1. Introducción
En el escenario internacional, las pymes del sector comercial pertenecientes al rubro ferretero no planifican el crecimiento de sus negocios por la falta de habilidades administrativas, además el 50% de estas no consideran prioritario la calidad de los productos y el control de sus inventarios (Maria & Milla, 2017). En el mercado peruano, el 50% de las pymes de este sector desaparecen en el segundo año de su creación, debido a la competitividad del mercado, por lo que si no cuentan con una correcta gestión de almacenes e inventario no podrán desarrollar sus operaciones a lo largo del tiempo (Chau, 2018). El rubro ferretero peruano facturó más de US$ 4 000 millones en el año 2019, aumentando sus ventas en un 6,4% (PRODUCE, 2019). La mayoría de pymes de diferentes países tienen como principal problema el manejo de sus almacenes, cerca del 62,3% tienen dificultades en la previsión de inventario (inexactitudes). por lo que se reduce el nivel de servicio (Nik Ab Halim et al., 2018). Según José Izcúe, gerente general de Senegocia, refiere que el nivel de servicio promedio según la OTIF para las empresas del sector comercial es del 90% como mínimo (Izcúe, 2017).
Por otro lado, de acuerdo con Atnafu y Balda (2018), las micro y pequeñas empresas tienen una deficiente gestión de almacenes, esto se refleja en el flujo de caja de una empresa, por lo que determinaron que la inversión de inventario para una pyme ocupa un gran porcentaje del presupuesto total, sin embargo, el control de inventario es una de las áreas de gestión más descuidadas. La mayoría de las empresas del sector comercial han implementado la herramienta 5S haciendo énfasis en la clasificación, orden y limpieza. Se ha revisado diversos casos de estudios, donde la aplicación de la filosofía Lean en pymes representa 3 variables principales estas son: ahorro de costos, mejora continua y la reducción de residuos, la aplicación de Kaizen ayuda a las pymes en el mejoramiento de su cadena de suministro en un 70% y ejerciendo un programa de mejora continua apoya en un 77% en la eficiencia (Zhou, 2016).
El enfoque principal de este estudio es realizarlo en una pyme del rubro ferretero que presente la problemática. En el caso de estudio analizado se encontraron altos tiempos en sus procesos de recepción, picking y almacenaje, además no cuenta con un correcto orden en sus almacenes, se desconoce el nivel de los inventarios y cuenta con productos obsoletos en sus instalaciones, todo ello provoca que no se atiendan las órdenes de compra en su totalidad. Por ello, para solucionar el problema se desarrolló el “HS Warehouse Managment Deming Model”, teniendo como herramienta principal las 5S y las de soporte como la utilización del ABC multicriterio, SLP, estandarización de trabajo y la sistematización de inventarios mediante un Kardex.
2.Análisis del Problema
Las causas que generan este problema en la empresa son los siguientes: tiempos elevados en el proceso de almacenamiento, retrasos en el proceso de picking y tiempos elevados en el proceso de recepción de productos. Por lo que, se determinó realizar un análisis de valor agregado (AVA), esta es una técnica que examina detalladamente cada fase de un proceso, para determinar si agrega valor, con esta técnica se busca definir los tiempos de cada proceso fundamental para lograr procesos más efectivos, productivos y competitivos (Davila Puente, 2017), los resultados obtenidos de la matriz AVA son los siguientes:
Tabla 1 Situación inicial de los procesos
Proceso | Tiempo que agrega valor | Tiempo que no genera valor | Tiempo total del proceso |
Recepción de pedidos | 159 min | 173 min | 332 min |
Almacenamiento | 279 min | 180 min | 459 min |
Armado de pedido (picking) | 212 min | 147 min | 359 min |
En la tabla 1 se muestra los resultados obtenidos para cada uno de los procesos identificados anteriormente. Para la recepción de pedidos se obtuvo 159 minutos de tiempo que agrega valor y 173 minutos que no es significativo, en el caso del proceso de almacenamiento se tiene que 180 minutos no agregan valor a esté y 279 minutos si agregan valor y por ultimo el proceso de armado de pedido se tiene que 212 minutos agregan valor y 147 minutos no generan importancia para esté.
