Serviços Personalizados
Journal
Artigo
Indicadores
Links relacionados
Compartilhar
Corrosão e Protecção de Materiais
versão impressa ISSN 0870-1164
Corros. Prot. Mater. vol.35 no.1 Lisboa mar. 2016
https://doi.org/10.19228/j.cpm.2016.35.01
ARTIGOS
Pitting corrosion of 304 stainless steel in an activated carbon filter
Corrosão por picada de um aço inoxidável 304 num filtro de carvão activado
J.I. Martins1,2*and C.M.B. Martins1,2
1 Universidade do Porto, Faculdade de Engenharia, Departamento de Engenharia Química, Rua Roberto Frias, 4200-465 Porto, Portugal
2 Universidade do Minho, Instituto de Ciências Sociais, Lab2PT- Laboratório de Paisagens, Património e Território, Campus do Gualtar, 4710-057 Braga, Portugal. E-mail: carlamariabrazmartins@gmail.com
* A quem a correspondência deve ser dirigida. E-mail: jipm@fe.up.pt
ABSTRACT
Water leakages of an orange color were found in the cross welding zone and barrel of an activated carbon filter used in a wastewater treatment plant. The analysis of the chloride content in the plant flowsheet showed that the equipment was subjected to unsuited chloride concentration for 304 stainless steel resistance to pitting corrosion. The inside shows holes distributed randomly from about 20 cm above the welding zone to the lower outlet port of the equipment. The rehabilitation of the equipment was made by replacing the damaged cylindrical part and performing an inner liner of polymer matrix composite. It was recommended to eliminate the entry of oxidants in the filter, and a better control of coal saturation.
Keywords: Stainless Steel 304, Ping Corrosion, Activated Carbon Filter, Hypochlorite, Welding, Composites
RESUMO
Fugas de água de uma cor laranja foram encontradas na zona de soldadura transversal e corpo de um filtro de carvão activado usado numa estação de tratamento de águas residuais. A análise do teor de cloreto no fluxograma da planta mostrou que o equipamento foi submetido a uma concentração de cloreto inadequada para a resistência do aço inoxidável 304 à corrosão por picada. O interior mostra perfurações distribuídas aleatoriamente a partir de cerca de 20 cm acima da zona de soldadura da saída inferior do equipamento. A reabilitação do equipamento foi feita através da substituição da parte cilíndrica danificada e aplicando um revestimento interior de um compósito com matriz polimérica. Foi sugerido a eliminação da entrada de oxidantes no filtro e um melhor controlo da saturação do carvão.
Palavras-chave: Aço Inoxidável 304, Corrosão por Picada, Filtro de Carvão activado, Hipoclorito, Soldadura, Compósitos
1. INTRODUCTION
Activated carbon is a material obtained from natural products subjected to a pyrolysis (400-600°C) in the absence of oxygen followed by a physical or chemical treatment. The first stage is aimed to convert the raw-material in elemental carbon, and the second to open and multiply the pores. This last phase confers a large specific surface area, in addition to forming functional groups responsible for the charcoal active sites [1, 2], which makes it suitable in wastewater treatment for removing organic substances [3, 4], metal cations and residual chlorine [5].
The manufacture of active carbon filters equipment is usually performed with special-mixed fiberglass, AISI 304 or 316 SS or carbon steel with rubber lining or epoxy resin against corrosion.
Austenitic stainless steels have high corrosion resistance in several aqueous medium, attributed to the presence of a thin invisible film and passive characterized by stability, durability, adhesion and self-repairs [6]. However, in chloride environments [7-10] these stainless steels may undergo pitting corrosion, according to concentration level of chloride. Once initiated, the rate of pitting corrosion is quite serious, since it continues to grow even when the adjacent area remains intact. The hypochlorite ion (ClO-) is also a key factor in pitting, particularly in dry-wet situation as has been showed by Martins et al. [11]. In this case, the residual chlorine content must not exceed 2 ppm or 5 ppm, respectively, for 304L and 316L stainless steels (AWWA Standards C651 / 65).
