Introduction
The replacement of missing teeth is essential to restore oral functions, such as masticatory, phonetic, and aesthetic.1 Removable partial dentures (RPDs) are a cost-effective treatment, making them an important alternative to fixed dentures.2 However, the clinical success of RPDs depends on various mechanical functions, including stability, support, retention, and reciprocity, which in turn are influenced by the fit accuracy of their framework.3,4
Cobalt-chromium (Co-Cr) alloys are still the most popular materials used to produce RPD frameworks due to their ideal mechanical properties, such as high yield strength, low elastic modulus, and high corrosion resistance.5,6 For decades, RPD metal frameworks were produced through the lost-wax technique, which involves many laboratory procedures prone to human errors and material distortions.1
With computer-aided design and computer-aided manufacturing (CAD-CAM) technology, it becomes possible to overcome many disadvantages of conventional techniques.7 Some of the well-known advantages of CAD-CAM, in comparison to traditional production techniques, are an efficient use of material with waste reduction; simplification of the procedures with less labor time; capacity for multiple productions at the same time; reduction of the operator variability with the elimination of multiples steps prone to human errors; and higher predictability and reproducibility.8 According to our knowledge, the application of CAD-CAM techniques to produce an RPD metal framework was firstly presented in 2004.9 Since then, few clinical studies have evaluated the influence of digital technology on the RPD’s fit accuracy, despite the growing digital laboratory developments.10
The purpose of this clinical study was to assess the influence of a CAD-CAM production protocol on the clinical fit accuracy of RPD metal frameworks to the supporting tooth structure.
The null hypothesis tested was that the production protocol does not influence the clinical fit of RPD metal frameworks.
Material and methods
The study protocol was approved by the Ethics Committee for Health of the Faculty of Dental Medicine of the University of Lisbon (FMDUL). Fifteen patients of the university’s dental clinic were selected by convenience from those who needed RPD rehabilitation, according to the following inclusion criteria: age over 18 years; at least one premolar or molar as a prosthetic abutment; absence of metal allergy; absence of active dental caries or grade II or III tooth mobility in the prosthetic abutments; absence of other oral lesions. All patients voluntarily signed a written informed consent agreement.
A total of twenty dental arches (n=20) were prepared after an evaluation of the study stone casts (Elite Model, Zhermack GmbH, Germany) obtained by pouring the primary alginate impressions (Orthoprint, Zhermack GmbH, Germany). Subsequently, secondary impressions were recorded using alginate impression material (Hydrogum 5, Zhermack GmbH, Germany) and individual trays and then poured with type IV plaster (Elite Rock, Zhermack GmbH, Germany) to achieve master stone casts. From each master cast, two cobalt-chromium RPD frameworks were produced with two different protocols: a CAD-CAM protocol (experimental group) and the conventional lost wax casting protocol (control group) (Figure 1).
In the experimental CAD-CAM group, each master cast was digitized with a laboratory scanner (S600 Arti, Zirkonzahn GmbH, Italy). The Partial Planner software (Zirkonzahn GmbH, Italy) was used to digitally analyze the insertion axis and design the RPD framework, creating an STL file that was sent to a laboratory center production (Sineldent®, Spain). The RPD metal framework was directly produced by the direct metal laser sintering (DMLS) technique, using a cobalt-chromium SP2 alloy (EOS GmbH, Germany) and the EOSINT M270 equipment.
The metal framework was then submitted to a heat treatment for 45 minutes to improve its mechanical properties.
In the control group, each master stone cast was duplicated to a refractory cast, and wax patterns were positioned to reproduce the RPD framework design. The created patterns were eliminated in an oven (Infinity L30, Jelrus, USA), and then the cobalt-chromium alloy (Remanium G 380+, Dentaurum GmbH & Co. KG, Germany) was injected using an induction casting equipment (Ducatron Quattro, Ugin Dentaire, France).
A single technician applied equal finishing and polishing methods in both groups, using the same master cast for testing.
Hand drills and rubbers were used for finishing, followed by immersion in an electrolytic bath (Polytherm compact, Dentaurum GmbH & Co. KG, Germany) for 3 minutes. Brushes and paste were used for the final polish.
Each RPD framework was adjusted until the correct fit to the supporting oral structures was achieved. After that, the fit accuracy of the framework occlusal rests to the corresponding rest seats of the abutment teeth was assessed by an indirect quantitative digital method.
