1. Introduction
1.1. Design for sustainability
Once an excellent solution for designing all kinds of products, plastic has become one of the most urgent problems to tackle currently. The material created to last is now, ironically, used for single-use purposes. Thirty-three per cent of all plastic - water bottles, straws and, most recently, unnecessary plastic packaging from e-commerce giants such as Amazon - is used once and thrown away (Plastic Pollution Coalition, n.d.). Plastic, however, will not biodegrade but breaks down into microscopic particles, contaminating the waters, threatening wildlife, poisoning food chains, affecting human health, the environment and costing billions to halt (Ibid.). Thus, there is an urgent need for plastic alternatives within the Design industry (Lockton et al., 2013).
The design process should include the state art of materials, and their most sustainable solutions should be identified. However, many times the design team has cost and time limitations and may not have all the solutions available. Nevertheless, material changes in the subsequent phases of production are more complex and expensive, delaying and compromising the final product. It is easier and less costly when available sustainable materials are intertwined with the design process. Therefore, materials experiments during the product design and fast prototyping allow easier changes and results. When considering closing the product life loop into a Circular Economy, the design process for each product element, assembling parts and machines available are the basis for identifying and evaluating the externalities. Once all the elements are defined, corrections can improve the sustainable product impact (Pfeifer, 2009). Therefore, bio-based materials reveal opportunities when considering a sustainable economy.
2. State of the art
2.1. Bio-based composites
Bio-based composites can combine two or more materials from a natural source: a reinforcing (e.g. fibres, particles) and a matrix (e.g. polymer, metal or ceramic). According to Saxena et al., soon, biodegradable polymers are expected to replace synthetics. Natural fibre composites are easily available, renewable, low-cost, lightweight and with specific strengths and stiffnesses. Bio-composites have received much commercial success in the semi-structural as well as structural applications (Saxena et al., 2011, p. 124).
Organic-based bio-plastic uses natural polymers from renewal biomass sources through polymerization reaction (Kipngetich & Hillary, 2012).
Green composites can be defined as bio-derived polymers reinforced with natural fibres; these might take on different properties and applications. According to Dicker et al., the main attribute of green composites "is their tendency to absorb water and degrade; a complementary application attribute would be limited exposure to moisture" (Dicker et al., 2013). Nevertheless, this material research study focused on hydrophobic properties to provide material longevity, resilience and applicability in 3D projects (e.g. pots, reusable packaging, tableware, furniture); (Sauerwein, 2020). Therefore, waterproof seaweed-based polymer (i.e. sodium alginate) was chosen, considering future studies can access raw material (both in Portugal and the Netherlands).
Seaweed in Europe, in North Atlantic and the Mediterranean, are used for varied purposes from food to bio-fertilizers. Depending on the size, they have named macroalgae or seaweed (i.e. benthic) or microalgae (i.e. planktonic) and be divided into three taxonomic groups: Chlorophyta (green algae), Rhodophyta (red algae) and Phaeophyceae (brown algae).
Seaweed presents an added value by neutralizing greenhouse gas emissions from factories, remediating wastewater and using CO2 as a nutrient source (Ferreira, 2014). Seaweed may be collected by mechanical harvesting, by boat, or manual depending on the species, allowing a simple, productive and eco-friendly industry with low investment (Radulovich et al., 2015). Another advantage of seaweed is the high growth rate (Kipngetich & Hillary, 2012, p. 11).
Brown algae contain Algins with a large amount of alginate used for many applications (e.g. biomedical, packaging, food, paper industry, textiles, wound dressing).
When crosslinked with calcium chloride, sodium alginate (the most common salt of alginate) generate strong gels that can be used and applied with different methods (e.g. solvent casting, extrusion, spraying). In addition, seaweed-based materials mechanical properties can be changed depending on the plasticizers: improving flexibility and resistance and reducing brittleness (Senturk Parreidt et al., 2018).