The crack or crevice corrosion in water is rare in stainless steels at a pH above 6 and ambient temperature, which is mostly the typical situation of industrial waste effluents. Under severe conditions, for example, narrow slits, low pH, high temperature, low flow rates, and other situations where there is a risk of a localized concentration of chloride, stainless steel 304L and 316L should be used for chloride content up to 50 ppm and 250 ppm, respectively.
Weld decay is a corrosion process that may occur in austenitic stainless steels as a result of sensitization in the heat affected zones (HAZ) of metal during welding operations [12]. At temperature range of 425-815 ºC the stainless steels may have a depletion in chromium, as the result of chromium carbide formation along the grain boundaries of the austenitic structure. Thus, the region adjacent to the grain boundary [13] becomes sensitive to intergranular corrosion attack, particularly in the presence of chlorides. Usually, the stainless steels of low carbon content are immune to sensitization.
This article analyzes the causes responsible for stainless steel 304 failure in an activated carbon filter equipment used in a wastewater treatment plant.
2. EXPERIMENTAL DETAILS
The steel was analyzed by emission spectrometry using a Spectrolab equipment, Table 1, and the composition shows a stainless steel 304.

The scanning electron microscopy (SEM) images and the analysis by energy dispersive spectroscopy X-ray (EDS) were made with a FEI Quanta 400FEG equipment, fitted with a probe for micro analysis EDAX Genesis X4M. The pressure inside the chamber was about 6x10-2 Pa. The distance between the objective lens and the sample, ranged between 6 mm and 15 mm. The SEM filament was operated at variable current and at 15 kV voltage. The SEM/EDS analysis has been performed in CEMUP (Materials Centre of the Oporto University).
Radiographs were performed using the equipment XRS-3 with a pulsed X-ray source and the Vidisco imaging system. The analysis of chloride in the effluent was performed by volumetric and potentiometric titration.
3. ASSESSMENT OF THE SITUATION
It is an activated carbon filter used in the installation of wastewater treatment of a cosmetic industry, Fig. 1a), showing leakages in the region of circumferential weld seam, Fig. 1b), and under the plastic coating to protect the equipment against scratches on shipping, Fig. 1c).
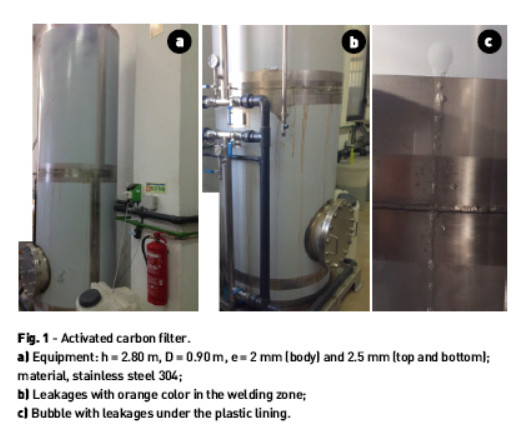
After removing the activated carbon, plastic lining and cleaning the inside of the equipment, it was possible to gather more information inserted in Fig. 2. With all this information, we can reach the following conclusions:
• The device is coated with plastic on the cylindrical portion except the area adjacent to the circumferential weld bead, Fig. 1a).
• The water leakages of orange color on the cylindrical body emanate from the welding bead, Fig. 1b and Fig. 2a), and from non-visible holes under the plastic, Fig. 1c) and Fig. 2b).
• The plastic removal in zone 30 cm from the bottom outlet of the equipment showed several perforations originating from the inside to the outside.
• Pits have a variable size from 0.7 to 2.5 mm, and tend to aggregation.
• Control valves do not show the presence of pits.
