Servicios Personalizados
Revista
Articulo
Indicadores
-
Citado por SciELO
-
Accesos
Links relacionados
-
Similares en SciELO
Compartir
Portugaliae Electrochimica Acta
versión impresa ISSN 0872-1904
Port. Electrochim. Acta vol.36 no.2 Coimbra mar. 2018
https://doi.org/10.4152/pea.201802133
Electrochemical and Metallurgical Behavior of Lead-Aluminum Casting Alloys as Grids for Lead-Acid Batteries
Salma Khatbi* , Youssef Gouale , Said Mansour , Abdeslam Lamiri and Mohamed Essahli
Univ. Hassan 1, Laboratory of Applied Chemistry and Environment, Faculty of Science and Technology, P.O. Box 5777, Settat, Morocco
Abstract
In order to evaluate the influence of aluminum on the corrosion resistance of lead anodes in 4 M H2SO4, as well as on the microcrystalline morphology of lead, different electrochemical and metallurgical studies were made such as potentiodynamic polarization, electrochemical impedance spectroscopy, hardness evolution, X-ray fluorescence spectroscopy and optical microscopy. The obtained results have shown that the addition of aluminum up to 1.5% in weight leads to a significant decrease of the corrosion and passivation rates (Icorr and Ipass) and it reduces the famous sulfation phenomena by facilitating the transformation of PbSO4 and PbO to PbO2. It also makes the micro-structure of Pb much stronger, which makes the Pb anodes more resistant to mechanical shocks within the battery. All of these improvements led to increase the lifetime of the conventional lead-acid battery up to 51.15%. Therefore, the new improved battery is more resistant, durable and more environment friendly.
Keywords: battery, corrosion, lead-aluminum alloy, electrochemistry, metallurgy.
Introduction
The lead-acid battery is considered as one of the most successful electrochemical inventions up to today; it is very difficult to find a battery that performs as well as the lead-acid battery and that can replace it in the field of energy storage. The lead plates which constitute this battery are very malleable, fragile and cannot resist, as it should, facing the corrosivity of the concentrated electrolyte which is made of 4 M H2SO4. Also, the battery suffers from the sulfation phenomena, which is characterized by the formation of a non-porous and impermeable layer of PbSO4 on the surface of the metal, thus preventing any possible reaction between lead and H2SO4 [1-4]. For all these reasons, it is imperative to find alternative solutions to reinforce these plates and make them more resistant to mechanical shocks as well as to electrochemical corrosion. Many researches have been made recently to find the best alloys capable of replacing the pure lead plates. Wislei R. Osorio et al. [5] have found that the Pb-1%Sn and Pb-2.5% Sn alloys immersed in 0.5 M H2SO4 reduce considerably the corrosion of lead when these alloys have coarse grains in comparison with other alloys that have finer grains. Also, this type of alloys allow to make much lighter batteries. M. I. Cekerevac et al. [6] and R. David Prengaman [7] have studied the influence of the addition of tin and silver on the corrosion rate of Pb by modifying its microstructure. They have found that, indeed, Pb-Ca-Sn-Ag alloys are more resistant to corrosion in comparison with pure Pb, and that by increasing the concentration of the added Sn and Ag, the microstructure of the primary alloy Pb-Ca is modified in a positive way. L. Albert et al. [8] have found that when Sn is added up to 1.2% in weight in 4.8 M H2SO4, the passivation rate of the Pb-Ca- Sn alloys decreases under conditions that simulate the deep discharge of the battery, by increasing the conductivity of the PbO layer that usually is formed on the surface of the metal. Very little researches have been done to evaluate the effect of the addition of aluminum on the corrosion of lead in batteries, and for this reason we have chosen aluminum as our element of addition. Among these researches, we have found those of B. Hong et al. [9] who have prepared a lightweight grid of Pb plated (Al / Pb) grid immersed in 5 M H2SO4 and made by molten salt electroless plating which had a life cycle of 475 cycles, and this complies with the requirements of the lead-acid battery. Their grid was 55.4% lighter than the conventional grid of pure lead and with a mass specific capacity of 17.8% higher. L.A. Yolshina et al. [10] have found that the addition of aluminum to the lead grids immersed in 4.75 M H2SO4 led to significantly reduce the weight of the battery, and increased its specific energy from 30 to 35%. Prior to this work, we studied the effect of the addition of phosphoric acid and its salt K2HPO4 into the corrosive electrolyte of 4 M H2SO4 on the corrosion resistance of lead. The obtained results were very promising, since the corrosion and passivation rates were significantly reduced [11]. Now, we're opting for a different approach; we have chosen to modify the composition of the negative plate of the battery (Pb) by combining it with other metals such as aluminum, which is known by its lightness and its high electrical conductivity. It will allow us to evaluate its effect on the resistance of lead to corrosion and mechanical shocks. To do this, we used different techniques such as: the potentiodynamic polarization, electrochemical impedance spectroscopy, optical microscopy and the X-ray fluorescence spectrometry.
