Serviços Personalizados
Journal
Artigo
Indicadores
Links relacionados
Compartilhar
Portugaliae Electrochimica Acta
versão impressa ISSN 0872-1904
Port. Electrochim. Acta vol.32 no.2 Coimbra mar. 2014
https://doi.org/10.4152/pea.201402137
Improvement of Corrosion Resistance of Ni-P-Al2O3 Composite Coating by Optimizing Process Parameters Using Potentiodynamic Polarization Test
Prasanna Gadhari and Prasanta Sahoo*
Department of Mechanical Engineering, Jadavpur University, Kolkata 700032, India
Abstract
Electroless Ni-P based composite coatings are more popular due to their excellent hardness, yield strength, wear resistance, frictional resistance, corrosion resistance, and good lubricity. The present study deals with significance of various coating process parameters on the corrosion behavior of the Ni-P-Al2O3 composite coatings on mild steel substrate. Corrosion behavior of the composite coatings after heat treatment at various annealing temperatures (300 °C, 400 °C, and 500 °C) are investigated by potentiodynamic polarization test using 3.5% NaCl solution. For maximization of corrosion resistance, the electrochemical parameters, corrosion potential (Ecorr) and corrosion current density (Icorr), are optimized using Taguchi based grey relational analysis. For optimization four coating process parameters are considered, namely, concentration of nickel source, concentration of reducing agent, concentration of second phase particles (alumina particles), and annealing temperature, as main design factors. The optimum combinations of the said design factors are obtained from the analysis. Analysis of variance (ANOVA) reveals that the concentration of alumina particles and annealing temperature has the significant influence on the corrosion resistance of the composite coatings. The microstructure of the surface is studied by scanning electron microscopy (SEM) and chemical composition is studied by energy dispersive X-ray analysis (EDX). The X-ray diffraction analysis (XRD) is used to identify the phase transformation behavior of the composite coatings.
Keywords: Ni-P-Al2O3 composite coating, corrosion, potentiodynamic polarization, optimization.
Introduction
In industries protection of machine parts, tools, and equipment from environmental changes, corrosion, erosion, friction and wear is very essential.
For that purpose these should be made from hard, tough, wear and corrosion resistant materials, but it is not beneficial in all respect. In such cases it should be possible by applying specific layer on the base material to protect form corrosion and environmental changes and also to increase wear and friction resistance. Special coatings for surface protection are an essential part of design, development and synthesis of advance and novel materials. Recently, electroless coatings have gained wide popularity in automobile, mechanical, aerospace, chemical and in scientific domain, due to its ability to produce hard, wear resistant, friction resistant, and corrosion resistant surface [1]. Electroless plating is an autocatalytic process in which the reduction of the metallic ions and coating deposition can be carried out through the oxidation of the reducing agent. The substrate develops a potential when it is dipped in electroless bath, which contains a source of metallic ions, reducing agent, complexing agent, stabilizer, additives and wetting agents, etc. Due to the developed potential, both positive and negative ions are attracted towards the substrate surface and release their energy through charge transfer process. The non-crystalline amorphous Ni-P coatings with more than 7 wt.% phosphorus content have excellent corrosion resistance. Hence they are used in corrosive environments such as oil and gas industry, mining, chemical, and structural components. The electroless coatings can be broadly classified into four groups viz, pure nickel and black nickel coatings, alloy and poly alloy coatings, composite coatings, and electroless nano coatings [2]. The electroless coating has highly consistent thickness across all the surfaces, including edges and complex interior geometry.
Electroless nickel composite coatings are developed by co-deposition of fine inert second phase particles into a metal matrix from an electroless bath. This coating is developed by impact and deposition of second phase particles on the surface of the substrate and subsequent surrounding of these particles by Ni-P matrix as it is deposited. To improve mechanical and tribological properties along with lubricity of Ni-P coatings, second phase particles have been introduced into the Ni-P matrix. The composite coatings can be mainly categorized into two groups: (1) coatings incorporating soft particles like PTFE, MoS2, HBN, graphite to improved corrosion resistance, reduced friction coefficient, and to provide better lubricity and (2) coatings containing hard particles e.g., SiC, WC, Al2O3, Si3N4 CeO2, TiO2, ZrO2, and diamond, etc., for getting the higher hardness, wear, friction, and corrosion resistance [3]. The excellent properties of electroless nickel composite coatings depend on the stable and uniform distribution of nano or composite particles; otherwise composite coatings would have non-uniformly distributed particulates and numerous defects, owing to segregation and agglomeration of nano or composite particles with high surface energy and activity in the electroless bath [4]. An appropriate heat treatment at 400 °C for 1 hour can increase hardness and tribological properties such as frictional and wear resistance of composite coatings significantly [5]. Various hard particles explained above are commonly used as reinforcement phase. Among these hard particles, Al2O3 is the most important in engineering materials because of its high elastic modulus, strength retention at high temperature, and high wear resistance [6]. In general, the incorporation of second phase particles in electroless Ni-P composite coatings depends on particle impingement on the coating surface and holding time of the particle on the coating surface [7]. Alirezaei et al. [8] have reported that deposition rate, codeposition particle percent, roughness and hardness of Ni-P-Al2O3 coatings have been influenced by the concentration of alumina in bath, whereas average roughness and hardness increase with particle content.
