Introduction
Metal oxides are very important technological materials. Most often, they are of great interest as catalysts in chemical reactions, as well as functional coatings in electronic and photonic devices.
Among metal oxides, CuO (II) is particularly important. Therefore, detailed reviews of its production methods and applications are presented in literature. Especially, great attention is paid to NP of CuO (II). They are used in catalysis, gas sensors, magnetic data carriers, batteries and solar energy transformers. Since CuO (II) exhibits unique characteristics, it is used as dye for antifouling paints, SC and sensors 1,2. Researchers 3 have used CuO (II) as electrodes for thin-film batteries. They were applied by direct I, at low E, to obtain films with NP. Many scientific papers are devoted to the study of CuO (II) catalytic properties.
For instance, 4 have used CuO (II) as catalyst for CO oxidation into CO2. This was first achieved on CuO, without substrate, which was prepared by controlled heating of precipitated Cu(OH)2, after the catalyst activation in a redox medium. 5 have shown it is possible to use CuO for CO2 Ec reduction. At the same time, electrode toxicity was found to be averted, by using CuE in electrolysis pulsed mode, with anodic and cathodic polarization. Anodic polarization intervals suppressed toxic substances deposition on the electrode. There are also studies showing CuO antimicrobial effect 6.
Since CuO is of great interest in engineering and industry, scientists and technologists have been researching methods for its synthesis. Literature mainly describes methods related to NP production, such as chemical reduction, Ec, hydrothermal, microwave irradiation, photochemical, sol-gel, solid-phase, solvothermal and sonochemical techniques 7.
Currently, among the various methods for obtaining Cu compounds, Ec techniques are of considerable interest. For example, CuO (II) has been obtained by electrolysis, using Cu anodes in an aqueous solution containing 60-75 g/L Na2SO4 and 10-20 g/L Na₂CO₃, or 80-125 g/L Na2SO4 and 20-35 g/L Na₃PO₄ 8.
However, direct I application is challenging. During electrolysis, under direct I, an I rectifier must be introduced into the circuit. Thus, additional space and maintenance costs are required. The process is carried out at relatively high j, while Cu anode passivation takes place, and electrolysis may be shortened, which can hinder the process.
9 has described methods for obtaining oxides from several metallic materials, using Ec processes that involve metal electrodes destruction under AC, at very high j. However, CuO (II) production CE did not exceed 2%.
The aim of the present work was to study CuE dissolution process in aqueous SO4 2- solutions under AC, and to develop an effective method for obtaining CuO (II).
Experimental
The main experimental methods were CV and electrolysis under AC. CV were recorded using an Autolab PGSTAT302N (Utrecht, the Netherlands) potentiostat in a thermostated three-electrode cell (Metrohm 663 VA Stand (Herisau, Switzerland)), with separated electrode spaces, using IPC 2000 program installed on a personal computer. The WE, AE and RE were a Cu plate (99.99%) (LD Didactic GmbH), a Pt wire and an AgCl electrode (immersed in a saturated solution of KCl: E = +203 mV), respectively. Before the study, the electrodes surfaces were cleaned with Matrix 1000, abraded with Mirka Finland 2000 sandpaper, washed with distilled water and degreased with ethanol. After each WE immersion in KCl, the stripping process was repeated. Distilled water obtained using an electric DE-M (Plant LLC “Elektromedoborudovanie”) aquadistillator was used for the solutions preparation. CV were recorded at a T of 25 ºC.
Electrolysis was carried out under industrial AC, at 50 Hz, in a T-controlled glass electrolyzer. I source was a (SOURCE) TDGC29-2KVA (Matrix Technology LLC) laboratory autotransformer. The electrodes were Cu plate (99.99%) and Ti wire (99.70%, LD Didactic GmbH). The interelectrode spaces were not separated. Na2SO4 solution (chemically pure, “Component-Reagent” LLC, Moscow, Russia) was used as electrolyte.