Experimental procedures
Preparation of the alloys
The prepared alloys are made of pure metals: Pb (99.98%) and Al (99.85%); they are based on Pb with the addition of Al in different contents: Pb-0.5% Al, Pb- 0.8% Al, Pb-1% Al and Pb-1.5% Al.
To prepare these alloys, we have taken the items in the appropriate proportions, we introduced them in a silica glass tube of 1 cm in diameter, sealed under high vacuum in order to prevent oxidation of lead. The assembly (alloy + tube) is brought to a temperature of approximately 700 °C. After fusion, the assembly is water quenched at room temperature.
All the prepared samples are aged at room temperature to follow the evolution of hardness as a function of time.
The prepared alloys are directly studied or preserved in liquid nitrogen. In order to obtain reliable and reproducible results, the working electrode undergoes, before each test, polishing with different abrasive papers 400, 600 and 1200. Then, they are rinsed with distilled water and dried.
As shown in the Fig. 1 [12], the binary system Pb-Al is characterized by 3 phases: liquid phase (L), solid solution of Pb and solid solution of Al.
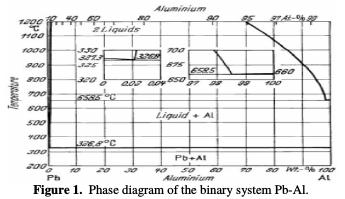
An immiscible liquid occurs below a critical threshold. The solubility of the solid lead in aluminum and that of the solid aluminum in the lead are extremely low. The critical composition is of 55.2% aluminum at 1566 °C.
Before and after elaborating the alloys, we have analyzed the chemical composition of, respectively, pure lead and the Pb-Al alloys to know the exact quantities of each element including impurities. To do this, we used the portable X-ray fluorescence spectrometer The Thermo Scientific Niton XL5. It's the newest and the faster device to give accurate results and exact composition of any metallic surface. Each chemical composition present in Table 1 is the result of punctual analysis.
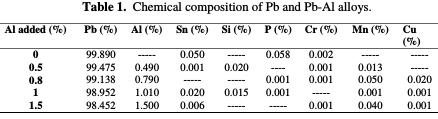
Hardness
The hardness tests were carried out by the Vickers method using a Testwell durometer under a load of 2 kgf. Each measurement corresponds to the average of a maximum of four imprints located on a planar section corresponding to a diameter plan or perpendicular to the axis of the cylindrical sample. The sections are obtained by sawing, mechanical abrasion and then chemical polishing. We should recall that the empirical relationship HV= 0.3 R (Mpa) can be used to assess the maximum load (R) of these alloys.
Optical microscopy
The physical properties of the quenched solid solutions of lead alloys evolve at room temperature. The hardening mechanisms are continuous/discontinuous transformations. In fact, this temperature corresponds to 0.5 Tf (alloy's melting temperature). We know that from 0.4 to 0.5 Tf, the alloy elements can diffuse. In case where the kinetics of the discontinuous transformation are rapid at room temperature, we use the original technique developed by Hilger [13] in order to be able to observe the structure before any transformation. For our alloys, the sample is polished, soaked in a chemical solution consisting of one part of 30% H2O2 and three parts of glacial acetic acid. The solution temperature is -50 °C. The duration of the immersing process varies between 20 seconds and 2 minutes depending on the state of the sample. The chemical polishing is followed by repeated chemical attacks/etching using a mixture of 100 mL distilled water, 25 g citric acid and 10 g ammonium molybdate.