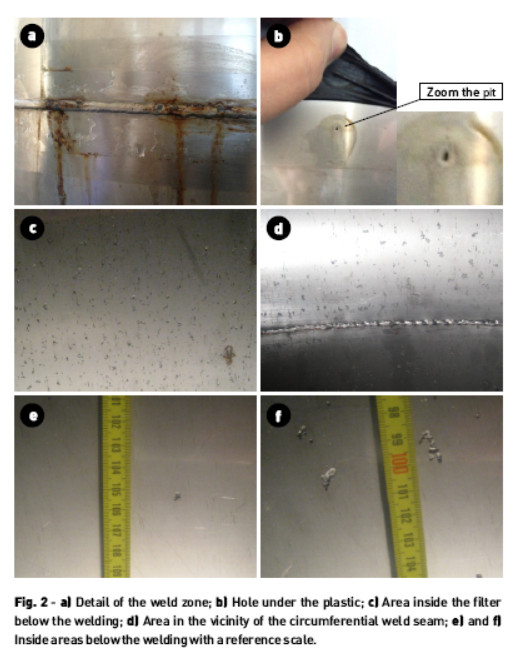
4. FLOWSHEET OF WASTEWATER TREATMENT
Fig. 3 shows the processing wastewater plant diagram with the flow rates and the respective composition of chlorides. The information set on flowsheet show the following:
• The chlorides are present in the raw wastewater and consequently their concentration is not increased significantly from the primary antifoam coagulant used in the physicochemical unit to promote flocculation.
• It is added to the effluent treatment plant, before adsorption unit, a flow of 10,000 L d-1 with a chloride concentration of 36 mg L-1 from a factory osmosis unit that uses the public water previously dechlorinated and decalcified for protecting the osmosis polymeric membrane.
• The incoming flow in the adsorption unit is 11,000 L d -1 with 177.1 mg L-1 chloride content.
• Microfiltration unit periodically needs to promote the cleansing of the ceramic membrane with a closed loop system using the following operative sequence: 1) washing with water; 2) cleaning with an alkaline solution of sodium hydroxide (0.5 %) and sodium hypochlorite (2,000 ppm); 3) washing with water; 4) washing with citric acid solution; 5) washing with water. Thus, from time to time it is introduced into the treated water storage tank, an effluent with residual chlorine (not determined) from the remaining hypochlorite.
• The hypochlorite handling for the recovery of ceramic membrane is in the vicinity of the activated carbon adsorption unit, wherein the storage tank sewage drains by gravity to the hand-tight tank feeding the adsorption unit.
Taking into account the composition of the input and output streams, a material balance of chlorides in the adsorption unit gives:

V = volume of solution within the adsorption unit, assumed as 40% of equipment capacity, V = 712 L.
[Cl-]s = chloride concentration in the solution inside the equipment.
The equation (1) shows that [Cl-]s = 4,028 ppm, which means a passage of chloride ions from activated carbon to the effluent. Thus, the interior of the equipment has been subjected to a high chloride concentration at neutral pH and room temperature.
5. TREATMENT OF WASTEWATER WITH ACTIVATED CHARCOAL
Activated carbon is commonly used in drinking water treatment or wastewater, for color removal, odor, and bad taste, through an adsorption mechanism.
Chemicals such as chlorine and hypochlorite employed in disinfection or organic material oxidation in the water are removed by a process somewhat different from the simple adsorption. In this case there is a catalytic decomposition of the oxidizing agent on the surface of the activated carbon according to the following reactions:



According to reactions (2) and (3), the cleaning of the ceramic membrane of the microfiltration unit will be an operation responsible for the chloride concentration increasing in the tank inside the adsorption unit.
The adsorption isotherms establish the relationship between the amount or concentration of adsorbed on the adsorbent (qe), and the equilibrium concentration of the adsorbate in the solution (Ce).
The equilibrium data for plotting this relationship, Fig. 4a, are obtained from "batch" experiments using the following expression:

V = volume of the solution used in the test (L).
Co = initial concentration of adsorbate in the solution (mg L-1 ).
Ce = concentration of adsorbate in equilibrium in the solution (mg L-1 ).
qe = concentration of the adsorbate in the adsorbent in equilibrium with the solution (mg g-1 of adsorbent).