I strength was measured by AC E 538 (Etalon Instrument LLC) ammeter. After the experiment, dispersed CuO (II) powder was produced in the electrolyzer. The precipitate was separated from the solution by filtration, washed with distilled water and dried in a drying cabinet. Then, it was identified by XRD analysis (DRON-4-07, IC “Bourevestnik" JSC, Russia). Elemental analysis was carried out using EDXRF spectroscopy on an INCA Energy 450 energy-dispersive microanalysis system mounted on a SEM (JSM-6610 LV, JEOL, Japan). The determination error was 0.01%.
CuO (II) CE was calculated for one AC half-cycle. During experiments, i effect on CuE (from 1000 to 7000 A/m2) and TiE (from 25 to 150 kA/m2) was determined.
Variations with Ct of Na2SO4 (from 25 to 175 g/L) and I frequency (from 50 to 300 Hz) were also studied. The experiments were carried out for 1 h, at 70 ºC.
Results and discussion
To elucidate the reaction mechanisms during CuE polarization in the SO4 2- electrolyte, CV were recorded in anodic and cyclic modes. Fig. 1 shows anodic CV recorded for CuE in a Na2SO4 solution, at different Ct, in E range from 0.1 to 2.2 V.
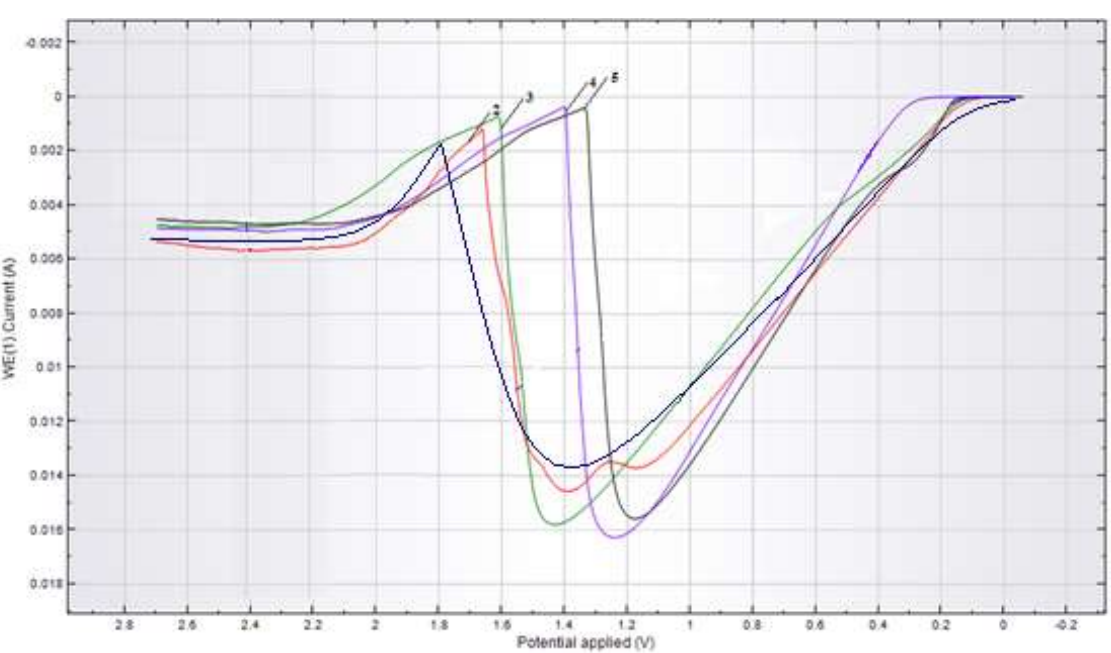
Figure 1: Anodic CV of CuE in Na2SO4 solutions at: Ct between 1-25, 2-50, 3-75, 4-100 and 5-125 g/L; V of 100 mV/s; T of 25 ºC.
Herein, a peak that corresponded to CuE oxidation I was seen. According to (1), in E range from 1.2 to 1.5 V, Cu partial passivation occurred (2).