Electrochemical techniques
Electrochemical measurements have been carried out by a cell of 3 electrodes consisting of a saturated calomel electrode (reference), a platinum wire electrode (auxiliary) and a sample of the lead as a working electrode. Before each test, the sample is left under an open circuit for 5 minutes to achieve a stable open circuit potential. The potentiodynamic polarization was carried out by sweeping the potential with a rate of 2 mV/s ranging from - 1500 to 2500 mV. We obtained various kinetic parameters as the corrosion current density (Icorr), the corrosion potential (Ecorr) and the passivation current density (Ipass). The corrosion current density has been measured by extrapolation of Tafel straight lines. The measurements of the electrochemical impedance spectroscopy have been carried out using a margin of frequency ranging from 100 kHz to 10 Hz at the corrosion potential. For the analysis, we used the device 10 VoltaLab model (PGZ100) connected to an HP computer. The acquisition and processing of data were done using VoltaMaster 4 and OriginLab software.
Results and discussion
Fig. 2 shows the hardness evolution of Pb-Al cast-alloys at room temperature (25 °C). It is noted that the initial values of hardness are approximately 11.02 HV, 11.30 HV, 11.37 HV and 11.49 HV.
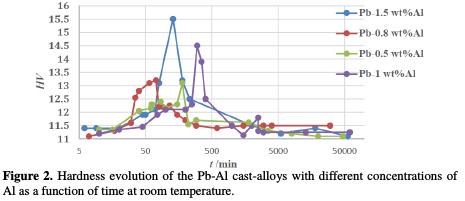
Therefore, in combining lead to aluminum, the initial value of the alloy's hardness is more than two times higher than that of pure lead (5 HV), meaning that lead is harder when added to aluminum. This increase in hardness leads to a great reduction the inter-granular corrosion as well as to increase the corrosion resistance. The alloys will have better mechanical properties and it will definitely be more resistant to mechanical shocks experienced within the battery. The hardness is higher, due to transformations that take place during the solidification of the alloy. At 25 °C, the maximum hardness achieved is approximately 13.15 HV for Pb-0.5%Al after 2 h, 13.35 HV for Pb-0.8%Al after 30 min, 14.5 HV for Pb-1%Al after 2 h 20 min and 15.5 HV for Pb-1.5%Al after 1 h 55 min. After that, we note a slight decrease of the hardness values. After 3 days, the hardness becomes stable at 11.45 HV for all alloys.
Optical microscopy
Fig. 3 and Fig. 4 represent the evolution of the structure of quenched cast Pb-Al alloy at 25 °C.
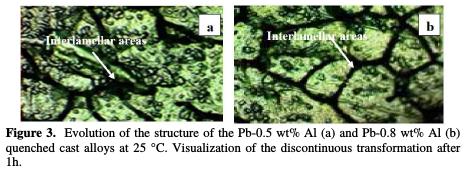
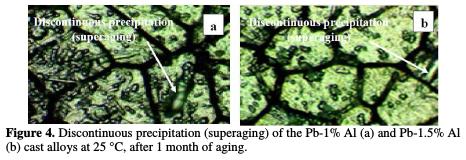
It's a visualization of the discontinuous transformation after 1h for Pb-0.5% Al and Pb-0.8% Al and after 1 month for Pb-1% Al and Pb-1.5% Al.
Microprobe analysis carried out in the regions concerned by the aging, shows that the precipitates are fully made of aluminum. However, the analysis of the interlamellar areas shows that the contents of aluminum in these areas is very low and that it remains the same throughout the matrix.
Potentiodynamic polarization
Effect of Al contents on the corrosion of Pb To study the electrochemical effect of aluminum (Al) on the corrosion of lead (Pb) in 4 M H2SO4, we have used two techniques of analysis: potentiodynamic polarization and electrochemical impedance spectroscopy. We have prepared 4 electrodes (Pb-0.5% Al, Pb-0.8% Al, Pb-1% Al and Pb-1.5% Al) using the procedure above described. To be able to study the effect of aluminum, we had to compare polarization and impedance curves obtained by immersion of the electrodes Pb-Al with those obtained by immersion of pure lead in 4 M H2SO4.
Fig. 5 shows the polarization curves of the pure lead and those of Pb-Al alloys at different contents of Al in 4 M H2SO4 at 25 °C.
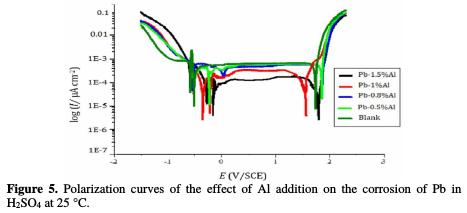
The intersection points of the Tafel lines give the corrosion current density Icorr. The polarization parameters are present in the Table 2.