Los tiempos altos en los procesos son producidos por una inexistente zona destinada para la recepción de productos, la inadecuada organización de los espacios en el almacén, tiempo excesivo para el armado de pedido, debido a que no se conoce el lugar exacto para encontrar los productos dentro del almacén. Además, se tienen zonas obstruidas con mercaderías que ocasionan un inadecuado desplazamiento. Es importante considerar que los registros de la empresa no son mecanizados y no se conoce el stock real de cada producto. Para el estudio se consideró analizar los indicadores principales que debería tener la empresa, en primer lugar, se midió el nivel de servicio y se obtuvo un 78%. Luego se revisó el nivel de exactitud de inventario (ERI), se obtuvo que solo el 31,50% de éstos estaba documentado. En cuanto el nivel de rotación de los productos se tuvo un 31% y la utilización del espacio del almacén solo era del 73%. En la figura 1 se detalla las evidencias según el nivel de servicio, calculando la brecha técnica de la empresa de acuerdo con el indicador seleccionado. También del impacto económico se tiene que las pérdidas equivalen un 29% de los ingresos. A demás se identificaron las diferentes causas raíz de las causas para luego presentar sus posibles soluciones.
Impacto Económico
El impacto económico que genera el problema en la empresa representa montos altamente relevantes que perjudican los ingresos de ésta. Por lo que, se hará un análisis cuantitativo de las cantidades monetarias perdidas del segundo semestre del año 2019. Por no cumplir correctamente las órdenes de compra se pierde aproximadamente USD 23,290.75, en productos obsoletos se tiene un valor de USD 26,183,17, el costo de almacenamiento es de USD 8,342.85 y el de mantenimiento USD 5,580.00; por último, el costo de sobrestock es de USD 38,942.55. En conclusión, al analizar el impacto económico la empresa está perdiendo alrededor de USD 102,339.29 siendo este el 29,59% del total de los ingresos.
3. Estado del Arte
Las 5S es un método de cinco pasos diseñado en Japón para asegurar la limpieza y el orden en el lugar de trabajo. Se llama así porque cada uno de los cinco pasos corresponde a una palabra en japonés que comienza con las letras: seiri, seiton, seiso, seiketsu, shitsuke (Vreca & Edgar, 2009). Se aplicó la herramienta 5S en una pyme, primero clasificaron las herramientas y productos, luego establecieron un lugar adecuado para almacenar herramientas, priorizando los de mayor uso y elaboraron métodos de trabajo para la limpieza. El resultado principal fue la reducción de los tiempos de búsqueda de materiales a 10 o 15 minutos como máximo (Stahlhofer et al., 2016).
Una empresa que comercializa bienes de consumo, aplicó la herramienta 5S y VPM para estabilizar las operaciones del almacén. Se ordenó y desechó lo que no es útil, se utilizó la gestión visual para evaluar los KPI y se estandarizaron los procesos del almacén, el resultado fue el aumento del 26% en la productividad de picking y una operatividad del almacén más equilibrada (Oey & Nofrimurti, 2018). Otro caso era la deficiente organización de la información del área logística porque no estaba integrada y afectaba al proceso de mejora continua. Se inició con la recolección de información para ingresarla a la nueva base de datos, posterior a ello se asignó un planificador para la revisión y se establecieron plazos para la actualización. Con la implementación obtuvieron ahorros estimados de 6245 euros y redujo tiempos de procesamiento en un 66%, el tiempo del proceso de envio se redujo en un 58% (Monteiro et al., 2017).