Cu(OH)2 production on the electrode surface dramatically reduced its oxidation rate. Further, when E reached more positive values, CuE was oxidized in a transpassive mode.
When the Ct of Na2SO4 was increased to 25-125 g/L, I peak magnitude did not change significantly, but E shifted noticeably towards the cathode. CV registered during CuE anodic polarization, with SR at different E, show (Fig. 2) that E also shifted to the cathode side, and that peak height decreased.
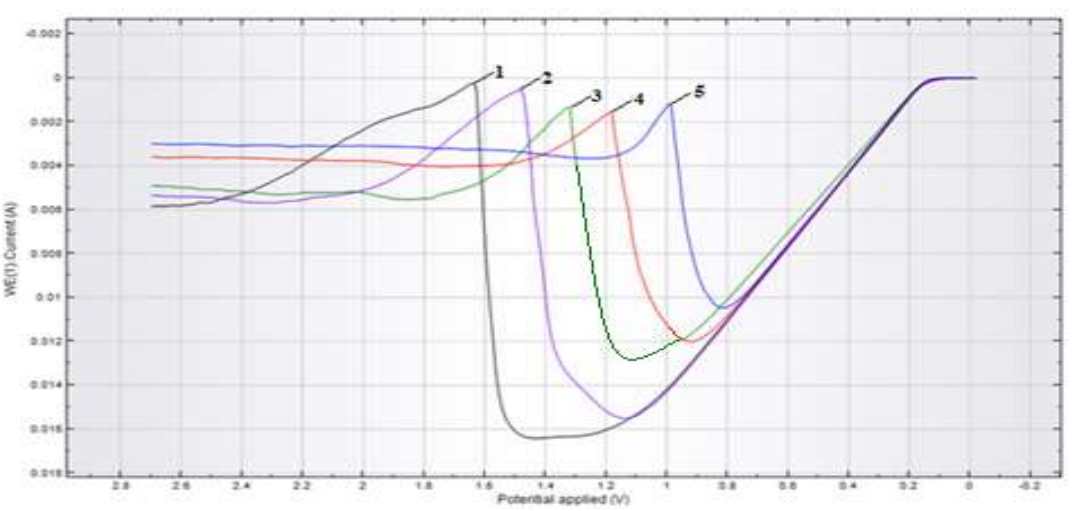
Figure 2: Anodic CV of CuE in Na2SO4 (25 g/L) at: SR between 1-50; 3-100, 4-150 and 5-200 mV/sec; T of 25 ºC.
The decrease in the peak height was apparently due to a change in the electrode surface structure that was associated with Cu(OH)2 production.
When the solution T was changed to 25-70 ºC, the peak height on the anodic CV naturally increased, and E shifted towards the cathode (Fig. 3).
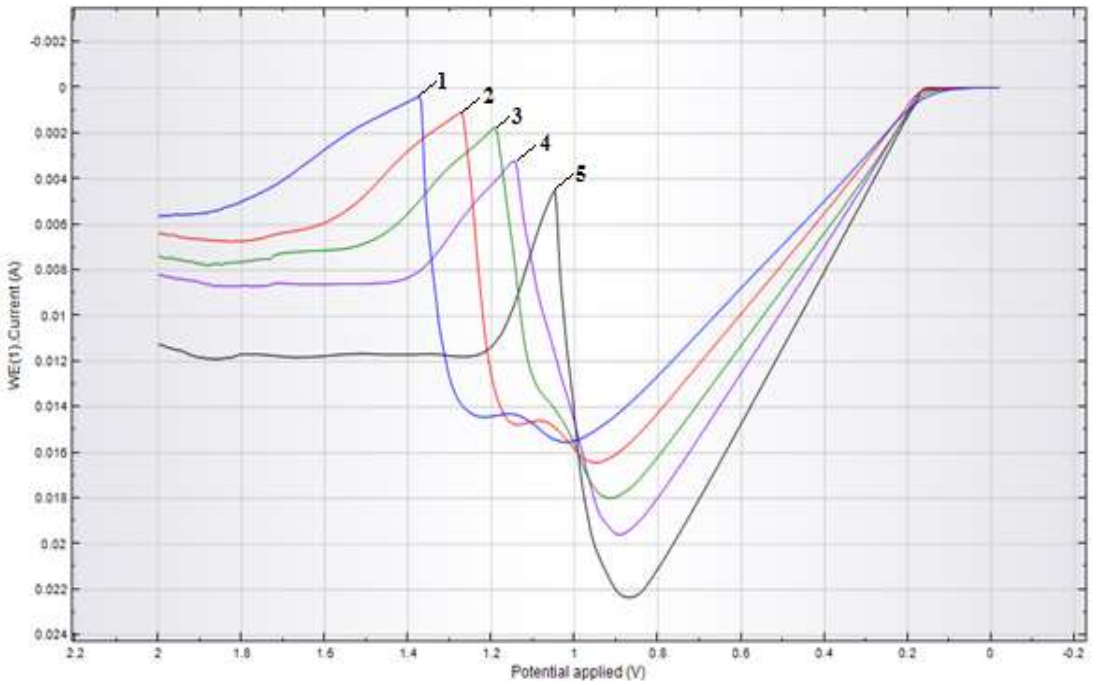
Figure 3: Anodic CV of CuE in Na2SO4 (25 g/L) at: Ct between 1-25, 2-35, 3-45, 4-55 and 5-65 g/L; SR of 100 mV/s; T of 25 ºC.
At T above 50 ºC, CuE surface acquired a black colour associated with CuO (II) production, according to dehydration process (3).
CV obtained in the anodic-cathodic mode (Fig. 4) shows that, when E was shifted towards the anode, CuE oxidation occurred, and a peak was seen.
Then, when E was shifted towards the cathode (0-0.5 V), Cu(OH)2 reverse reduction occurred. This reaction caused a smooth wave on the cathodic branch. In CuE cathodic-anodic CV (Fig. 5), H production I was observed on the cathodic branch, at E of -1.75 V and above. CuE oxidation I was observed on the anodic branch.