Electroless Ni-P coatings are well known for their excellent corrosion resistance. In particular environment it is higher than that of pure nickel or chromium alloy due to two factors, namely, amorphous nature and passivity of the coating [9]. The corrosion resistance of the coating depends on several factors for, e. g., phosphorus content, porosity, and heat treatment of the coatings. The most important factor that affects coating porosity is the surface roughness, which is influenced by mechanical preparation of surface and deposition of composite particles on the coated sample. To avoid the porosity of the composite coating, composite particles must be uniformly distributed over the coated surface. In this regard the surfactant plays very important role. Due to the presence of surfactant in the electroless bath, the composite particles are uniformly distributed over the coated surface and it also increases the corrosion resistance of the coating. Recently, much attention is being paid towards nickel phosphorus based composite coatings because their properties are much better than the basic Ni-P and Ni-B coatings [4].
According to polarization test results, Araghi et al. [10] have found that Ni-P- B4C composite coating exhibited good corrosion resistance but not better than Ni-P coating. The reduction in corrosion resistance is due to the creation of micro cracks on the surface of the composite coating. Zarebidaki et al. [11] have confirmed that the corrosion resistance of Ni-P-SiC coatings depends on the dispersion of nano particles throughout the coatings. At higher concentration, the SiC particles are agglomerated on the coated surface, which provokes the porosity of the composite coating. On the basis of Nyquist plot they also confirmed that Ni-P coatings have better corrosion resistance as compared to Ni- P/nano-SiC composite coatings. Parveen et al. [12] have found that the addition of CNT particles in the zinc coating increases the corrosion resistance. Zarebidaki et al. [13] have observed that the proper heat treatment significantly improves the coating density and structure. Due to change in coating structure and density, the corrosion resistance of Ni-P-CNT composite coating enhanced significantly. It is also observed that the corrosion resistance of coating depends on various factors such as phosphorus content, nature of corrosion solution, and incorporation of composite particles in Ni-P coatings. The experimental results confirmed that the Ni-P-CNT composite coating has better corrosion resistance as compared to Ni-P coating. As the composite coating has less effective metallic area prone to corrosion due to presence of CNT particles. Zarebidaki et al. [11] have observed that the porosity percent of the composite coatings decreased by increasing incorporation of alumina particles in the composite coatings, which results into increase in corrosion resistance. Allahkaram et al. [14] have found that incorporation of ZnO nano particles increases the corrosion resistance of the coating due to decrease in electrochemically active area of the coating surface. Same trend is observed by M. Momenzadeh and S. Sanjabi [15] for Ni-P-TiO2 nano composite coatings in 3.5 wt.% NaCl solution.
Rabizadeh et al. [16] have found that Ni-P/nano-SiO2 composite coatings have better corrosion protection as compared to electroless Ni-P coatings because of less corrosion prone area available on the surface of composite coatings. Cheng lee [17] has found that Ni-P/nano-TiO2 composite coating with denser structure and higher phosphorus content improved the electrochemical properties of the composite coating and also found that above 15 g/L TiO2 concentration the corrosion resistance decreased. Cheng Lee [18] has performed immersion test in 3.5 wt.% NaCl solution for different duration from one hour to 720 hours and found that Ni-P-CNT composite coating has higher corrosion protection compared to Ni-P/nano composite coating due to denser and uniform distribution of composite particles with higher phosphorus content. J. Novakovic and P. Vassiliou [19] have found that after vacuum heat treatment composite coating has less corrosion resistance as compared to electroless Ni-P coating and similar trend is seen in as deposited coating with higher corrosion resistance as compared to annealed samples.
Electrochemical corrosion measurements give a basic picture of corrosion behavior of material in a particular corrosion medium. It is clear from literature review on Ni-P coatings that the preferential dissolution of nickel occurs at open circuit potential, leading to the enrichment of phosphorus on the surface layer. The enrich phosphorus on the coated surface reacts with water from the electrolyte to form a layer of adsorbed hypophosphite anions, which block the supply of water to the electrode surface. It prevents the hydration of nickel, which forms a passive nickel film. In general, electroless Ni-P is a barrier coating, which protects the substrate surface by sealing off from the corrosive environment. The corrosion resistance of electrolessly coated surface depends on the amorphous nature and passivity. Amorphous alloy offers better corrosion resistance as compared to crystalline or polycrystalline materials because of freedom from grain/grain boundaries and glossy film which is formed and passivate their surfaces.
The studies of the corrosion behavior of electroless nickel coating are mainly conducted through electrochemical tests, namely, potentiodynamic polarization studies and electrochemical impedance spectroscopy. The resistance of the coatings towards corrosion is evaluated on the basis of the corrosion parameters obtained from corrosion potential (Ecorr), corrosion current density (Icorr), charge transfer resistance (Rct), double-layer capacitance (Cdl), and corrosion rate (Rc), etc. The present study deals with the evaluation of corrosion behavior of the Ni- P-Al2O3 composite coating, with the help of potentiodynamic polarization tests. The Taguchi method together with grey relational analysis is employed to optimize the process parameters in order to identify the combination of parameters that induce the maximum corrosion resistant properties in the coating. Analysis of variance (ANOVA) is employed to observe the level of significance of the factors and their interactions. In the last, validation of the result obtained through the analysis is done with the help of confirmation test. The surface morphology and composition of Ni-P-Al2O3 coatings are studied with the help of scanning electron microscopy (SEM), energy dispersed X-ray analysis (EDX) and X-ray diffraction analysis (XRD).