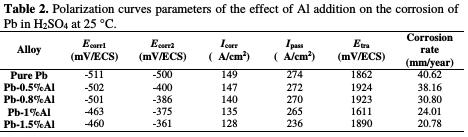
In the cathodic part of the polarization curves, we note an intense decrease of the current corresponding to the hydrogen evolution reactions. At this range of potential (-1.500 to 0.512 V), lead is in the activation phase. The corrosion of Pb and of the Pb-Al alloys is characterized by the appearance of two peaks corresponding to two corrosion potentials (Ecorr1 and Ecorr2). The first corrosion potential Ecorr1 corresponds to the reaction of Pb with H2SO4 and the formation of PbSO4 according to the following reaction:

The second corrosion potential Ecorr2 indicates the potential at which Pb oxidizes leading to the appearance of PbO; this oxidation is resulting from the reaction between Pb and H2O:

These two compounds (PbO and PbSO4) precipitate on the surface of the lead preventing H2SO4 to infiltrate, thereby inhibiting any reaction between the lead and the electrolyte. This is the phase of the passivation process, represented by a bearing of corrosion current density Ipass, which remains virtually constant for a period of time. This phase ends with the transpassivation. At this stage, the products of the corrosion (PbO and PbSO4) are transformed into PbO2 by reaction with water, according to the following reactions:
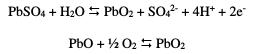
This transformation is indicated by a peak of polarization characterized by a potential of transpassivation (Etra) followed by an increasing current corresponding to the evolution of oxygen.
By observing the polarization curves in the Fig. 5 and the data in the Table 2, we can note that the more the content of added Al increases, the more the corrosion potentials Ecorr1 and Ecorr2 decrease (from -511 to -400 mV for Ecorr1 and from - 500 to -361 mV for Ecorr2) meaning that there is an important protection of lead against corrosion. Also, the addition of Al reduces strongly the corrosion current density Icorr from 149 to 128 μA/cm2 and the passivation current density Ipass from 274 to 236 μA/cm2 indicating that the addition of aluminum led to an improvement of the corrosion resistance of Pb. The quantity of the impermeable elements (PbO and PbSO4) passivating lead also decreases and consequently, the lifetime of the battery increases, which can be concluded by the decrease in the corrosion rate from 40.62 mm/year for pure lead to only 20.78 mm/year after addition of 1.5% in weight of Al, which means that the lifetime of the battery will be 48.84% times greater after the addition of aluminum up to only 1.5% in weight.
Fig. 6 illustrates the increase of the inhibition efficiency (%IE) as a function of the content of aluminum. IE was calculated using the equation:

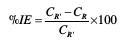
where CR' is the corrosion rate of pure Pb and CR is the corrosion rate of the alloy.
The bearing of passivation and therefore the potential for transpassivation (Etra) decreases with the increase of the Al concentration, meaning that aluminum facilitates the transformation of PbSO4 and PbO into PbO2. This decrease is followed by the reactions of the oxygen evolution. The parts of the polarization curves indicating these reactions do not change, meaning that aluminum has no significant effect on the oxygen evolution.
Effect of temperature on pure Pb and Pb-Al alloys
According to the obtained results, presented in Fig. 7 and the Table 3, it can be clearly noticed that the increase in the temperature has a negative effect on the corrosion of pure lead.
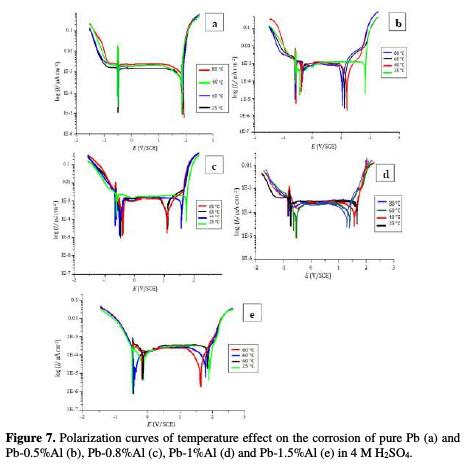
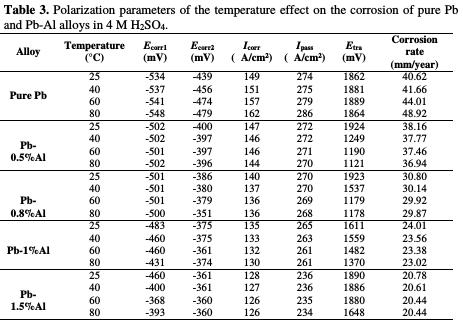
With the increase of the temperature from 25 to 80 °C, the corrosion potentials Ecorr1 and Ecorr2 increase (meaning that the protection of the metal decreases), the corrosion and passivation current densities (Icorr and Ipass) increase also, as well as the corrosion rate, which goes from 40.62 to 48.92 mm/year, indicating that when the temperature within the battery increases, the battery's lifetime decreases by 16.96%.