CuE oxidation in Na2SO4, during AC polarization, was accompanied by CuO (II) precipitate production in the electrolyte, which is explained as follows: in the anodic AC half-cycle, an oxide film of variable compositions was produced on TiE; oxide films produced in air, under normal conditions, basically correspond to TiO2, with some additional O; the oxide film production in anodic AC half-cycle was like the process occurring during anodic polarization by direct I.
According to literature, during anodic polarization, E of Ti immediately turns positive, and the metal is passivated (10, 11). At the same time, in neutral, slightly acidic, alkaline and oxidizing media, at E up to +2V, films of mixed oxides (Ti2O3 and TiO2) are produced on the Ti surface, where Ti5O9 and Ti6O11 predominate. This film has SC (gate) properties, due to which electric I flow in the circuit stops. With AC, in contrast to the polarization process by direct I, I direction changes.
So, when TiE is in anode half-cycle, and oxide films are produced on it, CuE is in cathode half-cycle, and practically no Ec reaction occurs on it. At the next shift in I direction, when TiE is in cathode half-cycle (TiO with SC properties only have I towards the cathode), H gas is released on it (4), and there is also a partial TiO film reduction:
At this moment, CuE is in anodic half-cycle, and it is oxidized according to (1).
It is noteworthy that, in cathodic half-cycle, H release reaction occurs, and OH¯ ions are formed. The electrolyte medium becomes alkaline, and its pH is higher than 7. Cu(OH)2 hydrate formation pH is achieved. Also, Cu(OH)2 has low Ksp value (2.2·10-20). Therefore, this compound is formed (2).
Cu(OH)2 undergoes dehydration, depending on conditions (i.e., at T above 60 ºC), and CuO (II) is produced 12,13 (3).
Thus, when I direction shifts, (1) and (4) are periodically and cyclically repeated every 50 s, and the process ends (2).