Experimental details
Preparation of composite coating
Effective deposition of coating on the substrate depends on the preparation of the substrate, hence it is essential to prepare the substrate surface carefully and properly. In the present study mild steel (AISI 1040) of size 20 mm × 20 mm × 2 mm is used as substrate material for Ni-P-Al2O3 composite coatings. Shaping, parting, milling processes are used accordingly for the preparation of the sample. The sample is then subjected to surface grinding process. The substrate is mechanically cleaned from foreign matters and corrosion products. After that the mild steel substrate is cleaned using distilled water. Sequentially a pickling treatment is given to the substrate with dilute (50 %) hydrochloric acid for short duration to remove any surface layer formed like rust followed by rinsed with distilled water and methanol cleaning. The substrate is activated by dipping into a warm palladium chloride solution (55 °C). This step is necessary to start the deposition on the substrate as soon as it is placed inside the electroless bath. The activated substrate is then immersed into the electroless bath maintained at 85 °C, and the coating is carried out for a period of three hours.
Fig. 1 shows the experimental set up for electroless Ni-P-Al2O3 composite coating.
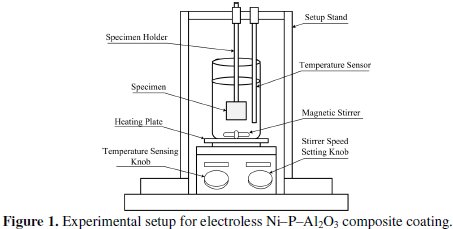
It consists of heater and magnetic stirrer (IKA® RCT basic) with temperature ranges from 0 to 310 °C and stirrer speed ranges from 0 to 1500 rpm. A rigid stand is provided to hold and support the substrate and glass coated temperature sensor. Glass beaker (250 mL size) contained with electroless bath (200 mL) is provided on the heating plate. The bath temperature is set with the help of temperature sensing knob, and stirrer speed can be set with the help of the stirrer speed setting knob. The function of the magnetic stirrer is to maintain the composite particles in suspension without agglomeration in bottom of glass beaker. The stirrer speed can be fixed after large number of trials to avoid the instability of the electroless bath due to agglomeration of particles. The bath composition and operating conditions for electroless Ni-P-Al2O3 composite coatings are selected after several experiments, and proper ranges of the parameters are chosen accordingly. The three most important parameters are varied and others are kept constant for coating deposition. The electroless bath composition and operating conditions used for the deposition electroless Ni-P- Al2O3 composite coatings are shown in Table 1.

To have better dispersion of second phase alumina particles and to avoid agglomeration of particles, a given amount of surfactant SDS (Sodium Dodecyl Sulphate) is added to the electroless nickel poly alloy bath. About 50 mL of electroless nickel solution containing required amount of alumina powder are thoroughly mixed with the help of PTFE magnetic stirrer. Magnetic stirrer (Remi make 2MLH) is used to get uniform suspension of particles in the solution. At first a Ni-P layer is deposited for 1 hour to prevent the porosity of the coating and then the solution containing Al2O3 particles is introduced into the same bath for the subsequent 2 hours for Ni-P-Al2O3 co-deposition.
During chemical reaction the nickel sulphate, which is used as source of metallic ions, supplies the nickel ions in the solution, while sodium hypophosphite (used as a reducing agent) reduces the nickel ions from their positive valence state to zero valence state. But as the reaction between nickel sulphate and sodium hypophosphite is quite fast and intense, instant decomposition of the bath is inevitable. Hence, complexing agents (tri sodium citrate and sodium acetate) are required to slow down the reaction into a viable form. Complexing agents form meta-stable complexes with nickel ions and release them slowly for the reaction, which helps to maintain the stability of electroless bath. But even after the addition of complexing agents, there remains a possibility of instability of the solution. Hence, a stabilizer (Lead acetate) is needed so that the solution remains stable for the duration of the coating. To increase the wettability and surface charge of Al2O3 particles surfactant, sodium dodecyl Sulphate (SDS) is used. The important functions of surfactant are to lower the surface tension of liquid, easier spreading of the particles, and reduce the interfacial tension between the solid and liquid surfaces. It reduces the agglomeration of the particles and electrostatic adsorption of suspended particles on the substrate [20]. The coating thickness is found to lie in the range of 28-32 microns. After coating is over, the samples are cleaned with distilled water. To understand the effect of heat treatment on corrosion resistance of the composite coatings, the coated samples are annealed in a box furnace for 1 hr at different temperatures (300 °C, 400 °C and 500 °C) according to the Orthogonal Array (OA). After annealing, the samples are cooled to room temperature without the application of any artificial cooling.
Optimization of process parameters
In composite coating there are several factors which have impact on characteristics of coating like as nickel source concentration, reducing agent concentration, pH of the solution, bath temperature, stabilizer and wetting agent concentration, concentration of second phase particles, substrate, etc. To obtain an optimum combination for maximum corrosion resistance the various coating parameters are varied within the specific range. However, from literature review it is clear that the three factors, viz., concentration of nickel source (nickel sulphate solution, A), concentration of reducing agent (sodium hypophosphite solution, B), and concentration of second phase particles (Al2O3 powder, C), are the most commonly used by the researchers to control the properties of composite coatings [20-22]. Moreover, annealing is found to have a great effect on the corrosion resistance of the coating. Thus, annealing temperature (D) is taken into account as the fourth parameter in the experimental design to study its effect on the corrosion resistance of the coating. The considered design parameters, together with their levels, are shown in Table 2.