En una empresa automotriz, primero agruparon sus productos de acuerdo con el SKU en función al criterio de volumen de ventas anual de cada artículo y la tasa de uso. Para separar el inventario en las categorías A, B y C, se tiene que crear una matriz ordenada que presente todos los SKU en orden descendente del valor en dólares de las ventas anuales. El valor acumulado de las ventas, generalmente, resulta en una curva donde típicamente el 20% superior de los artículos representa aproximadamente el 75% del volumen anual de ventas en dólares, el siguiente 30% de los artículos representa el próximo 15% de las ventas, y el 50% restante representa el último 10% del volumen en dólares. (Arikan & Citak, 2017)
El SLP es una herramienta utilizada para el desarrollo del diseño de planta y mejorar el flujo de los materiales. En un caso de estudio se pudo disminuir la distancia total recorrida de la planta, se implementó las 5S y se eliminaron actividades que no agregan valor, además disminuyeron los tiempos de entrega a 13 minutos y se redujeron sus costos de almacenamiento en un 25% (Ali Naqvi et al., 2016). Un caso de estudio implementó la herramienta 5S y la sistematización de sus productos utilizando el programa Microsoft Excel para tener un correcto registro. Primero se clasificaron los productos en una base de datos, para diferenciar lo útil con lo innecesario y procedieron a ordenarlos asignándoles un código de acuerdo con el nombre de cada artículo para conocer la cantidad de cada uno y el lugar de ubicación. Luego se asignaron los procedimientos con las normas y reglas de cada actividad de los procesos de la empresa para conseguir una estandarización. Entre sus principales resultados se redujo el tiempo de búsqueda de sus productos a 6 minutos (Verma & Jha, 2019).
4. Propuesta Innovadora
4.1. Fundamento de la propuesta
La propuesta de valor se generó a través de una revisión exhaustiva de la literatura, por ello en la tabla 1, se muestran los autores que tuvieron mayor grado de contribución a los problemas y herramientas de solución identificados en la presente investigación:
Tabla 2 Contribución de autores a la propuesta de valor
5S | Sistematización | ABC | Estandarización | SLP | |
Yadav V. et al. (2019) | P | ||||
Oey & Nofrimurti (2018) | P | ||||
Ye, Xiaolong & Yugang (2018) | P | ||||
Khan et. al (2019) | P | ||||
Zakirah et. al (2018) | P | P |
4.1. Modelo Propuesto
El modelo propuesto tiene como objetivo agilizar la gestión de almacenes, con ello se optimizará los tiempos involucrados en los procesos de recepción, armado y almacenamiento de productos para evitar la disminución del nivel de servicio. Es importante considerar que las empresas del sector comercial deben contar con un nivel de stock de productos para satisfacer la demanda en el tiempo solicitado, así evitar el incumplimiento de la entrega total de los pedidos. Por ello, se aplicará como principal herramienta las 5S y contará con herramientas de ingeniería para dar soporte en la aplicación de cada etapa del modelo, éste consta de 3 etapas de implementación, este se basa en un ciclo de mejora continua con la utilización de las 5S en conjunto con la clasificación ABC, sistematización del inventario, system layout planning (SLP) y la estandarización del trabajo para eliminar las actividades que no generan valor en el proceso, además se diagramará los flujos correspondientes a cada proceso y se tendrá una política para la gestión de los almacenes. La siguiente figura se ha denominado el “HS Warehouse Managment Deming Model”, el cual muestra el proceso de ejecución del modelo propuesto, para las entradas al proceso primero se hace la revisión de la literatura y se identifica el nivel de servicio actual, luego se desarrollará cada una de las etapas descritas en la imagen y se obtendrá como resultado un alto nivel de salida, procesos estandarizados, reducción de tiempos en los procesos y nuevos indicadores.
4.2. Componentes del Modelo
Etapa 1: Clasificar productos en almacén + ABC
Inicia con la inspección del almacén, donde se identificará las existencias de la empresa y se clasificarán según el estado de cada producto. Se utilizará tarjetas rojas para colocarlas a cada producto que se encuentre obsoleto o deteriorado y posteriormente se ubicarán en la “zona de obsoletos”. En esta zona, el dueño de la empresa determinará qué productos serán desechados definitivamente y cuáles serán denominados “chatarra”. Luego, se procede a utilizar la herramienta ABC multicriterio, para conocer la cantidad de productos con los que disponen. El objetivo de aplicar esta herramienta es conocer los productos de mayor rotación, con ello se tiene un registro preliminar y se procede a clasificarlos para los diferentes almacenes.