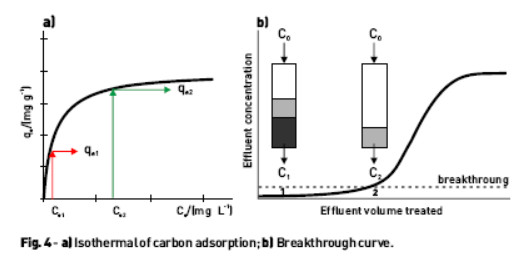
After some time, the loading of the carbon increases, the available adsorption places are filled, and breakthrough of the chloride in the effluent occurs, Fig. 4b). However, there may be chloride transfer from the solid phase to the effluent even when the adsorbent is not saturated. The inverse behavior of the activated carbon is explained by analyzing the equilibrium adsorption isotherm data, Fig. 4a). Indeed, it is only necessary that the input effluent to the adsorption unit has a chloride concentration (Ce1) smaller than the equilibrium concentration (Ce2) related with the content accumulated in the adsorbent (qe2). In this case it is established a concentration gradient of chloride ion that will impose on the system an evolution for a pseudo equilibrium position with chloride concentrations qes and Ces , respectively, to the adsorbent and solution, so that it satisfies the following material balance:

V= volume of solution within the adsorption unit (L).
Ces = [Cl-]s = chloride concentration in the solution (mg L-1 ].
Mc= total mass of activated carbon inside de filter (g).
qes = concentration of the adsorbate in the adsorbent at pseudo equilibrium (mg g-1 of carbon).
qe2 = concentration of the adsorbate in the adsorbent at point 2 in equilibrium isotherm (mg g-1 of carbon).
According to the transcript about the flowsheet of the wastewater plant this situation can occur several times.
6. RESULTS
6.1 Radiographs of weld
The radiographs in the welding zone of the equipment, Fig. 5a, show a good penetration and uniform bead, even in the place where holes have been observed. As holes were found in areas outside the welding zone we must conclude that the material failure is not due to welding, but instead to the high aggressiveness of the environment for the steel alloy in question.
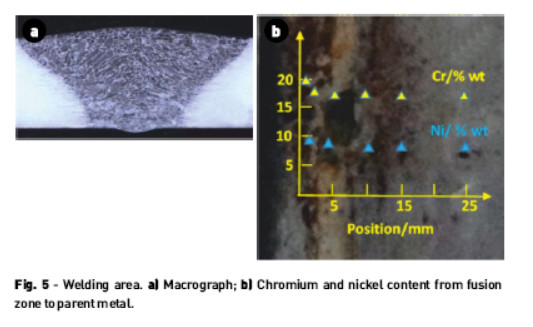
6.2 Chemical analysis by SEM/EDS
The chemical analysis performed from the fusion zone until the parent metal, Fig. 5, shows a chromium content according to passivation.
The chromium content ranges from about 19.0 % in the fusion zone to 18.3 %, and nickel from 8.7 % to 8.0 %.
7. DISCUSSION
The interior of the filtration unit is constituted by a diffuser plate positioned slightly above the bottom outlet, on which 25 cm of sand and an activated carbon bed with about 1.8 - 2.0 m thick are placed. The pressure drop in the unit is in the order of 0.8 bar. Despite the existence of an expansion chamber in the system, there will always be preferential paths in the effluent percolating through the filter bed. This occurrence originates differential cell concentration responsible for localized attack [14], which is also associated with the composition of the effluent. This parameter with regard to the chloride content is essential, in view of the adverse effect of this anion on the 304 stainless steel passivation. The concentration of sodium chloride may increase inside the filter unit when the activated carbon is close to saturation by one of the following ways: 1 -When cleaning the ceramic membrane microfiltration unit, since residual chlorine in contact with activated coal is converted into the chloride according to reaction 2) and 3); 2 -When the concentration of chlorides in the input chloride effluent has a lower value corresponding to the equilibrium saturation of carbon. In this case, it is noted that the interior material was subjected to a concentration (4,028 ppm) much greater than the value taken as acceptable. The aggressiveness of the hypochlorite ion in the stainless steel is also associated to its cathodic behavior besides the reduction reaction of oxygen [11].