After the addition of aluminum, we clearly note that the increase in the temperature has slighter effect in comparison to the one in the case of pure lead. In fact, the values of the corrosion potentials Ecorr1 and Ecorr2 increase slightly, which means that the addition of Al minimizes the effect of temperature on the corrosion of Pb. Therefore, temperature reduces the negative effect of the corrosion obtained from the addition of aluminum. Meanwhile, the transpassivation potential Etra decreases in the case of each alloy. The potentiodynamic experiments show that addition of Al to Pb significantly facilitates the formation of PbO2 at high temperatures and hence accelerates the corrosion process but not as much as in the case of pure Pb.
Electrochemical impedance spectroscopy
Effect of Al concentration on the corrosion of pure Pb The electrode of pure lead and that of lead-aluminum were polarized in 4 M H2SO4. The potential scan began at -1500 mV at a rate of 2 mV/s. A steady state- passive current was obtained and then the electrochemical impedance spectroscopy measurements were carried out.
Fig. 8 shows the Nyquist representations of pure lead and Pb-Al alloys with different contents of Al in 4 M H2SO4 at 25 °C.
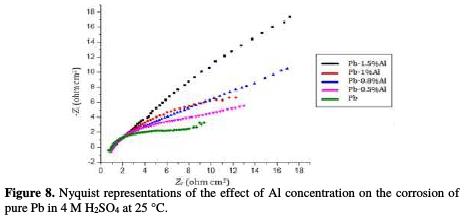
The charge transfer resistance Rt values (determined from the intercept of the semi-circle with the real part of the cell impedance at low frequencies) and those of the double layer capacitance Cdl at Ecorr = -536 mV/ECS are listed in Table 4.
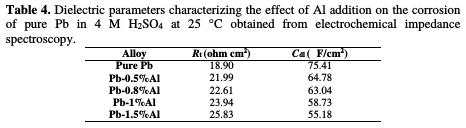
The Nyquist representations of Fig. 8 are in the shape of deformed semi-circles. This means that the main reaction mechanism present on the double layer is the charge transfer mechanism and that control of charged species by diffusion is absent [16-17]. By increasing the concentration of Al up to 1.5% in weight, we note that the diameter of the half-circles increases, indicating a strong resistance to corrosion in this margin of concentration. As it is indicated in Table 4, Rt increases from 18.9 to 25.83 ohm cm2 by adding only 1.5% in weight of Al, and the values of Cdl decrease from 75.41 to 55.18 μF/cm2, meaning that the corrosion rate of lead decreases and the lifetime of the battery increases. These results are in good agreement with those obtained by potentiodynamic polarization.
Fig. 9 gives the equivalent circuit of the measured electrochemical impedance spectroscopy, in which RS represents the resistance of the solution, C and R1 represent the capacitance and resistance of the double layer, and R2 and Q are the resistance and capacitance of the anodic film, where Q is a constant phase element (CPE) reflecting the dispersion effect of the film.
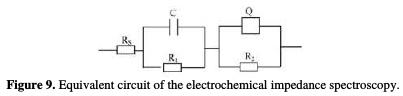
The real reason of the dispersion effect is not clear, but the inhomogeneous ion distribution in the film, ionic mobility, capacitance response, etc., may illustrate it [18].
The results of the electrochemical impedance spectroscopy represented in Fig. 10 and in Table 5 are in good agreement with those of the potentiodynamic polarization.