The evaluation was performed with a silicone mold (V-Posil Light Fast set, Voco GmbH, Germany) of the gap between the framework occlusal rests and their respective rest seats. To avoid pores in the molds, the rest seats were previously dried with a dental-chair air tip, and the silicone was injected using an applicator and mixing tips. In addition, after the application on the rest seats, the silicone was vibrated with a finger. Next, the metal framework was inserted and, pressuring the occlusal rests using the fingers, the polymerization of the silicone was done. The obtained silicone molds were trimmed by removing the exceeding material with a scalpel blade, and the resulting specimens were individually digitized using micro-computed tomography (micro-CT) equipment (Skyscan 1174, Bruker, Belgium) (Figure 2). An orthodontic wax (Protection wax, Dentaurum, Germany) was used to stabilize the silicone specimens during the digitization. The scans were performed with 50 KV, 800 μA, 6.6 μm of image, 5500 ms of exposure, 0.9 of rotation step, and no Al filter. The software used for reconstruction, three-dimensional (3D) registration, and morphometric analysis were NRecon (Bruker, Belgium), DataViewer (Bruker, Belgium), and CTAn (Bruker, Belgium), respectively.
The projection images initially reconstructed with the NRecon software were uploaded in the DataViewer software, and the datasets of the silicone specimens were then reoriented.
A 3D registration with overlapping of the silicone specimens was done using their counterpart as a reference, and the same VOI (volume of interest) was defined for reference and target datasets (Figure 3). After segmentation, the mean thickness and the mean volume of the selected fraction of each specimen were calculated, respectively, in micrometers and cubic micrometers, using the CTAn (Bruker, Belgium). The final thickness and volume data were obtained using the mean thickness and volume values of all silicone specimens assessed per framework (Figure 4). The same investigator, previously submitted to a training and calibration period, performed the fit accuracy evaluation of all RPD metal frameworks.
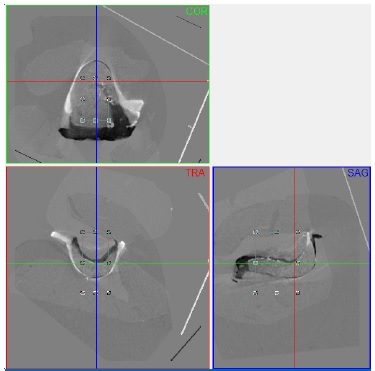
Figure 3 3D registration and analysis of two corresponding silicone molds after digitization by micro‑CT, by overlapping of the datasets using the same VOI in the DataViewer

Figure 4 2D measurement of the mean thickness of a transversal segment of a silicone mold, after segmentation and mean thickness and volume calculation, in the CT‑Analyzer
The collected data were analyzed (IBM SPSS, v.25) using a Shapiro-Wilk test to confirm normal distributions (p>0.05), a paired t test for the silicone thickness data, and a Wilcoxon test for the silicone volume data (α=0.05).
Results
The results obtained are presented in Table 1. The thickness mean values of the silicone specimens were 309.8 ± 112.57 μm for the conventional protocol and 333.4 ± 115.44 μm in the CAD-CAM group. In turn, the volume mean values of the silicone specimens were 5.4x108 ± 4.00x108 μm3 for the conventional protocol and 6.0x108 ± 3.34x108 μm3 in the CAD-CAM group. No statistically significant differences in silicone thickness (p=0.441; paired t test) (Figure 5) and silicone volume (p=0.204; Wilcoxon test) (Figure 6) were found between the two production protocols.