Etapa 2: Orden y limpieza en almacén + SLP +Kardex
En esta etapa, se registra los productos encontrados en el almacén en un Kardex diseñado para la empresa, se usará el sistema PEPS (primeras entradas, primeras salidas) y se ordenará por marca y nivel de rotación del producto. Con el SLP, se reorganizará el espacio de las áreas del almacén y se distribuirá eficientemente cada anaquel de los almacenes para optimizar la utilización del espacio. Luego, se procede a ordenar los productos dentro de cada almacén considerando los resultados obtenidos de las diferentes herramientas utilizadas hasta esta etapa del modelo. Finalmente se implementa una cultura de limpieza en el almacén, la cual incluye un flujograma de las actividades de este proceso, además se utilizará un checklist para especificar los implementos de limpieza, el estado de cada herramienta y la periodicidad de la limpieza.
Etapa 3: Estandarización de trabajo y Disciplina
Empieza con el mejoramiento de los flujogramas de los procesos de recepción, almacenamiento y picking, eliminando las actividades que no generan valor para su ejecución. Además, se establece el nuevo flujograma de limpieza con la finalidad de estandarizar el trabajo y controlar las actividades a realizarse en el almacén. Adicional a ello, se crean políticas para la gestión de almacenes y la de SST, parte de la estandarización es desarrollar la correcta descripción de los puestos de trabajo del personal de la empresa. Se incorporan fichas de control y formatos para evidenciar los sucesos diarios del almacén. Se implementa un tablero de control visual, para que los trabajadores puedan observar la información relevante, por ejemplo: el estado de los almacenes con respecto al orden y la limpieza, el nombre del encargado de la limpieza por cada semana, las funciones principales de cada uno de los trabajadores del almacén, además se tiene un espacio destinado para colocar anuncios sobre reuniones o capacitaciones y finalmente el conteo de los pedidos que ingresan y cuántos son entregados completos.
Luego se procede a realizar las capacitaciones a los colaboradores de la empresa para que conozcan el nuevo funcionamiento del área y los cambios realizados, para aumentar la productividad de la empresa y disminuir los errores comunes. Por último, se establece que cada tres meses se realicen auditorias al almacén, serán realizadas por el dueño y se apoyará de una ficha, la cual se llenará según el estado del almacén al momento de la inspección. Es importante controlar el correcto desarrollo de las 5S e identificar las nuevas áreas de mejora para dar soluciones rápidas y hacer cada vez más eficiente el proceso.
5. Validación
5.1 Validación de implementación
La validación se realizó mediante la ejecución de un programa piloto de implementación para cada una de las etapas del modelo, por ello se estableció el tiempo óptimo para demostrar el nivel de confiabilidad de adaptación del modelo, por lo que la duración aproximada es de un mes. A continuación, se evidencia cada una de las etapas propuestas.
Etapa 1: Clasificar productos en almacén + ABC
De acuerdo con el modelo propuesto, se inició con la clasificación de los productos utilizando tarjetas rojas para identificar los productos obsoletos o en mal estado, la cual se muestra en la figura 3
Luego se registran los productos para proceder con su clasificación, se consideró las unidades de los productos existentes y el valor monetario, con ello se constató que existen más de 200 productos en el almacén. Con la herramienta ABC se determinó los productos que tienen mayor rotación obteniendo 71 en la categoría A, 65 en la categoría B y 64 en la categoría C, los resultados descritos se muestran en la figura 4. La utilización del ABC servirá para realizar la distribución de los almacenes en la siguiente etapa.
Etapa 2: Orden y limpieza en almacén + SLP +Kardex
En esta etapa, se utilizó el registro obtenido de la etapa anterior para complementar la información con la herramienta SPL, la cual ayudo a distribuir los anaqueles del almacén según la rotación de los productos. La figura 5 se tomó como referencia para la distribución de los productos en los anaqueles del almacén.
Luego de distribuir la ubicación pertinente para cada producto se ordenó en el anaquel asignado y procedió a enumerar los anaqueles con su respectivo código QR para identificar rápidamente los productos correspondientes a cada espacio. En la figura 6 se muestra el antes y después de los anaqueles.