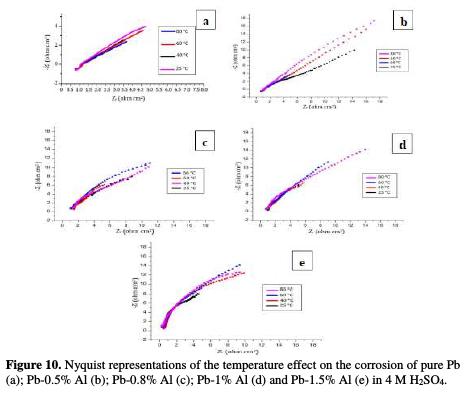
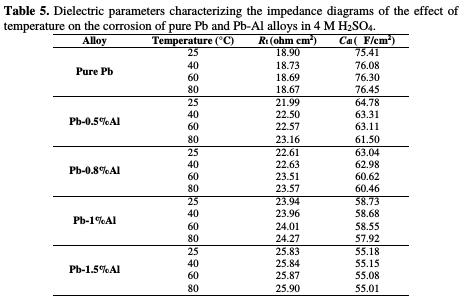
In the case of pure Pb, by increasing the temperature (from 25 oC to 80 °C), the charge transfer resistance Rt decreases (from 18.90 to 18.67 ohm cm2) and the capacity of the double layer Cdl increases (from 75.41 to 76.45 μF/cm2), signifying that whenever the temperature within the battery increases, the battery lifetime decreases. However, after Al addition, the charge transfer resistance Rt slightly decreases (from 25.83 to 25.81 ohm cm2 for Pb-1.5%Al) and the capacitance Cdl slightly increases (from 55.18 to 55.21 μF/cm2 for the same alloy). After aluminum addition, the increase in temperature within the battery ceases to have such a negative effect on the corrosion as in the case of pure lead.
Conclusions
The results of our work on the metallurgical and electrochemical effects of Al addition on lead in the lead-acid battery may be summarized as follows:
- Aluminum addition in contents not exceeding 1.5% Al led to an increase in the aluminum hardness (which was initially 5 HV) up to approximately 11.5 HV, meaning that the alloys are twice harder and more resistant than pure lead.
- Aluminum addition reduces the corrosion current density, Icorr, thus increasing the battery lifetime.
- Al leads to a decrease in the passivation current density, Ipass, as well as in passivity bearing size (especially for Pb-1% Al), meaning that Al facilitates the transformation reactions of PbO and PbSO4 into PbO2, which significantly reduces the lead-acid battery sulfation phenomena.
- The Pb-1.5% Al alloy proves to be the most resistant to corrosion, the battery lifetime being then be 51.15% times greater.
- The reaction mechanism that governs the metal surface is the charge transfer, as indicated by the deformed semi-circles shown by the electrochemical impedance spectroscopy.
- The temperature increases the corrosion rate of pure lead and consequently, decreases the battery's lifetime (to 16.96%). However, after aluminum addition, the negative effect of temperature decreases, and the battery's lifetime is not as reduced as with pure lead.
References
1. Bullock KR. J Electrochem Soc. 1979;3:360. [ Links ]
2. Abd El-Rahman HA, Salih SA, El-Wahab AMA. Materialwiss Werkstofftech. 2011;42:791. [ Links ]
3. Garche J, Doring H, Wiesener K. J Power Sources. 1991;33:220. [ Links ]
4. Meissner E. J Power Sources. 1997;67:135. [ Links ]
5. Osorio WR, Peixoto LC, Garcia A. J Power Sources. 2009;194:120. [ Links ]
6. Cekerevac MI, Romhanji E, Cvijovic Z, et al. Mater Corros. 2010;61:51. [ Links ]
7. Prengaman RD. J Power Sources. 2001;95:233. [ Links ]
8. Albert L, Chabrol A, Torcheux L, et al. J Power Sources. 1997;67:265. [ Links ]
9. Hong B, Jiang L, Hao K, et al. J Power Sources. 2014;256:300. [ Links ]
10. Yolshina LA, Kudyakov VY, Zyryanov VG. J Power Sources. 1999;78:87. [ Links ]
11. Khatbi S, Gouale Y, Lamiri A, et al. Port Electrochim Acta. 2016;34:393. [ Links ]
12. Hofmann W, Vibrans G. Lead and Lead Alloys. 1st ed. Berlin: Springer; 1970. [ Links ]
13. Boulahrouf JH. Mater Character. 1990;24:167. [ Links ]
14. Lander JJ. J Electrochem Soc. 1956;103:215. [ Links ]
15. Abd-El Rehim SS, Amin NH, Ali LI, et al. J Chem Technol Biotechnol. 1998;2:201. [ Links ]
16. Morakchi K, Hamel A, Zazoua A, et al. J Ren Ener. 2008;11:362. [ Links ]
17. Larabi L, Harek Y, Traisnel M, et al. J Appl Electrochem. 2004;34:839. [ Links ]
18. Li DG, Zhou GS, Zhang J., et al. Electrochim Acta. 2007;52:2152. [ Links ]
*Corresponding author. E-mail address: khatbisalma@gmail.com
Received July 31, 2017; accepted November 5, 2017