Table 1 Fit accuracy results for thickness (μm) and volume (μm3), considering the production protocols (n=20)
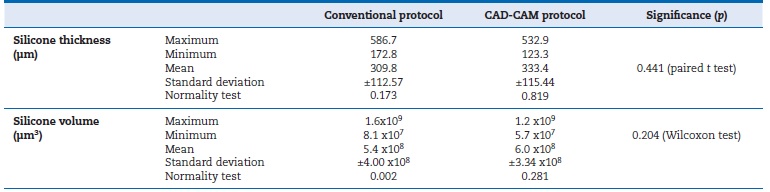
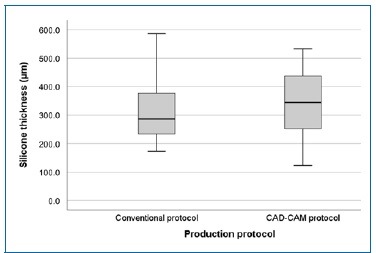
Figure 5 Box plots of the silicone thickness values (in micrometers) for the two production protocols under study. No statistically significant differences (p=0.441; paired t test) were found between groups
Discussion
There are several descriptions of methods to assess the fit accuracy of the RPD metal frameworks in the literature. Considering their importance for the stability and function of RPD, the occlusal rests are the most evaluated component.10-13Although no method can be considered the gold standard, quantitative data acquisition enables a more detailed and precise evaluation than qualitative information.10 Qualitative methods like direct visual inspection or pressing test on occlusal rests provide limited information and are prone to human subjectivity.9,10,14,15An inspection using a calibrated wire is a more objective qualitative method but still provides limited information.16
Regarding how information is collected, the fit accuracy assessment methods can be direct or indirect. Although a direct quantitative assessment can provide higher trueness, it may not be applied to a clinical evaluation (for instance, the gap measurement by microscopy after the cut of the structures) and may involve patient radiation (for instance, the digital measurement after structures digitization by computed
tomography techniques) or the match of different scanners by a computer algorithm (for example, the digital measurement after structures digitization by an intra-oral scanner).17-19
The indirect assessment of the fit accuracy of RPD metal frameworks applied, using silicone molds of the gap between occlusal rest and the respective rest seats, preserved the integrity of the structures and had already been considered by many authors as a reliable technique.1,10-12 Compared to other substrates, as acrylic, the addition silicone (V-Posil light Fast set, VOCO) has greater reproduction detail, radio-opacity, resistance, flexibility, and tolerance to taste.1,10,12,20
In the present study, the measurement of the thickness and volume of the silicone specimens was made by micro-CT technique due to its advantages to other analog or digital measurement techniques (for example, methods using gauges, microscopes, or scanners), such as specimen preservation, high-resolution power, high precision, simple methodology, specimen digitization by just one scan, and the ability to measure the total thickness and simultaneously the volume of the specimen.1,10-12,21-23
No differences in thickness and volume were found between the two groups of frameworks, so the null hypothesis could not be rejected. These findings are in line with the results of a previous laboratory study,1 whose authors also did not declare differences in the fit accuracy of RPD metal frameworks produced by a similar CAD-CAM protocol with those produced by a conventional protocol.1 However, a clinical study10 demonstrated better results with the conventional protocol compared to the CAD-CAM protocol. These results can be explained by differences in the experimental design and by the different indirect quantitative assessment methods used, namely, evaluating silicone specimens that were cut in slices and measured in specific points by optical microscopy.
In the present study, to avoid different distortions, the same master stone cast was used to produce both protocols, in opposition to two master stone casts (one for each protocol) used in the previously mentioned clinical study.10 In addition, despite the use of the same production equipment (EOSINT M270) in the two studies, different cobalt-chromium alloys were used: instead of Wirebond C+,10 our study used the EOS SP2, known to create structures of high density, strength, and biocompatibility.7
The measurement of the gap volume by application of micro-CT techniques was an innovative approach. Compared to other methods, the evaluation of the gap volume allows a more concrete interpretation of the 3D maladjustment between two structures. However, considering the definition of the segmentation value, despite being a reference in relative measurements, the micro-CT technique requires special attention in absolute measurements.24
Other limitations of this study include the maintenance of the metal framework in the correct oral positioning during the polymerization of the silicone and the stabilization of the silicone molds in the orthodontic wax before the micro-CT digitization. To overcome the difficult standardization of these steps and avoid bias, the same investigator executed these procedures after a period of training and calibration.
In addition, the VOI was always selected after the registration to exclude areas where the silicone molds were bent or had a pore.
Notwithstanding the complexity and the obstacles of clinical investigations on this topic, more studies with larger samples are needed to confirm the viability of the proposed CADCAM protocol.
Conclusions
Considering the obtained results and the limitations presented, this study concludes that there are no differences in the clinical fit accuracy of RPD metal frameworks between the two production protocols studied. In addition, considering the well-known benefits of digital technology, this research suggests that the proposed CAD-CAM protocol is a viable method for RPD metal framework production. However, further studies with a larger sample and other variables are needed to confirm this suggestion.