Para fomentar una cultura de limpieza en los almacenes, se elaboró un flujograma donde se describe las principales actividades a realizar, esto se complementa con la creación de la hoja de control de los materiales a utilizar y el registro de inspección de limpieza. La siguiente figura muestra el esquema que deben seguir para llevar el control de la inspección.
Con la sistematización de inventario, se logró generar un Kardex en el programa Excel en cual se utilizó el método PEPS para el registro y salida de productos del inventario, conociendo el costo de cada uno de ellos, para que las compras futuras se generen cuando no se cuente con el stock necesario de cada producto. La incorporación de la codificación QR a los productos ayudó para conocer el stock y la ubicación destinada en el anaquel.
Etapa 3: Estandarización de trabajo y disciplina
Para finalizar se procede con la estandarización de los procesos, con el objetivo de que los operarios entiendan de forma funcional las actividades que deben cumplir por cada uno de los procesos que realizan dentro del almacén. Además, para mejorar la orientación de funciones de los operarios se realizó el MOF de cada puesto de trabajo. Luego se capacitó a los trabajadores para que conozcan el nuevo funcionamiento de sus áreas de trabajo, enfatizando en el rediseño de los procesos y el uso del tablero de control visual. Con ello, el encargado del almacén podrá realizar auditorías periódicas para verificar el cumplimiento de las herramientas implementadas.
La implementación de la 5S en tres etapas distintas y con el apoyo de herramientas de fácil adaptabilidad permitió que se obtengan mejoras en el tiempo de almacenaje, el cual se redujo en un 57%, debido a que se eliminaron actividades que no generaban valor y se tiene un mayor control en el orden y limpieza de los almacenes. En cuanto al proceso de picking disminuyó el tiempo en un 55% y por último en el proceso de recepción de pedidos se redujo aproximadamente en 63%. En la siguiente tabla se muestra las mejoras obtenidas con respecto a los tiempos de los procesos.
Tabla 3 Definición de algunos estilos
Indicador (Tiempos) | Valor Inicial | Valor Esperado | Resultado Final |
Proceso de almacenamiento | 459 min | 198 min | 210 min |
Proceso de picking | 359 min | 160 min | 158 min |
Proceso de recepción | 332 min | 124 min | 150 min |
Además, se evaluaron diferentes indicadores para verificar la efectividad de la implementación. El desarrollo del proyecto tiene como objetivo principal mejorar la gestión de almacenes porque dificulta la atención completa de todos los pedidos. Con ello se aumenta el nivel de servicio en un 13,8%. En la tabla 3 se puede verificar el aumento del indicador con respecto al nivel inicial identificado.
Tabla 4 Nivel de servicio anterior vs optimizado
Nivel de Servicio (Anterior) | Nivel de Servicio (Optimizado) |
78% | 91,8% |
En cuanto a la implementación de las herramientas de soporte, se tuvo un impacto en la organización y se determinaron indicadores para demostrar la mejora de la empresa, lo que permitió obtener mayor participación y posicionamiento en el mercado ferretero cumpliendo las expectativas del cliente. La tabla 4 sintetiza los resultados correspondientes a cada indicador utilizado en el desarrollo de la implementación de la propuesta de mejora, teniendo los siguientes resultados; para el nivel de 5s se obtuvo un 4.22, en el caso del nivel de rotación de los productos se logro un 86.5%, para la exactitud del registro de inventario se logró en un 88% y para la utilización del espacio se distribuyó cerca del 86,3% del espacio total de los almacenes.
5.2 Validación por Arena Simulator
Se simulará el proceso de recepción y almacenamiento de productos en almacén y luego el proceso de picking, para ambos se usará el programa Arena. Para el primer proceso se considera los almacenes de la empresa, se inicia cuando un producto solicitado llega a almacén; el almacenero se encarga de colocar los productos en la zona de recepción para realizar una revisión de lo que figura en la factura con los productos recepcionados. De encontrar algún producto faltante, se comunican con el proveedor y se procede a devolver la mercadería. Luego se identifica en que almacén debe ser colocado la mercadería entrante, la cual es distribuida entre el almacén del piso 1, 4 y sótano para ubicarlos en el anaquel correspondiente. En el proceso de picking, se comienza con la llegada de una orden de pedido solicitada por un cliente, la cual es enviada al almacén para poder armarlo, por lo que se procede a seleccionar los productos detallados en la orden y llevarlos a la “zona de armado de pedido”, aquí se verifica que esté completo y se deja en la “zona de despacho de pedido”. En ambas simulaciones se tendrá en cuenta que la empresa trabaja de lunes a sábado en un horario de 9 am a 6 pm, con 1 hora de refrigerio. Y se contará con una duración de repeticiones de 120 días.