It should be noted that, when polarized by industrial AC, at a frequency of 50 Hz, I direction changes every 50 s. Each electrode is alternately polarized in the anodic direction, then in the cathodic one. In this regard, cathodic and anodic half-cycles concepts were herein used.
When i at TiE changed from 0 to 75 kA/m2 (Fig. 6), CuE dissolution CE increased up to 96.5%. However, within i values from 75 to 150 kA/m2, CE decreased sharply. The i (75 kA/m2) effect on CuE dissolution CE, was studied.
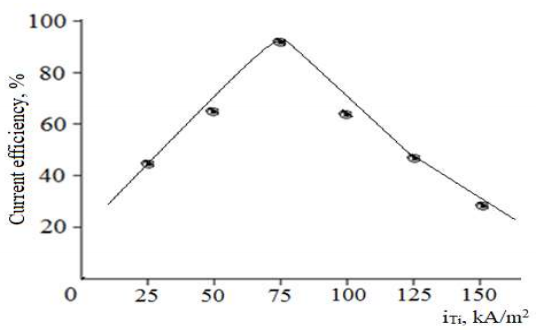
Figure 6: Effect of j (1000 A/m2), at TiE, on CuE dissolution CE in 70 g/L Na2SO4 at: T of 70 ºC; time of 1 h.
As seen from Fig. 6, when i changed from 250 to 500 A/m2, CE was only 25-55%. When i was increased to 1000 A/m2, Cu dissolution CE exceeded 90%. However, this index slightly decreased with further polarization.
It has been herein shown how i on the electrodes affected CuE dissolution CE. CuO (II) production was directly related to CuE dissolution. So, it can be said that, with an increase in CuE dissolution CE, CuO (II) production was higher.
With an increase in i at TiE (Fig. 7), SC oxide films production rate apparently increased, and its surface structure changed.
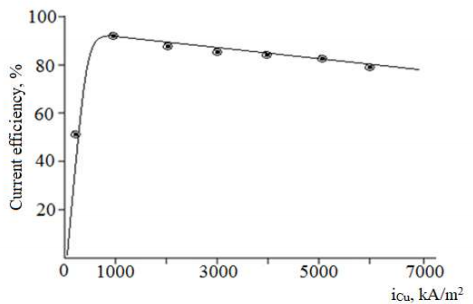
Figure 7: Effect of i (75 kA/m2), at TiE, on CuE dissolution CE in 70 g/L Na2SO4 at: T of 70°C; time of 1 h.
A sharp decrease in CuO (II) production CE, with an increase in i above 75 kA/m2, occurred since looser oxide films with low SC properties were produced on TiE.
The highest dissolution CE (above 90%) was observed at i of 1000 A/m2 on CuE. An upward change in j, from 2000 to 7000 A/m2, did not lead to significant changes in CE (Fig. 8), but only to a slight decrease in this indicator, which is explained by CuE partial passivation, and the occurrence of a side reaction in O release:
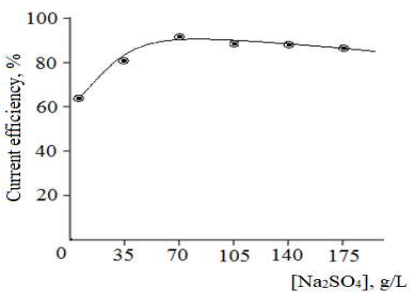
Figure 8: Influence of Na2SO4 C (70 g/L) on CuE dissolution CE and CuO (II) production at: Ti i of 75 kA/m2; Cu i of 1000A/m2; T of 70 ºC; and time of 1 h).
During polarization with direct I, at i of 2000 A/m2 and higher, Cu anode was passivated over time. However, CuE was not passivated during polarization with AC, even at i of 8000 A/m2.
Preliminary experiments carried out at T from 25 to 50 ºC showed that Cu(OH)2 was produced by electrolysis, and its colour was blue, which is characteristic of this compound. When T rose to 60ºC and above, Cu(OH)2 blue (which underwent dehydration) and CuO (II) black precipitates were produced. When T reached 70ºC and above, dehydration instantly occurred, and CuO was immediately produced. Thus, all experiments were carried out at T of 70 ºC.