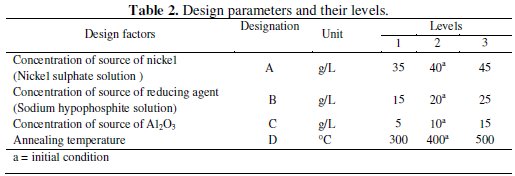
To obtain the desired performance characteristics of the many engineering problems, optimization is essential. These problems are dealt with the optimization of design parameters to achieve better or desired performance. Taguchi design technique is one of the optimization techniques, which is simple in use and robust in design. It consists of system design, parameter design, and tolerance design. Scientific and engineering information required to produce a part is given by the system design. Parameter design suggests the optimum combination for process parameter level by analyzing tolerance for developing quality characteristics. Hence, an attempt has been made to optimize the corrosion behavior of electroless Ni-P-Al2O3 composite coating using grey based Taguchi method [23]. The concept of this method is the optimization of process parameters with high quality and low cost. The method recommends the use of loss function to measure the quality characteristics. The value of the loss function is transformed into a statistical measured called signal to noise ratio (S/N ratio). It is the ratio of mean (desirable value or signal) to standard deviation (noise). S/N ratio can effectively consider the variation encountered in a set of trials. Based on the objective of the study, the S/N ratio characteristics can be divided on the basis of three criteria: lower-the-better (LB), higher-the better (HB) and nominal-the best (NB). A larger S/N ratio represents minimization of noise factors. The combination of parameter levels which gives maximum S/N ratio are known as optimum combination of parameter levels.
The present study deals with evaluation of corrosion characteristics by measuring the corrosion current density and corrosion potential. Due to corrosion potential and corrosion current density, it becomes a complex multivariate problem and cannot be solved by the Taguchi method single-handedly. Because higher S/N ratio of one response may correspond to the lower S/N ratio of other. Grey relational analysis is an effective tool, which can be employed for the overall evaluation of the S/N ratio to optimize the multiple response characteristics. The grey system theory was first proposed by Deng in 1989 [24]. Any system in nature is neither full of accurate information (white system) nor completely lack of information (black system). Mostly the system consists of partial information (grey system, which is the mixture of white and black system). The optimization of the process is performed in various steps as follows:
• The result of the experiments is normalized in the range of zero and one by performing the grey relational generation.
• The normalized data represent the correlation between desired experimental data and actual experimental data. With the help of normalized data the grey relational coefficients are calculated.
• By averaging the grey relational coefficients the grey relational grade is calculated. The grey relational grade is treated as the overall response of the process instead of the multiple responses of corrosion potential and corrosion current density.
A statistical analysis of variance (ANOVA) is performed to find the significant parameters of the experiment. With ANOVA and grey relational analysis, the optimal combination of the process parameters can be predicted. In the last, a confirmation test is conducted to verify the optimum process parameters obtained from the analysis.
In the present study, corrosion behavior of electroless Ni-P-Al2O3 composite coating is studied with the help of potentiodynamic polarization characteristics. Corrosion potential (Ecorr) and corrosion current density (Icorr) are obtained from the Tafel extrapolation of the polarization curve. Ecorr and Icorr are taken as the response variables for the current density. A positive (nobler) Ecorr value and a lower Icorr value indicate that the coating under test has higher corrosion resistance.
The design of experiment of the present study includes an orthogonal array based on Taguchi method to reduce the number of experiments for the optimization of the coating process parameters for corrosion characteristics. The selection of orthogonal array plays important role to complete the experiment successfully. An OA allows one to compute the total degree of freedom (DOF) of main and interaction effects via a minimum number of experimental trials. As it is a three level four factor experiment the total DOF considering the individual factors and their interaction is 20. Hence the L27 OA is chosen which has 27 rows corresponding to the number of experiments and 26 DOF with 13 columns. The L27 OA is shown in Table 3.
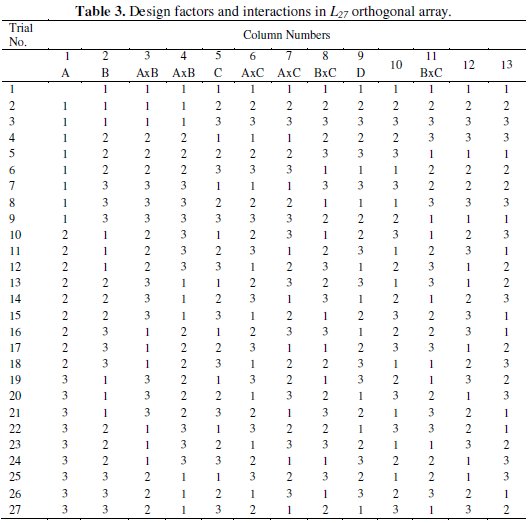
Each row in the table represents the specific combination of experimental run and each column represents a specific factor or interactions. The cell value indicates the level of corresponding factor or interaction assigned to that column. The experimental run is controlled by the setting of the design factors and not by the interactions.
