Introduction
IN 718 Ni-based SA is known to possess higher tensile strength, excellent creep resistance, low-cycle fatigue strength, good formability and weldability 1-10. Hence, it is often chosen as a good alloy, to be used for high speed machinery shafts. However, it has been found that IN 718 is pronouncely affected by frictional wear during itsapplicationthis SAdue to its difficulties during machining. In fact, IN 718 is widely known to have poor thermal conductivity, work hardening high rate, high ( and chemical affinity towards cutting tool materials 11-15. All these inherent properties not only are problematic to the machining processes, but also render this SAsusceptible to inferior mechanical properties, corrosion and frictional wear during its applications.
In an endeavour to improve IN 718 corrosion, surface and mechanical properties, at elevated temperatures 16, we doped it with GrNs. From the engaged methods and analyses, higher ( values were obtained. Furthermore, less reduction of the young modulus values occurred during high temperature oxidation. PDP curves also showed more electropositive Ecorr and lower Icorr values for the modified IN 718. Most notably, GrNs, ( and EIS measurements showed a strong oxide layer that is more corrosion mitigative. Likewise, morphologies showed no localized corrosion under all conditions. All those features proved that IN 718 doping by GrNs played a significant role in improving its corrosion resistance, mechanical and surface properties 17. Nonetheless, frictional wear analyses were not conducted.
Hence, the present study investigated and reported on the modified IN 718 tribological performance, which was fabricated by selective laser melting. Investigations were made on wear and frictional properties, under room temperature. Surface morphologies were also incorporated into the tribological impact. All comparisons were made the IN 718 standard.
Experimental
Hardness and modulus of elasticity measurements
Mechanical properties were clarified from ( and young modulus analyses. The ( depths were measured using ASTM E384-05 criterion that is described elsewhere 18. Young modulus tests on both bare and coated foils were carried out following EN 10002-1 measurement guide lines, and they were performed by an Instron 3384 testing machine.
Surface characterizations
SEM was used to examine the surface morphologies, while XRD was used to determine the oxides phases that were formed during the tribological tests.
Tribological set-up and measurements
Friction and wear properties of bare and nano-coated foils were studied by a RTEC2441 (s/n :, USA) universal tribometer. The measurements were at room temperature. The tests were run under dry lubrication conditions that are explained further ahead. A steel ball was used as the counterpart material against both standard and modified materials. The diameter size of the steel ball was 1.50 mm, and the acquisition rate was 3.14 Hz, with an equivalent stroke length of 6 mm. The measurements were intended to incorporate friction and wear properties from both pure and modified IN 718.
SWRs and AWIs
AWIs and SWRs calculations were carried out from equations 1 and 2.
where: MB and MC are the mass loss from the bare and coated foils, respectively; DC and DB are the density of the coated and bare foils, respectively; and WRB and WRC are the total number of wheel revolutions during the tests on the bare and coated foils, respectively.
where V is the velocity (m/s); F is the force (10 N); L is the total sliding distance; and m and ƿ are the engaged material mass loss and density, respectively.
Results and discussion
Hardness and modulus of elasticity measurements
Fig. 1 shows the mechanical properties of both pure and modified IN 718. As it can be seen in Fig. 1, pure IN 718 has lower ( and younger modulus values than those of the modified one. Confirming the mechanical properties criterion that generally recognizes improvement of materials possessing higher ( and modulus elasticity values 20-25, the incorporated GrNs provided better tribological properties.
Tribology measurements (wear and friction)
SWR and AWI rate
Overall wear analyses on both pure and modified IN 718 are displayed in Fig. 2 and 3. As it can be seen in Fig. 2, AWI is much higher for the modified IN 718. On the other hand, pure IN 718 had higher SWR than that of the modified one, as it can be seen in Fig. 3, which suggests better tribological properties of the modified IN 718 26-30.
Analyses of µ
The µ analyses on both pure and modified IN 718, in a progression of time under no loads and several , are shown in Figs. 4 and 5. As it can be seen in Fig. 4, an increase in the load rapidly affected the oxide layer and µ on the pure IN 718 surface. Furthermore, an occurrence of a running-in period is swhon n Fig. 4 (i and iii), whichcould be due to an interlock of asperities between IN 718 and the steel ball from the tribometer 31. In Fig. 4 (ii), it can be seen that µ starts by decreasingis phenomenon is called transient period, during which IN 718 was suspended in a space where it was smoothed before its oxide layer was transferred to the steel ball. As time went by, minor fluctuations occurred on the oxide layer formed under no load conditions. However, as the load was increased, major fluctuations occurred on pure IN 718.
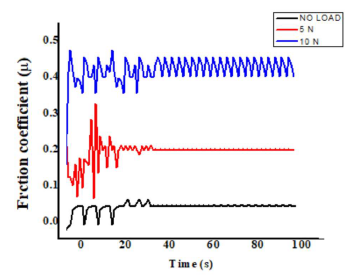
Figure 4 µ of pure IN 718 under no load and several low loads (5 to 10 N), in a progression of time.
The running-in period was also observed on modified IN 718, as it can be seen from Fig. 5. Nevertheless, µ was lower under all conditions. An improvement observed on the modified IN 718 was due to Gr oxidation, which gave a better structural strength to the SA, thus improving its load carrying capacity 32,33. An increase inthe load was also found to have caused flutuations on the steady-state condition of the oxide layer, during the modified IN 718 tribological measurement. There are normally two factors that could lead to aggressive tribological conditions, as the load increases: a friction-induced thermal effect during sliding, under high loads 34; and an increased contact between the rubbed surfaces, which was excerbated by the higher load 35 36. Therefore, it was the cushion formation of an oxide layer that acted as buffer (immunity), detering IN 718 surface wear.
