheaper and lower quality equipment, machinery and temporary structures, that is, by high safety risks resulting from low bid to win bids.
Conclusions
The study main conclusion is recognizing the key role of the workers’ organizational safety culture perception on safety performance prediction, whose influence was mediated by working conditions but not by safety leadership. This conclusion contributes to optimize the allocation of resources to improve safety performance in the company, namely by the safety culture, which is especially relevant in the current context of international crisis. Therefore, top management leaders and intermediate leaders has to be more awareness about the importance of safety culture and safety leadership to ensure occupational construction-accidents reducing. The top management leadership needs to reinforce the organizational safety culture, and the intermediate leadership needs to support it and become more involved in transmitting the safety culture to workers in the company’s operating base. Another important conclusion is the recognition of the relevant role of working conditions on safety performance prediction, which shows that supervisors should be more attentive to indicators of working conditions, whether by controlling high work demands that may lead workers to by-pass safety procedures or by reinforcing work resources to motivate workers to get involved in occupational safety.
The manuscript addresses the relationships between key predictor’s variables on occupational safety and we expect that the conclusion could contribute to raise awareness and the information level of safety engineering and decision makers in the company under study. Furthermore, considering that the latter is one of the largest Portuguese construction companies, we hope the knowledge obtained may help to understand what is going on in other firms, in this sector in Portugal, and to identify problematic areas that need to be addressed.
This study has some limitations that should be considered when reading its results. The study only considered individual workers’ safety perceptions (it did not analyze working groups) and did not study subcontractor workers, nor migrant workers. The variables under study were measured through a survey and not objectively assessed, so that authors obtained individual workers’ responses (perceptions). As the questionnaires did not define a safety leadership reference-level, likely the workers’ responses tended to focus more towards leadership levels directly linked to the workplace and less on the company’s top management leadership levels. The sample’s representativeness in relation to the company’s working population was not controlled (the sample proved to be representative considering only the sex and workers’ professional category). Because this study is a cross-sectional one, the parameters estimated do not determine the direction of variables influences. Furthermore, the measurement models of the variables under study showed some collinearity, although the correlations between the dimensions were acceptable.
Some current research limitations indicate possible future study lines. For example, future researches will be enriched if consider both, the safety climate and the safety culture, and if consider collective construction working groups’ perception, allowing a broader understanding of the relationships between the variables under study. Furthermore, the methodology adopted does not allow the statistical generalization of the results obtained. It would be interesting for future studies to verify whether the proposed mediation models would get similar results to those of the present investigation in other construction companies, in Portugal and abroad, aiming at its possible generalization to the construction sector.
Practical applications
As practical applications, the study conclusion contributes to optimize the allocation of resources to improve safety performance in the company, insofar as they suggest that improving safety performance mainly depends on the attention that managers give to the company’s safety culture and their working conditions. The study also contributed to the company’s selection and adequate training programs in order to reinforce safety leadership competencies to be more sensitive to occupational working conditions and to be more effective in safety culture dissemination. In short, we hope that the study conclusions can inspire the company and its workers to be more aware of the importance of safety culture, working conditions and safety leadership when preventing occupational accidents.