Experiments conducted at different electrolyte Ct and electrolysis duration showed that CuE dissolution occurred more easily in Na2SO4 (65-75 g/L) (Fig. 3), for 1 h. With increased AC frequency, CuO (II) production CE decreased. As Fig. 9 shows, at 50 and 300 Hz, CE was 90.6 and 49.9%, respectively.
XRD (Fig. 10) and elemental analyses (Table 1) results indicate that CuO was produced.
Table 1: Elemental composition of CuO (II) obtained by industrial AC polarization (according to spectral analysis).
Mass % | |||
---|---|---|---|
Element | O | Сu | Total |
Spectrum 1 | 19,99 | 80,01 | 100,00 |
Spectrum 2 | 20,01 | 79,99 | 100,00 |
Spectrum 3 | 19,98 | 80,02 | 100,00 |
Average content | 19,99 | 80,01 | 100,00 |
The micrograph of the obtained powders shows (Fig. 11) that CuO (II) powders were produced as separated aggregates consisting of ultrafine particles.
Conclusions
This article presents the results of studies on CuE dissolution process in aqueous SO4 2- electrolyte, under AC. A method for obtaining CuO (II) was developed. Ti was used as the second electrode in the electrolysis. CuE intensive dissolution, during polarization by industrial AC with Cu (II) ions production, was achieved. Cu (II) ions in the solution interacted with OH¯ ions, to form Cu(OH)2. With the appropriate conditions, Cu(OH)2 was dehydrated when CuO (II) was produced. CuO (II) production depended mainly on j at TiE. It was established that CuO was produced in the form of an ultrafine precipitate. Favourable conditions to obtain CuO (II) in Na2SO4 (65 to 75 g/L) were i of 75 kA/m2 (at TiE) and 1000 A/m2 (at CuE), with AC of 50 Hz, experiment duration of 1 h and T of 70 ºC. The obtained CuO (II) composition was identified by XRD phase and elemental analyses methods.
Authors’ contributions
A. Bayeshov: determined the purpose and basic concept of the work; theoretically justified the possibility of processes occurring during polarization by industrial AC; developed an electrochemical circuit for electrolysis under AC. A. K. Bayeshova: determined the purpose and basic concept of the work; theoretically justified the possibility of processes occurring during polarization by industrial AC; selected experimental methods and electrode materials; conducted preliminary electrolysis experiments. F. M. Zhumabay: recorded CV; studied the dependence of CuO formation process on various factors. All the authors were engaged in the process of obtaining CuO and studying CuE dissolution conditions.
Acknowledgement
The authors express gratitude to the head of the Laboratory of Physical Research Methods of the Institute of Fuel, Catalysis and Electrochemistry, named after D. V. Sokolskiy, A. R. Brodskiy and research fellow V. I. Yaskevich, for microphotographs obtained with a SEM. This article was written according to the calendar plan of projects АР 088 56 929, funded by the Ministry of Education and Science of the Republic of Kazakhstan.
Abbreviations
AC: alternating current
AE: auxiliary electrode
CE: current efficiency
Ct: concentration
CuE: Cu electrode
CuO: copper oxide
Cu(OH)2: copper hydroxide
CV: cyclic voltammogram
E: potential
Ec: electrochemical
EDXRF: energy-dispersive X-ray fluorescence
I: current
i: current density
KCl: potassium chloride
Ksp: solubility product constant
Na₂CO₃: sodium carbonate
Na2SO4: sodium sulfate
Na₃PO₄: trisodium phosphate
NP: nanoparticles
OH¯: hydroxide ion
Red-ox: reduction-oxidation reaction
RE: reference electrode
SC: semiconductor
SEM: scanning electron microscope
SO4 2-: sulfate-electrolyte
SR: scan rate
T: temperature
TiE: Ti electrode
WE: working electrode
XRD: X-ray diffraction