2.2. Organic Waste Fillers
Natural fillers can be classified depending on three sources: Plant, Animal and Mineral. The different sources were used for this study. Three waste fillers were used:
Chicken Eggshells from industrial by-products constitutes a severe environmental hazard. However, they contain up to 95% calcium carbonate and can be used as a value bio-filler for composites (Toro et al., 2007).
Shell sand is mainly formed from shells, barnacles, sea urchins, snails and skeletal calcareous algae. Natural shell sand takes a long time to be naturally created. Therefore, it can be considered a non-renewable resource (Norges Geologiske Undersøkelse, n.d.). Nevertheless, shells collected from the aquaculture and seafood industry provide a valuable biomaterial with environmental and economic benefits instead of waste resources (Morris et al., 2019).
Coffee Grounds the majority of the 7 million metric tons of coffee produced each year, goes to a landfill or is composted. Nonetheless, materials with coffee grounds can result in a biodegradable composite, light, with the smell of coffee.
See materials inspirations on fig.1, fig.2 and fig.3.
3. Methodology
3.1. Materials
The bio-composites with organic waste fillers were experimented with: used coffee grains, prepared egg shells (washed and hoven dried), Puik shells sand mixture for birds, sodium alginate, calcium chloride, glycerine, tap water, white vinegar and white sugar. Jars, pots, spoons, hand mixer, metal filter, stone mortar, stove, hoven and precision scale were used on the materials preparation.
The extruder parts were designed in Rhinoceros and printed in a Prusa 3D Printer with PETG, PLA and PLA/PHA (see fig. 6). Assembled with a syringe, 5V stepper motor and long threaded bolt with nut.
3.2. Methods
This project was done during one week for the 2020 Fabricademy assignment 'Open-source hardware: from fibres to textile', Textile Lab Amsterdam. Open-source hardware was used with bio-based materials to be extruded resourcing to a handheld 3D printer (Jongenburger, 2013).
A Qualitative and Quantitative Methodology was divided into parallel methods: the division allowed doing different tasks simultaneously, considering one-week assignment. Methods were: Literature Review; Design through Practice, Exploratory Ideation; Project Development; Prototyping and Assembling; Material Experiments with Sodium Alginate and fillers; Coding and testing.
The experiment recipes started from provided references (Bolumburu, 2018; Ferlatte, 2019; Kochhar, 2018). These were adjusted for appropriate usage of a syringe with an electric handheld extruder for 3D printing.
The research was developed for educational purposes within the Design field. Through direct observation, bio-based composites were analysed through: a) needed effort of handheld extrusion; b) through the solidity or liquidity; c) adaptation to the nozzle in use; d) their properties. Materials were photographed in two distinct phases: wet and cured and after the material was dried to observe shrinking and final characteristics (Table 1, in Appendices).
4. Development
Through Ideation, it was defined to develop a handheld extruder and bio-based materials to extrude. The class with six students from different backgrounds and nationalities was divided into identified tasks, according to personal skills and interests: Coding motor control + adapting 3D file; Sketches; Assembling the machine; 3D Printing; Materials recipes and Documentation. Although there was interaction during the project, the division allowed doing different tasks in parallel, considering one week as the timeline.
Google docs and drive were used for sharing all the created work. For quickly study results, a novel extruder was developed from a previous open-source 3D extruder model.
Several experiments with bio-composites using sodium alginate and organic waste as fillers were completed successfully and utilizing a novel handheld 3D printer, revealing feasibility (see fig.4 and fig.5).
Polymerization process: 1) Sodium alginate with glycerine as a plasticizer, tap water as a vehicle; fillers and stiffeners (e.g. eggshells, coffee grains waste; shells sand); 2) Moulding and Curing - spraying with Calcium chloride hydrated (10% solution); 3) Drying - in air and room temperature.