Potentiodynamic test and microstructure study
The potentiodynamic polarization tests of heat treated electroless Ni-P-Al2O3 composite coated samples are carried out using a potentiostat (Gill AC) of ACM instrument, UK. The tests are conducted by using 3.5% NaCl solution as electrolyte at ambient temperature of 30 °C. The electrochemical cell consists of three electrodes. A saturated calomel electrode (SCE) is used as reference electrode, which provides a stable 'reference' against which the applied potential may be accurately measured. A platinum electrode is worked as counter electrode or auxiliary electrode, which provides the path for the applied current into the solution. The coated specimen is used as working electrode, which actually is the sample being interrogated. The design of the cell is such that only an area of 1 cm2 of the coated surface is exposed to the electrolyte. The experimental set of potentiodynamic polarization test is shown in Fig.2.
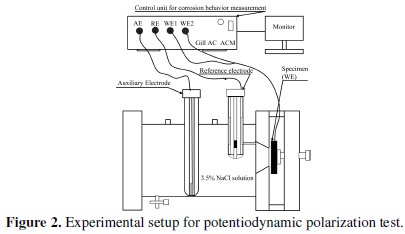
A settling time of 15 minutes is assigned before every test in order to stabilize the open circuit potential (OCP). The potentiostat is controlled with the help of personnel computer which also stores the polarization data. The polarization curve is obtained from dedicated software, which also possesses a special tool in order to extrapolate the values of corrosion potential and corrosion current density from the plot. A Tafel ruler is provided with associated software to measure the corrosion potential and corrosion current density. A horizontal ruler is matched at the junction of cathodic and anodic branch. This point gives the value of corrosion potential and the corrosion current density is obtained by extrapolating the fitting lines of the anodic and cathodic branches of the Tafel curve.
The weight percentage of nickel, phosphorus, aluminum oxide, and oxygen in the composite coating is verified by using energy dispersive X-ray analysis (EDAX Corporation). Scanning electron microscope (JEOL, JSM-6360) is used to observe the surface morphology of the composite coating before and after the heat treatment. This is done in order to analyze the effect of heat treatment on the electroless Ni-P-Al2O3 composite coatings. The phase compositions of composite coatings before and after heat treatment are detected by using an X-ray diffraction analyzer (Rigaku, Ultima III).
Results and discussion
Surface morphology and characterization of the composite coating
Fig. 3 shows the SEM micrographs of as deposited and heat treated Ni-P-Al2O3 composite coating.
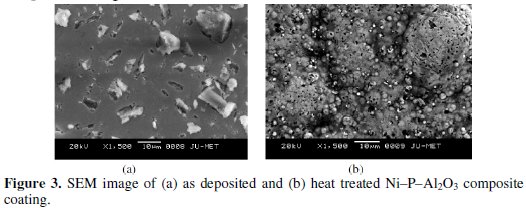
From the figure it is clear that the coated surface has smooth surface with almost uniform distribution of alumina particles over the coated surface without any porosity. It is due to the presence of the surfactant (SDS) in the electroless bath. When the composite coating is heat treated at 400 °C for one hour, the globules of nickel and phosphorus are seen with embedded alumina particles. The globules become more compact, which further reduced the porosity of the coating. It may result into increase in corrosion resistance of the composite coating.
Fig. 4 shows the EDAX analysis of as deposited Ni-P-Al2O3 composite coating.
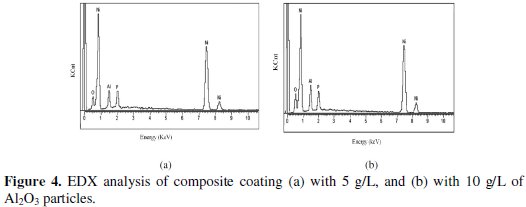
The EDAX analysis is done on the coatings developed from the bath consisting of different concentration of nickel sulpahte, sodium hypophosphite, and Al2O3 particles.
From analysis it is confirmed that the composite coating consisting of 5 g/L of Al2O3 particles has 78.07 wt% of nickel, 6.67 wt% of phosphorus, 8.74 wt% of oxygen, and 6.52 wt% of alumina particles. Similarly the composite coating with 10 g/L of Al2O3 particles has 72.46 wt% of nickel, 6.92 wt% of phosphorus, 11.06 wt% of oxygen, and 9.56 wt% of alumina particles. It indicates that the alumina content in the composite coating is increased with increase in Al2O3 particles in the electroless bath.
An X-ray diffraction (XRD) analyzer (Rigaku, Ultima III) is used for identification of the different compounds in the electroless Ni-P-Al2O3 composite with and without heat treatment. Figure 5 shows the XRD plots of as deposited and heat treated composite coatings.
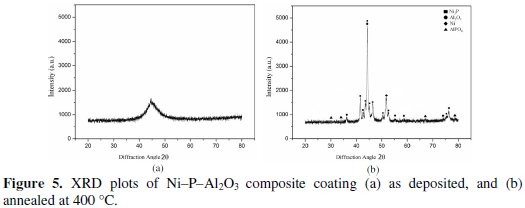
From the figure it is seen that in as deposited condition the phase is mostly amorphous in nature as single broad peak is available at the diffraction angle of 44.468. After heat treatment at 400 °C for one hour, the amorphous phase of composite coating gets converted into crystalline phase. Different peaks are seen at different diffraction angles. The highest peak of Ni3P with Al2O3 is observed at the diffraction angle of 44.320. Ni3P peaks are also observed at the diffraction angles of 43.1, 43.5, 43.74, 44.26, and 45.04. Similarly peaks of Al2O3 are observed at diffraction angles of 37.06, 53.46, 55.7, and 77.28. Peaks of Ni are observed at diffraction angles of 52.18, and 77.38.