SEM analyses
SEM micrographs for the engaged substrates, before tribological measurements, are shown in Fig. 6, while the ones captured after tribological measurements are shown in Figs. 7 and 8.
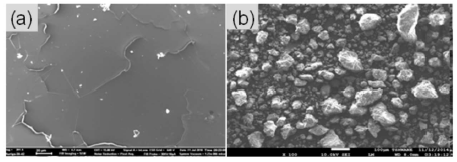
Figure 6 Surface morphologies on IN 718: (a) bare; (b) and modified, before tribological measurements 18.
Shallow inclusions and voids, under no load conditions, on pure IN 718, can be seen in Fig 7 (a). As the load was increased to 5 N, ploughs, voids and pores were discovered on pure IN 718 surface, as it can be seen in Fig. 7 (b). At the load of 10 N, tracks were discovered on its surface, which can be seen in Fig. 7 (c).
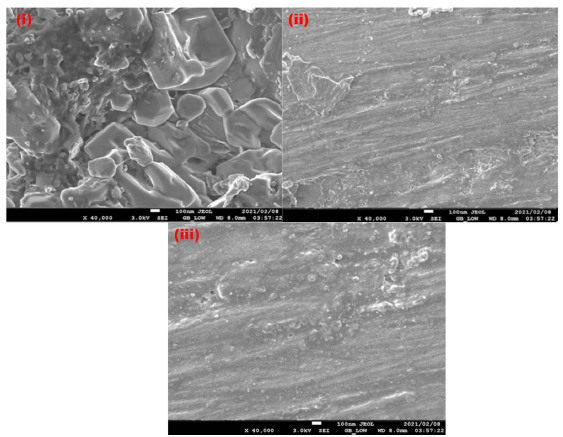
Figure 7 Surface morphologies on: (i) pure IN 718 under no load; (ii) 5 N applied load; and (iii) 10 N applied load, in a progression of time.
Contrarily, micrographs of a smooth oxide layer can be noticed on modified IN 718 surface, which are Fig. 8 (a). At an applied load of 5 N, shallow fine grooves were noticed. The corresponding scan is shown in Fig. 8 (b). With the increase in load to 10 N, shallow ploughs were found on its surface, as it can be seen in Fig. 8 (c). SEM analyses, herein, corroborate the earlier results on SWR and µ coefficient. This observation, therefore, strongly suggests that GrNs incorporation into the IN 718 provided improved mechanical properties and a tribological oxide layer which lowered the frictional wear.
Conclusions
The tribological characterization of both pure and modified IN 718 has throughly been investigated in this study. The following conclusions were drawn up from the main findings:
Modified IN 718 possessed higher ( and younger modulus values.
Pure IN 718 had relatively lower AWIs. Contrarily, higher AWIs and lower SWRs were discovered for the modified IN 718.
Lower µ values were noted, under all the conditions, on the modified IN 718. However, an increase in the load proved to affect the tribological oxide layer of both pure and modified IN 718.
Shallow inclusions and voids were not noted in the pure IN 718 morphologies, under no load condition, while voids and pores were discovered for an increased load of 5 Nthe SA. Moreover, micrographs of wear tracks were noted at 10 N applied loadIN .
Contrarily, micrographs showed a smooth oxide layer formed on the modified IN 718 surface, under no load condition. With an increase in the loads to 5 and 10 N, shallow fine grooves and shallow ploughs, respectively, were noticedthe modified SA.
Generally, GrNs incorporation into IN 718 provided improved mechanical properties and a tribological oxide layer, which lowered frictional wear.
Acknowledgement
We would like to thank DAAD/NRF for funding this study, and Powerkote (PTY) LTD for availing the foils for the research.
Declaration
This study was funded by the German Research Exchange (DAAD/NRR in Country), and the materials used were supplied by Powerkote. There are no conflicts of interest towards the submission of this manuscript. However, some information remains as intellectual property (IP) from Powerkote. Hence, the coating materials have not been disclosed. Data and software used in the application of nanocomposites on the foils remains confidential. All parties involved in this work are consenting and aware of the publication of this work. Most importantly, all ethics were mandatorily obeyed.
Authors’ contributions
Khotso Khoele: conceived and designed the analysis; collected the data; performed every analysis; inserted the data or analysis tools; wrote the paper. Onoyivwe Monday Ama: contributed with the analysis of the results; edited the work on data and inserted analysis tools. David Disai: edited the work at certain parts. David Jacobus Delport: designed the analysis; contributed on the paper writing. Suprakas Sinha Ray: made overall editing of the work; provisioned equipment for the characterization of the samples.
Abbreviations
AWI: abrasive wear index
Ecorr: corrosion potential
EIS: electrochemical impedance spectroscopy
GrNs: g
Icorr: corrosion
IN 718: Inconel 718
IN 718 + GrNs: modified IN 718
Ni: nickel
PDP: potentiodynamic polarization
SA: super alloy
SEM: s
SWR: specific wear rate
XRD:X-ray diffraction
Symbols definitions:
µ: friction coefficient
(: hardness