Primero se consideran un aproximado de 30 muestras válidas por cada actividad dentro de cada proceso, con ello identificar el tipo de distribución adecuada para la simulación y su mejora. Se obtienen las siguientes tablas (5 y 6) con las distribuciones ajustadas según la aplicación de la fórmula de muestra.
Tabla 6 Distribuciones de las variables del Proceso de Recepción y almacenamiento
Variable | Descripción | Valor | Distribución | Expresión |
T TELL | Tiempo entre llegadas de productos | Min. | Uniforme | UNIF (1.55e+003, 2.87e+003) |
TSR | Tiempo de recepción de productos | Min. | Triangular | TRIA (20, 22.9, 27.7) |
TSRP | Tiempo de revisión de factura de productos | Min. | Exponencial | 17 + EXPO (22.8) |
TSA1 | Tiempo de ubicar un producto en sótano | Min. | Uniforme | UNIF (61, 100) |
TSA2 | Tiempo de ubicar un producto en Piso 1 | Min. | Triangular | TRIA (7, 23.9, 24) |
TSA3 | Tiempo de ubicar un producto en Piso 4 | Min. | Triangular | TRIA (27, 35.6, 40) |
Tabla 7 Distribuciones de las Variables del Proceso de Picking
Variable | Descripción | Valor | Distribución | Expresión |
TELL1 TELL | Tiempo entre llegadas de pedidos al almacén | Min. | Uniforme | UNIF (13, 35) |
TSR | Tiempo de Revisión de disponibilidad de productos | Min. | Uniforme | UNIF (8, 21) |
TSA1 | Tiempo de ubicar un producto en almacén del sótano | Min. | Triangular | TRIA (10, 13, 40) |
TSA2 | Tiempo de ubicar un producto en almacén del piso 1 | Min. | Uniforme | UNIF (12, 21) |
TSA3 | Tiempo de ubicar un producto en almacén del piso 4 | Min. | Uniforme | UNIF (12, 32) |
TSAP | Tiempo de armado de pedido | Min. | Triangular | TRIA (12, 14, 15.7) |
Luego se grafica un flujo de los procesos a mejorar en orden y cantidad de actividades involucradas teniendo en cuenta las colas que se generan, en la figura 10 se muestran todos procesos involucrados en el sistema. La finalidad es simular la situación real e identificar las actividades principales que se deben de cumplir y de esa forma validar el escenario antes y después de la mejora. En la figura 10 y 11 se muestra la representación gráfica de los tres procesos a mejorar.
El software Arena simuló los procesos de Recepción, Almacenamiento y Armado, considerando los inputs analizados, las variables y las actividades del sistema según la distribución asignada.
Proceso de recepción y almacenamiento de productos
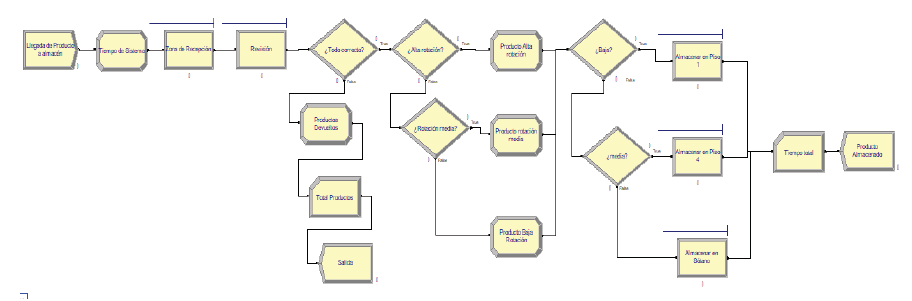
Figura 12 Modelo en software Arena de los procesos de recepción y almacenamiento de productos en almacén - Situación de Mejora
Proceso de picking
Después de realizar el flujo en Arena, se debe calcular el número óptimo de corridas para que los valores obtenidos sean significativos para la simulación. Se procedió al ajuste del valor N y se vuelve a correr el modelo en Arena tomando en cuenta la situación actual, la mejora y los tiempos obtenidos del sistema. Donde el número óptimo de corridas para el proceso de Recepción y almacenamiento es de 300 y para el proceso de Picking es de 62.