Optimization of process parameters and validation test
The present investigation deals with two responses, namely corrosion potential and corrosion current density for optimization of corrosion resistance of Ni-P- Al2O3 composite coatings. Grey analysis is a method which converts multivariable (response) problem into single response (variable) problem. The experimental values of corrosion potential (Ecorr) and corrosion current density (Icorr) from potentiodynamic polarization test are given in Table 4.
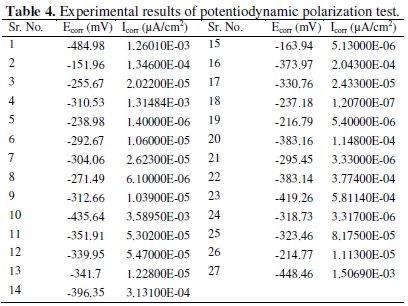
The specific set of calculations are performed to convert the given multiple responses into a single performance index also called as grey relational grade.
Linear normalization of the experimental results, i.e., corrosion potential and corrosion current density, in the range of zero and one are essential for generating the grey relational coefficient. A material will have lower tendency to corrosion if Ecorr value tends to be positive and lower value of Icorr. From Table 4 it is clear that the values of corrosion potential for all experiments are negative, hence higher the better criterion is used for normalization. Similarly for all positive values of corrosion current density, lower the better criterion is used for normalization. The expressions for higher the better and lower the better criterion are given as below.
Equation for higher the better:

Equation for lower the better:

where xi( k ) is the value after grey relational generation, while min yi( k ) and max yi( k ) are the smallest and largest values of yi( k ) for the kth response. The data after grey relational grade are shown in Table 5.
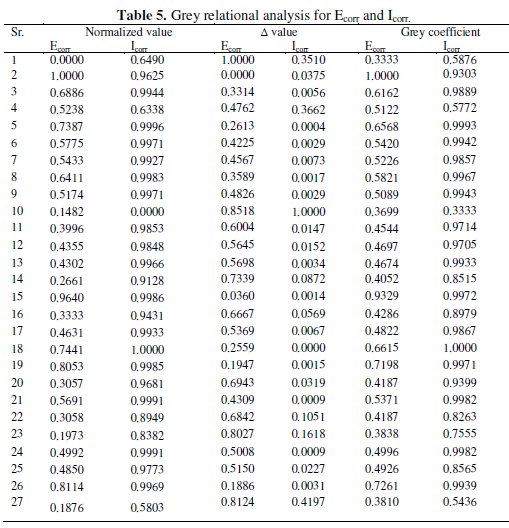
The grey relational coefficient is calculated from the normalized value and the equation for grey relational coefficient is as follows.

where Δoi = ǁ xoi( k ) - xi( k ) ǁ is the difference of the absolute value between xoi( k ) and xi( k ). Δmin and Δmax are the minimum and maximum values of the absolute differences (Δoi) of all comparing sequences. The grey relational coefficients are calculated for the experimental data using ξ = 0.5. The values of grey relational coefficients are shown in Table 5.
The overall multiple response characteristics evaluation is based on grey relational grade and is calculated as follows

where n is the number of process responses. The grey relational grades are considered for the optimization of multi response parameter design problem. The values of grey relational grades with their order are shown in Table 6.
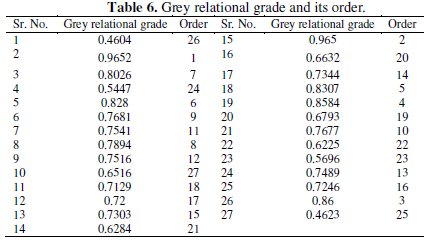
To optimize the process parameters for high quality with low cost, Taguchi method is the most suitable method. This method uses S/N ratio to convert the experimental results into a value for the evaluation characteristics in the optimum parameter analysis. Here signal stands for desirable or mean value and noise tands for undesirable value (SD). A larger S/N ratio represents a better quality characteristic because of the minimization of noise and corresponding process parameters are incentive to variation of environmental conditions and other noise factors. The S/N ratio is maximized to reduce the effect of random noise factors and to significant effect on the process parameters.
Since the grey relational grade has to be maximized, the S/N ratio is calculated using higher the better criterion which is given by:

where y is the observed data and n is the number of observations. As the experimental design is orthogonal, it is possible to separate out the effect of each coating parameter at different levels. The mean grey relational grade for three levels of the four factors is summarized in Table 7.
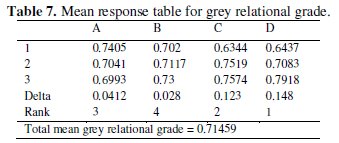
All the calculations are performed using Minitab software [25]. The response table shows the average of the selected characteristic for each level of the factors. The ranks shown in the table are based on Delta statistics and it compares the relative magnitude of effects. The Delta statistics is the difference of highest average and lowest average of each factor. Ranks are assigned on the basis of Delta values; rank 1 is assigned to the highest Delta value, rank 2 is assigned to next highest value, and so on. Fig. 6 shows the main effects plot for mean of grades and Fig. 7 shows the interaction plots between the process parameters.