In order to solve the problems in the activated carbon the following actions were taken: 1 - Eliminate chlorine in the input stream of the filter unit coming from the ceramic membrane cleaning. The discharge of the downstream effluent must be made to a tank containing a reducing agent (e.g., sodium bisulfite) for limiting the residual chlorine content to 0.01 ppm before entering the public network. 2 -Remove the plastic coating, which is only performed for protection of the equipment during road or railway transport. 3 - Control the chloride content in the input stream and output of adsorption unit to set the breakthrough of chlorides suitable to avoid the inversion of the adsorption mechanism of the activated carbon. 4 -Avoiding the stainless steel 304 contact with the effluent proceeding to its coating with a polymer (polyester) matrix composite, Fig. 6. In this mode the stainless steel only provides the mechanical properties.
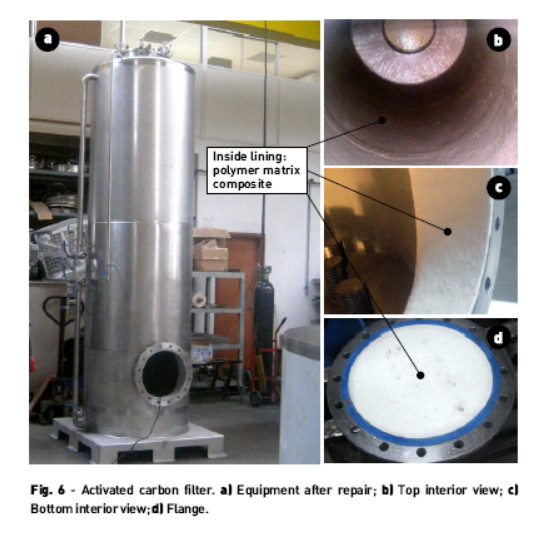
8. CONCLUSIONS
According to the observations and experimental results it is concluded the following: 1 -The perforations observed on the metal surface of the 304 stainless steel activated carbon filter develop from the inside to the outside of the equipment. 2 -The radiographs performed on the welding zone don't show technical deficiencies in its execution. 3 -The interior of the filtration unit was subjected to a chloride content which is incompatible with the pitting corrosion resistance of stainless steel 304, in the order of 4,000 ppm.
References
1 H. Teng, J. A. Ho and Y. F. Hsu, Carbon, 35, 275-283 (1997). [ Links ]
2 N. R. Khalili, M. Campbell, G. Sandi and J. Golas,Carbon, 38, 1905-1915 (2000). [ Links ]
3 C. Moreno-Caslla, Carbon, 42, 83-94 (2004). [ Links ]
4 G. M. Mwangi and G. B. Oguntimein, West Indian Journal of Engineering, 35, 65-71 (2013). [ Links ]
5 M. I. Yusufu, C. C. Ariahu, N.N. Nkpa and B. D. Igbabul,J. Chem. Eng. Mater. Sci., 3, 23-29 (2012). [ Links ]
6 J. Sedriks (Corrosion of Stainless Steels), 2nd Edition, John Wiley & Sons, New York, USA (1996).
7 A. Fossati, F. Borgioli, E. Galvanetto and T. Bacci, Corros. Sci., 48, 1513-1527 (2006). [ Links ]
8 Q. Yang and J. L. Luo, Electrochim. Acta, 46, 851-859 (2001). [ Links ]
9 E. A. Abd El Meguid, N. A. Mahmoud and S. S. Abd El Rehim, Mater. Chem. Phys., 63, 67-74(2000). [ Links ]
10 S. S. El-Egamy and W. A. Badway, J. Appl. Electrochem., 34, 1153-1158 (2004). [ Links ]
11 C. M. B. Marns, J. L. Moreira and J. I. Marns, Engineering Failure Analysis, 39, 65-71 (2014) [ Links ]
12 M. Song and K. Guan, Engineering Failure Analysis, 18, 1613-1618 (2011). [ Links ]
13 D. A. Jones (Principles and Prevenon of Corrosion), MacMillan, New York. pp. 115, 200 and 291 (1992) [ Links ]
14 J. I. Marns and M. C. Nunes, Electrochim. Acta, 52, 552-559 (2006). [ Links ]