Para analizar la situación de mejora obtenida con el simulador, se tomó en cuenta los resultados de la implementación de la propuesta de mejora, los cuales reflejan que los tiempos del proceso de recepción y almacenaje se redujeran aproximadamente más de un 50%, debido a la integración de las herramientas ABC y SLP permitieron que las operaciones del almacén sea más eficiente, además el tiempo del proceso de picking se redujo en 55% en comparación a la situación inicial, esto se debe a que la sistematización del inventario ayuda a dar respuesta inmediata a los requerimientos de los clientes. En la siguiente tabla se detallan los resultados obtenidos con el software y se comparan con los datos iniciales y los esperados.
6. Discusión
6.1 Análisis de Resultados
Al realizar el análisis se plantearon 3 escenarios mostrados en la tabla 5 correspondientes a 3 meses de implementación del modelo propuesto, en el siguiente cuadro se registra el progreso positivo de cada indicador propuesto para mejorar la gestión de almacenes. Se evidencia la implementación de diversas herramientas para estandarizar los procesos; con ello los tiempos de los procesos de recepción, almacenamiento y picking se redujeron más del 50% en comparación de la situación inicial. Con la aplicación de las 5S se logró fomentar una cultura de orden y limpieza en el caso de estudio, además la participación de los trabajadores contribuyó en el éxito de la implementación, por ello el nivel de la auditoria de las 5S aumento en un 52,4%.
6.2 Trabajos Futuros
Las pymes pertenecientes al sector comercial empiezan sus actividades con una deficiente gestión empresarial, por lo que se encuentran en constantes cambios para mejorar el inadecuado control de inventarios, el orden en sus almacenes y todo es causado porque no se determinan sus procesos correctamente y no involucran activamente la tecnología en sus negocios (Kianto et al., 2018). Es importante conocer todo el inventario que tienen en sus almacenes por ello, se puede adquirir un sistema qué relacione los inventarios con el sistema de facturación de la empresa para realizar los descuentos automáticos de mercaderías. Además, se debería añadir un diseño en la red de distribución de la empresa para involucrar toda la cadena de suministro, con esta nueva red la empresa tendría capacidad de respuesta ante la demanda.
7. Conclusiones
Con la implementación de la propuesta de mejora se comprueba su viabilidad, en la gestión de almacenes del caso de estudio. Debido a que se logró aumentar en un 13% el nivel de servicio en estos 3 meses de prueba a comparación de la situación inicial. Al pasar los meses la adaptabilidad del trabajo se continuó con los procesos estandarizados para sobrepasar el 95% del nivel de servicio esperado.
El modelo propuesto permitió crear en la empresa un ciclo de mejora, aumentando el nivel de 5S en más del 50% del nivel inicial. La implementación de la herramienta estandarización de trabajo permitió que el tiempo del proceso de picking se reduzca en 55%, el proceso de almacenamiento disminuyó en 57% y el proceso de recepción tuvo una reducción del 63%. Con el ámbito del orden y limpieza se pudo rediseñar el System Layout Planning optimizando el espacio en un 86,3%,
Realizando una simulación con el programa Arena se relacionó los procesos de recepción, almacenamiento y picking de la empresa, para tener la certeza de que efectivamente el nuevo flujo de los procesos es más eficiente y productivo que la situación actual. Asimismo, se pudo comprobar que la implementación del proyecto y la simulación dieron resultados positivos debido a que, los tiempos de los procesos críticos se redujeron en más del 50%.