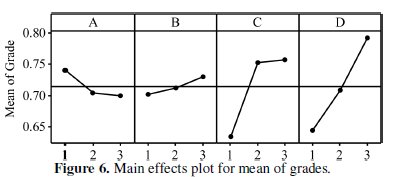
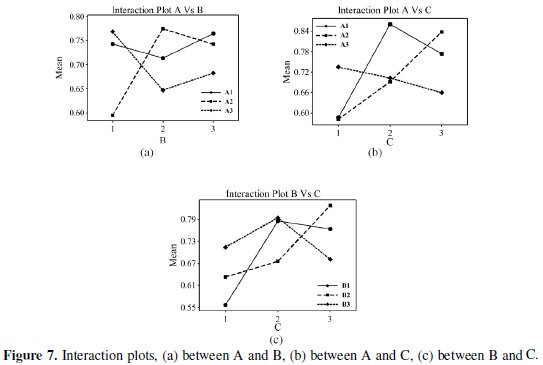
In the main effects plot if the line for particular parameter is horizontal, then the particular parameter has no significant effect. On the other hand, a parameter for which the line has maximum inclination will have the most significant effect. From the main effect plot it is clear that parameter D (annealing temperature) has the most significant effect and parameter C (concentration of Al2O3 particles) also has a significant effect. Increase in corrosion resistance of composite coating with introduction of Al2O3 particles has also been observed earlier. In Ni-P- (Al2O3-TiC) composite coating, the corrosion rate and corrosion current are less as compared to the Ni-P coating [6]. In other case [3], the authors have observed that corrosion resistance is inreased with increase in Al2O3 particles. Parameters A and B are less significant due to less inclination to the horizontal line.
Fig. 7 shows the interaction between parameters A, B, and C. From plot it can be seen that the lines intersect in all plots, i.e., all factors have some amount of interaction between each other. From the interaction plot it can be observed that strong interaction between parameter B and C and between parameter A and C occurs. Hence from the present analysis it is confirmed that annealing temperature and concentration of Al2O3 particles are the significant parameters for the corrosion characteristics of Ni-P-Al2O3 composite coatings. In Taguchi method optimum level of combinations are selecting for those levels, which are having higher S/N ratios. In the present study the optimal combination is found to be A1B3C3D3.
In the main effects plot if the line for particular parameter is horizontal, then the particular parameter has no significant effect. On the other hand, a parameter for which the line has maximum inclination will have the most significant effect. From the main effect plot it is clear that parameter D (annealing temperature) has the most significant effect and parameter C (concentration of Al2O3 particles) also has a significant effect. Increase in corrosion resistance of composite coating with introduction of Al2O3 particles has also been observed earlier. In Ni-P- (Al2O3-TiC) composite coating, the corrosion rate and corrosion current are less as compared to the Ni-P coating [6]. In other case [3], the authors have observed that corrosion resistance is inreased with increase in Al2O3 particles. Parameters A and B are less significant due to less inclination to the horizontal line.
Fig. 7 shows the interaction between parameters A, B, and C. From plot it can be seen that the lines intersect in all plots, i.e., all factors have some amount of interaction between each other. From the interaction plot it can be observed that strong interaction between parameter B and C and between parameter A and C occurs. Hence from the present analysis it is confirmed that annealing temperature and concentration of Al2O3 particles are the significant parameters for the corrosion characteristics of Ni-P-Al2O3 composite coatings. In Taguchi method optimum level of combinations are selecting for those levels, which are having higher S/N ratios. In the present study the optimal combination is found to be A1B3C3D3.
The influence of the process parameters on corrosion resistance of the coating and significance level of the process parameters can be investigated with the help of ANOVA. Analysis of variance is a statstical technique which can provide some important conclusions based on analysis of the experimental data. ANOVA separates the total variability of the response into contribution of each of the factors and the error. The results obtained through ANOVA with the mean grey relational grade are performed using Minitab software. ANOVA results for potentiodynamic behaviour of the composite coatings are shown in Table 8.
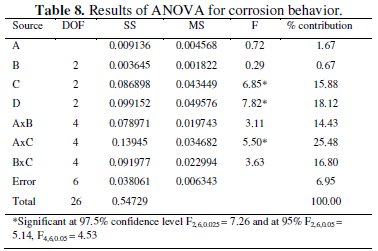
ANOVA calculations are based on the F-ratio, also called as the variance ratio: the ratio between variance due to change in the process parameter levels and the variance due to experimental error. It is used to measure the significance of the parameters under investigation with respect to variance of all the terms included in the error term at the desired significance level. If the calculated value is higher than the tabulated value, then the factor is significant at the desired level. In general, if the F value increases, the significance of the parameter also increases. The ANOVA table shows the percentage contribution of each parameter. From the table it is observed that parameter D, i.e., the annealing temperature, has the most significant effect on the potentiodynamic behaviour at the confidence level of 97.5% within the specific test range. The concentration of Al2O3 particles (C) is also significant at the 95% confidence level. Among the interactions, the interaction of parameters between A and C has the significant contribution. The percentage contribution of the factors and interactions is calculated to know the influence of the process parameters. From ANOVA's table it is clear that parameter D has the largest contribution (18.12%) followed by parameter C (15.88%). Among interactions, A×C interaction has highest contribution (25.48%) followed by B×C (16.80%).
Validation of the result of optimum parameters calculated by Taguchi method is the final step. The confirmation experiment is performed by conducting the experiment with optimal setting of the factors and levels previously calculated.
The predicted value of S/N ratio at the optimum level his calculated as

where ηm is the total mean grade, η is the mean grade at optimal level, and o is the number of main design parameters that significantly affect the corrosion resistance of Ni-P-Al2O3 composite coating.