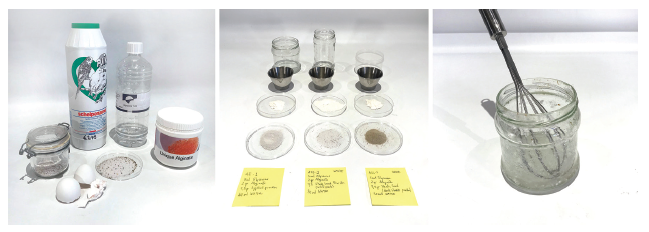
Fig.4 Ingredients prep - Eggshells, Shells sand, Sodium Alginate and Glycerine. Source: Fabricademy class 2020-2021.

Fig.5 Filtering oyster from shells sand-shell sand, 'white sand' and 'dark sand'. Source: Fabricademy class 2020-2021.
5. Analyses and Results
Most samples present opportunities as bio-based materials, although three recipes were chosen as final results by their specific characteristics: facility in extrusion on the handheld 3D extruder developed; fast curing process and materials aspects after two weeks drying.
A comparative sample with white sugar (for texture) was made and discard (although sugar soluble in waster could be tested for new results). Material was too stiff to be extruded and is not organic waste (code 10 SSS - Table 1, p. 5).
The shell sand appears like a strong composite with some minimal pores. It needs to be tested to confirm its waterproof behaviour (code 10 ASS-W8 - Table 1, p. 5).
Eggshells bio-based material created a ceramic result (code 12 AE - Table 1, p. 5). It needs to be tested with the most delicate eggshell powder to confirm the possibility of 3D moulds and extrusion. White eggshells can have more concentration of calcium. They resulted whiter and suggested a benefit when returning to nature (e.g. plants fertilizer; fodder for birds).
Coffee grains absorbed more moisture, resulting in a grained bio-plastic with a coffee aroma (code 13 AC - Table 1, p. 5). Depending on sodium alginate, water and glycerine, it can result in a more stiff composite or a flexible rubber or leather. The yarn extruded was fast to cure and dry, and flexible, while the 3D extruded in layers in the Petry dish resulted stiffer, suggesting that it loses more water after cured and dried.
6. Conclusions
In seashore countries (e.g. Portugal, Netherlands), shells sand reveal opportunities for treasuring waste as sustainable materials.
High calcium carbonate value on Eggshells waste gives particular resilience and physical attributes, of worth, for bio-ceramic composites.
Coffee grains bio-composite revealed plasticity and rubber appearance, relevant for vegan leathers or packaging. These have potential interest for future studies: collecting waste on city coffee shops and scaling up bio-based products.
The three elected experiments revealed that could be classified different accordingly to characteristics: shell sand bio-composite (see fig.8b); eggshell bio-ceramic (see fig.8b); and coffee grain bio-plastic (see fig.8c);.
In conclusion, using natural waste for bio-composites allow easy reproduction, testing and improved results. Furthermore, using open-source bases promotes worldwide collaborative learning and research towards a sustainable approach (e.g. social and economic).
Organic wastes as fillers suggest low shrinkage when comparing after extrusion with curing, with after dried results.
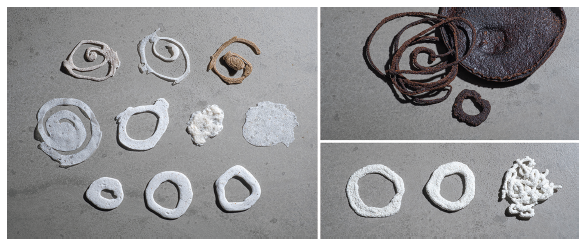
Fig.7 Bio-based composites extruded clockwise: a) Shell sand; b) Coffee grains experiments; white Eggshells. Source: Fabricademy class 2020-2021.
Acknowledgements
This work is financed by national funds through FCT - Fundação para a Ciência e a Tecnologia, I.P., under the Strategic Project with the references UIDB/04008/2020 and UIDP/04008/2020, and by PhD Research Scholarship FCT 2021.04708.BD.
The authors gratefully acknowledge TextileLab Amsterdam - Fabricademy collaboration.