The results of the validation test in the present study are shown in Table 9.
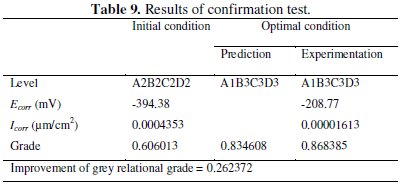
The improvement of grey relational grade from initial to optimal condition is 0.262372, which is about 36.72% of the mean relational grade and is a significant improvement. The polarization curves for the Ni-P-Al2O3 composite coatings developed at initial and optimal condition are shown in Fig. 8.
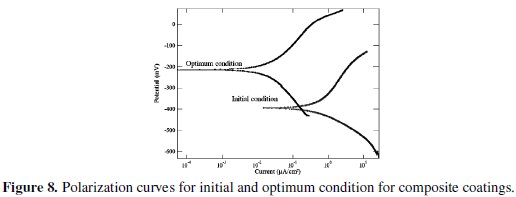
Conclusion
In the present study, Taguchi method in combination with Grey relational analysis is used in order to optimize the electrochemical characteristics of electroless Ni-P-Al2O3 composite coating via potentiodynamic polarization in 3.5% NaCl solution. The optimum parameter combination is found to be A1B3C3D3. At optimum combination nickel concentration is 35 g/L, reducing agent concentration is 25 g/L, concentration of Al2O3 particles is 15 g/L, and annealing temperature is 500 °C. From ANOVA results it is confirmed that annealing temperature and concentration of Al2O3 particles have most significant influence on potentiodynamic behavior of composite coating. The interaction between nickel source and concentration of Al2O3 particles has the maximum significance among the interactions. The corrosion resistance of the composite coating improves with increase in alumina content and annealing temperature higher than 400 °C. The improvement of grey relational grade from initial condition to the optimal condition is found to be 36.72%. The coating composition is studied by EDX analysis. The micro structural analysis and crystallization behavior of the coating is studied with the help of SEM and XRD analysis. From SEM micrograph it is clear that the alumina particles are uniformly distributed over the smooth coated surface without porosity. From EDX analysis it is confirmed that the coating is composite coating with the presence of alumina particles, nickel, phosphorus, and oxygen. The XRD plots reveal that the as deposited composite coating is amorphous in nature and it converts into crystalline structure after heat treatment at 400 °C with Ni3P as a major compound.
References
1. Balaraju J N, Narayanan T S N S, Seshadri S K. J Appl Electrochem. 2003;33:807. [ Links ]
2. Sudagar J, Lian ., Sha W. J Alloys Compd. 2013;571:183. [ Links ]
3. Sharma A, Singh A K. J Mater Eng Perform. 2013;22:176. [ Links ]
4. Sahoo P, Das S K. Mater Design. 2011;32:1760. [ Links ]
5. Apachitei I, Tichelaar F D, Duszczyk J, et al. Surf Coat Tech. 2001;148:284. [ Links ]
6. Abdel Aal A, Zaki Z I, Hamid Z A. Mater Sci Eng A. 2007;447, 87. [ Links ]
7. Balaraju J N, Narayanan T S N S, Sheshadri SK. Mater Res Bull. 2006;41:847. [ Links ]
8. Alirezaei S H, Monirvaghefi S M, Salehi M, et al. Surf Coat Tech. 2004;184:170. [ Links ]
9. Riedel W. Electroless nickel plating. Hertfordshire (UK):Stevenage, Finishing Publications Ltd; 1991. [ Links ]
10. Araghi A, Paydar M H. Mater Design. 2010;31:3095. [ Links ]
11. Zarebidaki A, Allahkaram S R. Micro Nano Lett. 2011;6:937. [ Links ]
12. Praveen B M, Venkatesha T V, Naik Y A, et al. Surf Coat Tech. 2007;201:5836. [ Links ]
13. Zarebidaki A, Allahkaram S R. Micro Nano Lett. 2012;7:90. [ Links ]
14. Allahkaram S R, Alivand R F, Bakhsh M S. Iran J Mater Sci Eng. 2013;10:10. [ Links ]
15. Momenzadeh M, Sanjabi S. Mater Corros. 2012;63:7. [ Links ]
16. Rabizadeh T, Allahkaram S R. Mater Design. 2011;32:133-138. [ Links ]
17. Lee C K. Int J Electrochem Sci. 2012;7:8487. [ Links ]
18. Lee C K. Int J Electrochem Sci. 2012;7:12941. [ Links ]
19. Novakovic J, Vassiliou P. Electrochim Acta 2009;54:2499. [ Links ]
20. Liu D, Yan Y, Lee K, et al. Mater Corros. 2009;60:690. [ Links ]
21. Sahoo P. J Phys D: Appl Phys. 2008;41:095305. [ Links ]
22. Das S K., Sahoo P. Adv Mechan Eng. 2012;703168. [ Links ]
23. Roy R K. A primer on the Taguchi method. Ann Arbor, Mich, USA:Dearborn, Society of Manufacturing Engineers;1990 [ Links ]
24. Deng J. Introduction to Grey System, J Grey System. 1989;1:1.
25. Minitab user manual (release 13.2). Making data analysis easier. MINITAB Incorporation, State College, PA, USA;2001. [ Links ]
*Corresponding author. E-mail address: psjume@gmail.com
Received 16 April 2014; accepted 23 April 2014